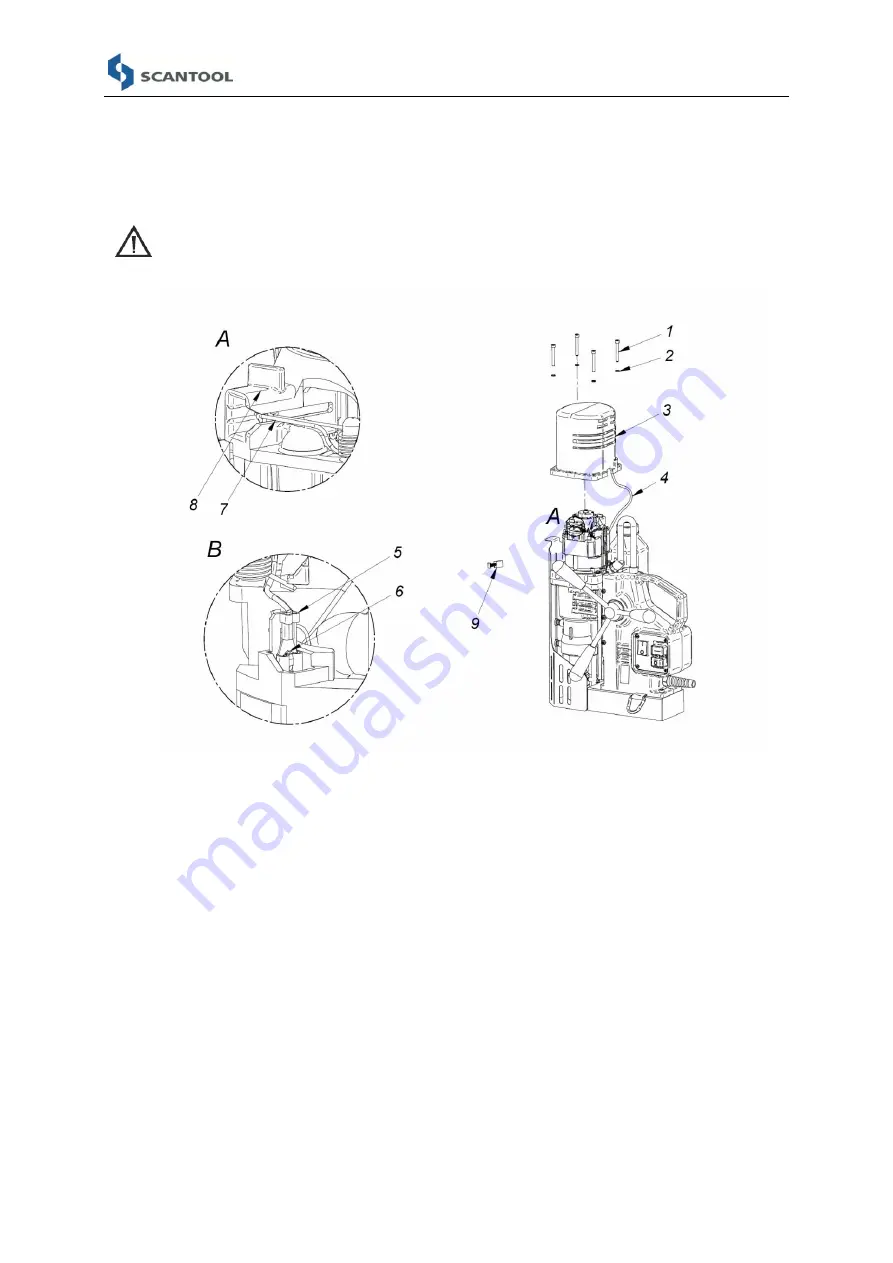
MODEL MB-45
MODEL MB-45
Operator’s manual for Drilling Machine
- 20 -
Replacement of motor brushes:
For the MODEL MB-45 drill, the state of the carbon brushes should be monitored every
100 working hours.
Replacement of motor brushes should take place when the machine is turned off and
the power cable is disconnected from the power grid!
1. Unscrew 4 M5x40 engine cover screws (1), using a 6-kt s=4 wrench.
2. Carefully take off the engine cover (3). Remember that it is connected with the motor by a
grounding lead (4).
3. Take off the motor brushes from the connector (6) using the flat ending (5) of the lead.
The ending has a safeguard against its sliding down
– first, press the protruding element
at the middle of the ending, then carefully slide off the ending from the connector.
4. Push aside the spring arm (7) pressing down the brush and rest it on the surface of the
brush holder (8) and remove the brush (9).
5. Inspect brush length - if the length is less than 5mm, the brush should be replaced with
an original brush.
6. Carry out all actions in reverse, in order to install the engine.
After replacement, new brushes should be Grinded in for about 20 minutes on idle gear.
Replacement of engine brushes is possible without removing the drive from the drill.