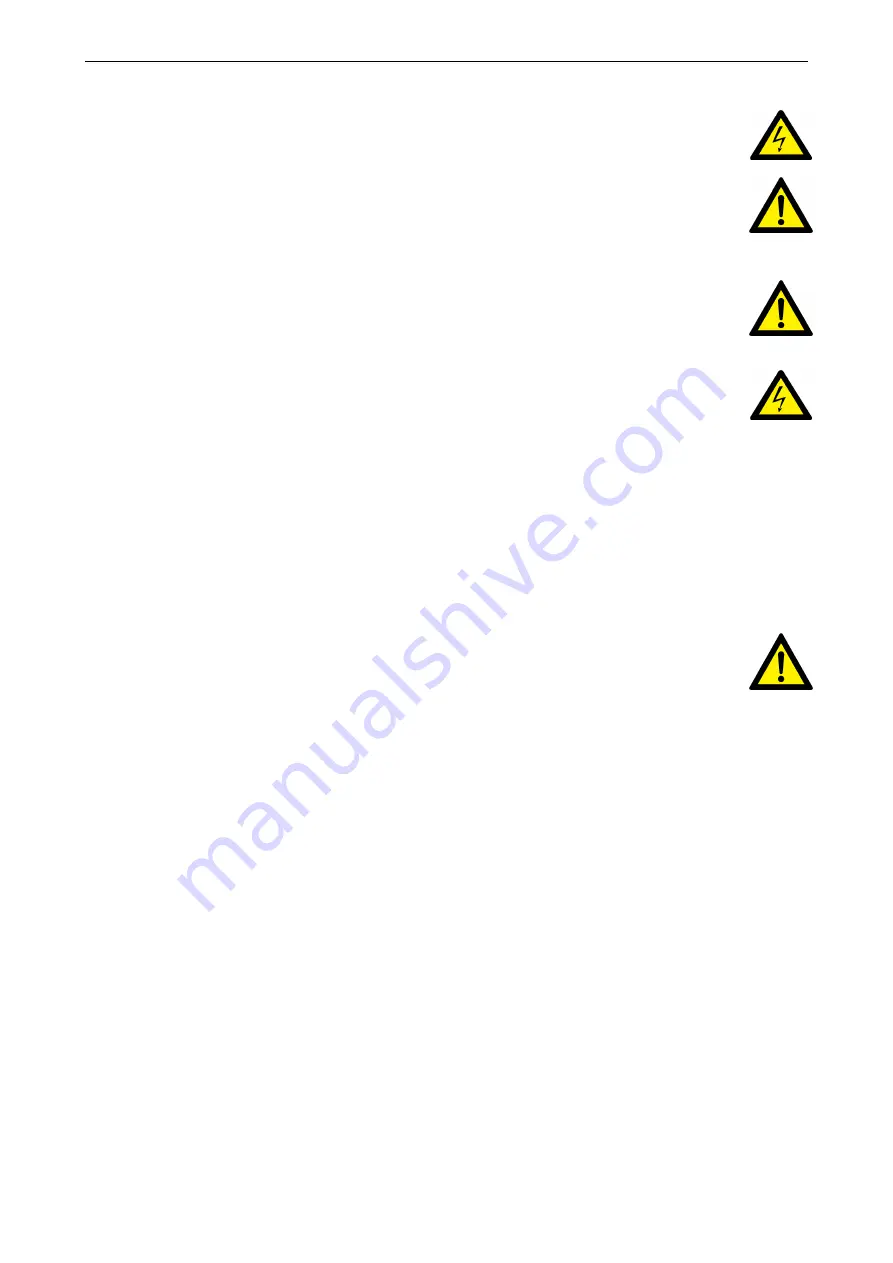
Operating Manual Linear ACTUSAFE CMFS(L)
OM-ENGLISH-Failsafe-Linear-16xx-V2.00-2022.03.03
9 Maintenance
9
Maintenance
WARNING: All maintenance work may only be performed with the actuator disconnected from the power
supply.
CAUTION:
Due to this requirement, the actuator has to be in the failsafe position!
NOTE:
If this is not the case, it may be because of a fault in the fitting (stuck valve stem).
WARNING: The actuator has a pre-loaded coil spring or a disk spring assembly! When loosening the
flange mounting bolts, the spring force against the valve can cause the actuator to come loose from
the valve. Adequate safety measures must be taken.
WARNING: Any powering up must be ruled out during maintenance! Work on the electrical systems or
components may only be carried out by electricians or by individualswho have been instructed how to
do so, working under the guidance and supervision of an electrician in accordance with electro techni-
cal regulations.
After completing their commissioning, the actuators are ready for use. The actuator is filled with oil as standard when
shipped.
Routine checks:
• Be mindful of increased running noises. In cases of long down times, operate the actuator at least every three
months.
• Check the failsafe function (check the operating time and smoothness of running in failsafe operation). Lengthening
in the running time may also be caused by an increased torque requirement for the fitting after long down times.
WARNING: The actuator has a pre-stressed coil spring or disk spring assembly. Improper dismounting
may lead to both damage to the actuator as well as serious injuries! If maintenance work is needed re-
quiring the actuator to be dismounted, contact SCHIEBEL Antriebstechnik GesmbH regarding detailed
instructions and/or any special-purpose tools for relaxing the spring assembly!
The actuators are designed for any mounting position (See section 2.5, page 24), which is why there is neither a filling level
indicator nor a drain plug on the main casing.
Depending on the stressing subjected to, do the following approx. every 10,000 to 20,000 hours (about 5 years; see
section 15, page 76):
• Oil change
• Replace seals
• Check all the roller bearings and the worm gear assembly and replace if necessary.
Take the types of oils and greases to be used from our Lubricant Table. (See section 15, page 76).
NOTE:
Check the cable glands at regular intervals (annually) for tightness of the cables and retighten if necessary.
If the visual inspection (eg. dust or water penetration) indicates that the effectiveness of the Sealing elements of the
cable entry has suffered damage or aging, such elements have to be replaced preferably by using the original spare parts
from the manufacturer of the equipment or through cable entries of comparable quality as well as the same ex- or IP
protection class.
19