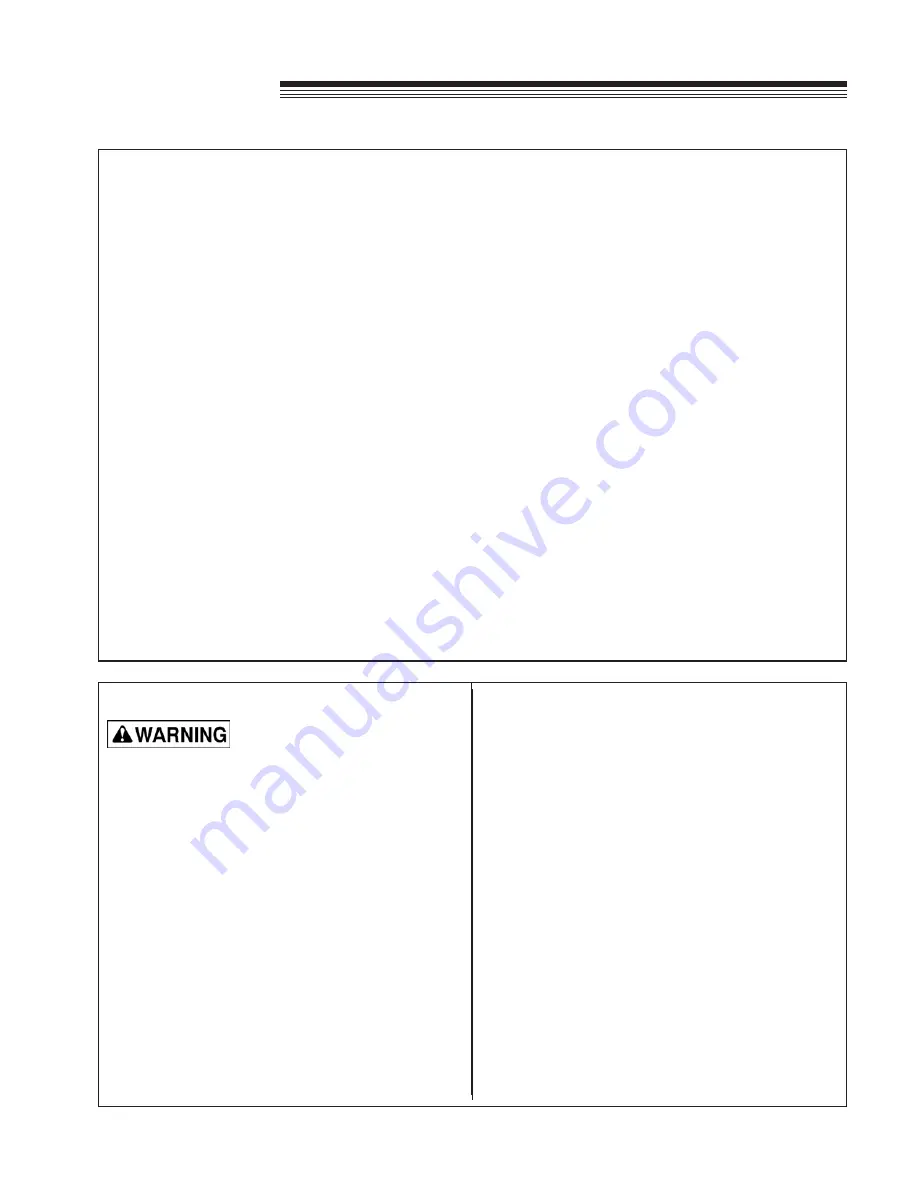
23
XRZ
CHECK DAILY
Operator Presence Interlock System - Start Operation
For the engine to crank, the parking brake must be on, the PTO (blades) off and traction levers in the neutral
lock position. Sit in the seat and check, one by one, if the engine will crank with the parking brake off, the
blades on, and either traction lever out of neutral lock.
Operator Presence Interlock System - Run Operation
The operator must be in the seat for the engine to run with the parking brake off, the traction levers moved out
of the neutral lock position, or the blades on. To check:
1. Start the engine and run at 1/2 throttle with the operator on the machine but raised off the seat.
2. One by one: move the parking brake to the OFF position, traction levers out of the neutral lock position
(check each independently), and turn the blades on. Each check should kill the engine after 1/2 second.
(A 1/2 second delay is built into the system to prevent engine cutout when traversing rough terrain.)
Repair machine before using if the Operator Presence Interlock System does not operate correctly in start or
run. Contact your authorized Schiller Grounds Care, Inc. dealer.
Hardware
Tighten any nuts and bolts found loose. Replace any broken or missing cotter pins. Repair any other prob-
lems before operating.
Tire pressure
Rear tires should be kept inflated to 12 lbs/in
2
(0.8 kg/cm
2
). Front tires should be kept inflated to 15 lbs/in²
(1.05 kg/cm²). Improper tire inflation can cause rapid tire wear and poor traction. Uneven inflation can cause
uneven cutting. Over inflation of caster tires can cause casters to "wobble" on hard surfaces.
MAINTENANCE
BATTERY-
AGM TYPE BATTERY SUPPLIED
Battery acid is caustic and fumes
are explosive and can cause serious injury or death.
Use insulated tools, wear protective glasses or
goggles and protective clothing when working with
batteries. Read and obey the battery manufacturer’s
instructions.
Be certain the ignition switch is OFF and the key has
been removed before servicing the battery.
1. Verify battery polarity before connecting or discon-
necting the battery cables.
2. When installing the battery, always assemble
the RED, positive ( + ) battery cable first and the
ground, BLACK, negative ( - ) cable last.
3. When removing the battery, always remove the
ground, negative ( - ) cable first and the red, positive
( + ) cable last.
4. AGM type battery.
Use AGM charger when
charging. P/N 4171973
5. Clean the cable ends and battery posts with steel
wool. Use a solution of baking soda and water
to clean the battery. Do not allow the solution to
enter into the battery cells.
6. Tighten cables securely to battery terminals and
apply a light coat of silicone dielectric grease to
terminals and cable ends to prevent corrosion.
Keep terminal covers in place.