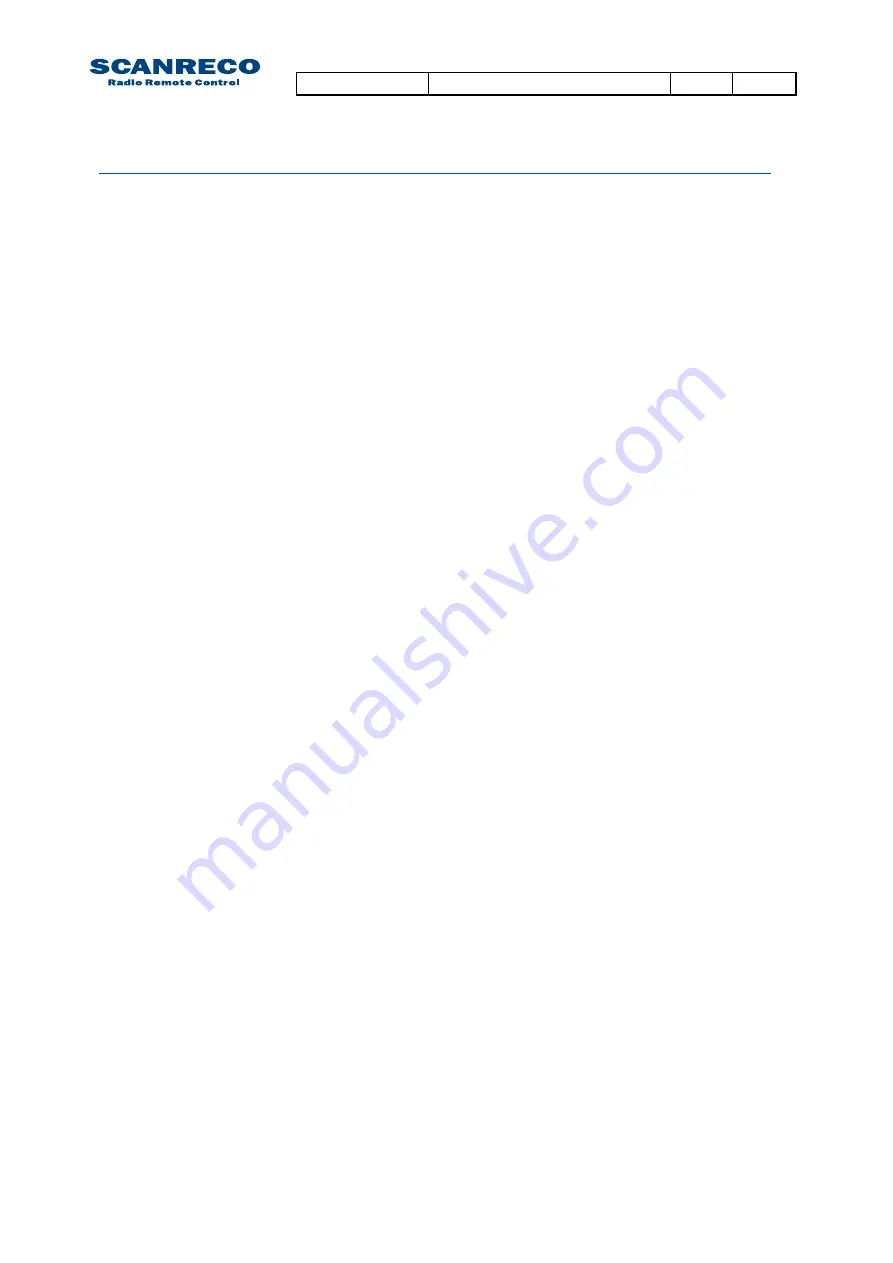
3.1 General description of Scanreco RC-400 G2B/G3B
The Scanreco RC 400 G2B/G3B remote control system has been especially developed for
hydraulically driven mobile cranes and machinery. The system is a digital remote
control system based on an extremely advanced microprocessor technology. Years of
exhaustive and demanding testing have shown that the remote control system can
cope with the roughest of environments.
The system is protected against electromagnetic and radio frequency radiation and
can be installed onto most hydraulic valve types (voltage, current pulse width, or
protocol steered) found on the market.
In its basic form the remote control system is comprised of a portable control unit
with manoeuvre levers for proportional control and switches for ON/OFF functions, a
central unit with connection cable for driving proportional electro-hydraulic slide
controllers.
Digitally coded control information (lever deflection and switch position) is sent from
the control unit via electric cable or via radio to the central unit. The control unit and
central unit translate the magnitude and direction of the manoeuvre lever deflections
and switch positions to corresponding valve function, speed and direction and thus
crane movement.
3 General system description
Document type
Document number
Page
Rev
Service Manual
S071
C
7 of 46