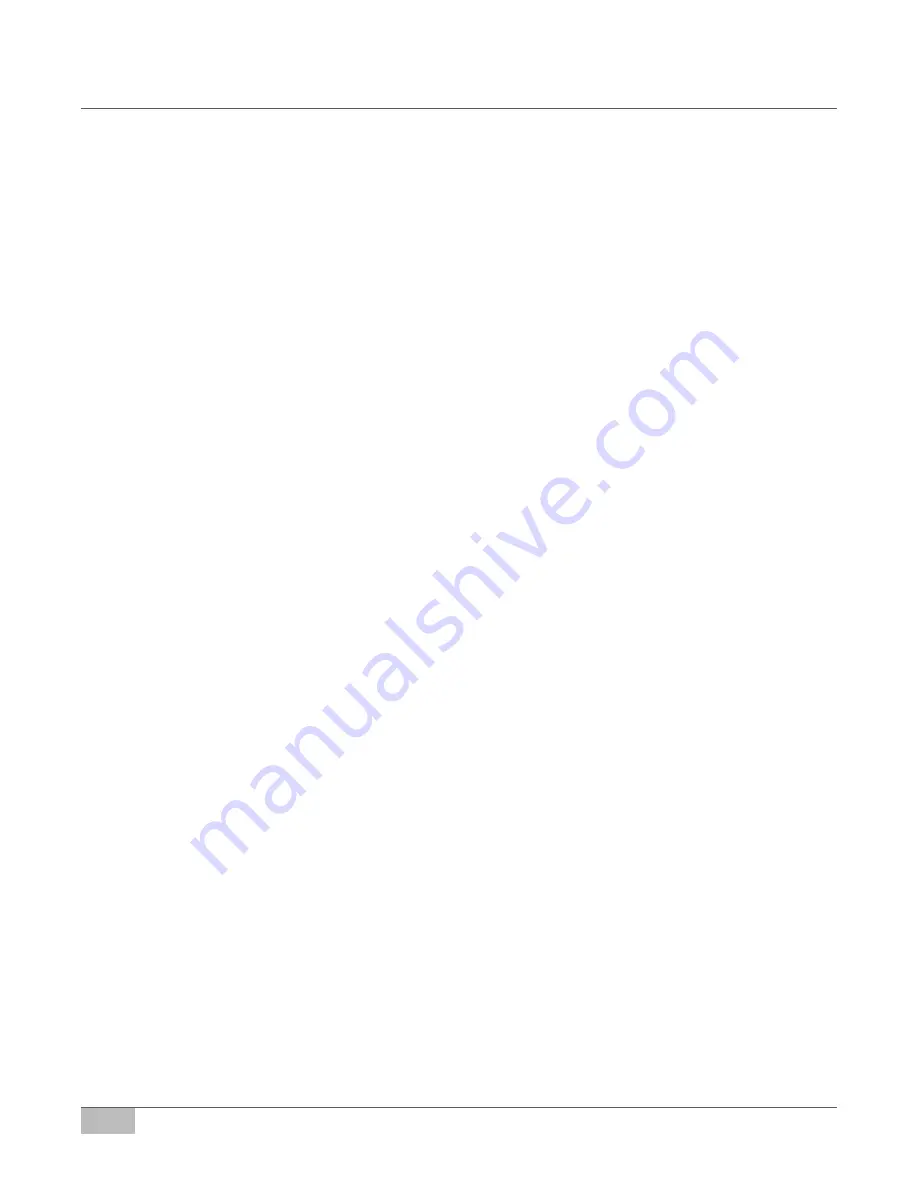
- 28 -
User Manual | 03.2021 | v04
www.schaererusa.com
Warranty Information
The service technician will make an on-site assessment of whether or not a repair is covered under warranty. If
the customer has questions about warranty coverage or disputes the technician’s decision that a service call is
not covered under manufacturer’s warranty, please contact SEB Professional North America at 888.989.3004 to
discuss warranty coverage.
Customer Care Visit
One optional Customer Care Visit shall be included. This visit shall be scheduled in or near the 2nd quarter and
need to take place during normal business hours. SEB Professional North America will coordinate scheduling
through its Service Partners. In the event that the store or site does not make itself available for the visit, SEB
Professional North America reserves the right to void its obligation toward the visit. The Customer Care Visit is
optional SEB Professional North America is under no obligation to full fill the visit unless otherwise specified and
agreed upon both parties (the customer and SEB Professional North America).
SEB Professional North America is entitled to utilize customer-initiated service visits to perform the customer care
visit inspection, should one occur during or near the respective customer care visit dates.
Components/Parts Covered Under Warranty
The following major internal components are covered under this contract:
Control
Board
PC-Board
Pump
Head
Pump
Motor
Flow
Meter
Brewing
Unit
(Automat)
Brew
Valve
Tea
Valve
Temperature Probe (internal damage)
Water Boiler
Grinders Grinder
Motors
Brew Group Drive Motor
Transformer
Card
Reader
Display
(internal
damage)
Air Pump
Position switches (internal damage)
Warranty Exceptions
Examples of components NOT covered under this contract, excluding manufacturer defects:
Paneling
(Shell)
Bean
Hoppers
Cup
Warmer
Plate
Drip
Tray
O-rings
Product
Buttons
(external
damage)
Coffee
Spout
Display
(external)
Grinder Blades (normal wear and tear)
Hot Water Spout
Chip
Cards
Examples of major component malfunctions NOT covered under manufacturer’s warranty:
• Any valve that is clogged or damaged by calcium or other solids/deposits.
• Any sensor is covered with calcium or other solids/deposits.
• Any boiler filled with solids/deposits that needs to be replaced.
• Any damage due to cartridge residue reaching the machine because it was not flushed properly.
Examples of operator error, misuse, abuse, neglect, lack of cleaning, etc., issues that are NOT covered under
manufacturer’s warranty:
• Clogged brew group/automat due to lack of cleaning.
• Any clogging of the drip tray or cracks in the drip tray.
• Foreign objects (coins, small stones, plastic objects, etc.) in the grinders.
• Position switches, inside the automat/brew group area.
• Calibration complaints (beverage volume and temperature) based on measurements not following the
correct measuring procedure.
• Main waterline being turned off.
The terms and conditions of this contract are valid for the current program period only. The examples listed above
do not represent an exhaustive list of the errors that might be encountered. They are examples only. Terms and
conditions of this contract are subject to change.
Summary of Contents for 040381-00051EUS
Page 16: ...16 User Manual 03 2021 v04...
Page 22: ...www schaererusa com Maintenance Hopper Cleaning 22 User Manual 03 2021 v04...
Page 26: ...26 User Manual 03 2021 v04...
Page 29: ...29 User Manual 03 2021 v04 www schaererusa com Notes Notes...
Page 30: ...30 User Manual 03 2021 v04 www schaererusa com Notes Notes...