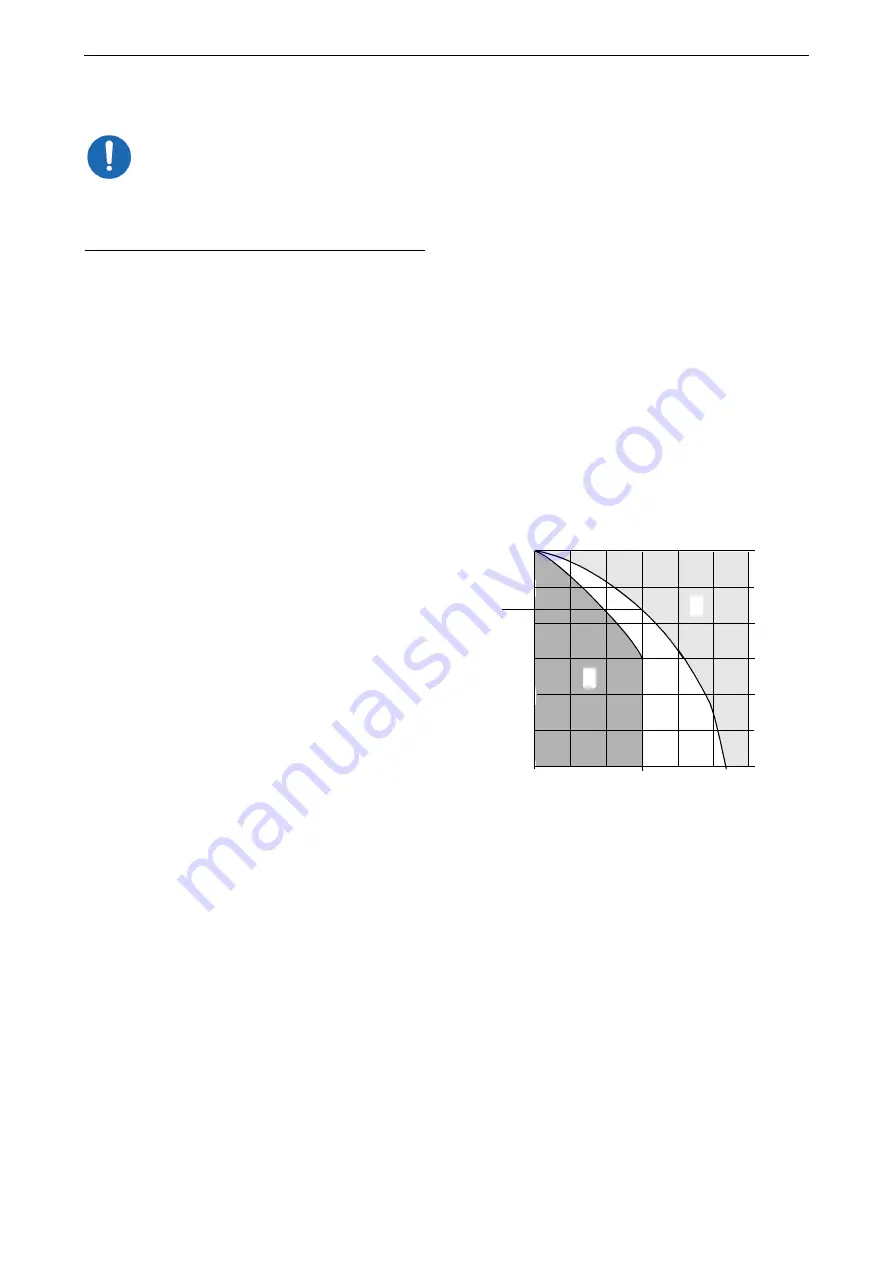
OPM 260 en-GB
41
©
Scania CV AB 2021, Sweden
Cooling system
Risk of freezing
IMPORTANT!
The engine should not be subjected to heavy
loads when ice starts to build up in the cooling
system.
As the coolant starts to freeze, the water in the
coolant starts to crystallise and the percentage of
ethylene glycol in the coolant therefore rises. If
freezing produces a great increase in the amount
of ice, circulation problems could arise. There is
no risk of damage by freezing if the content of
Scania antifreeze and corrosion protection, or an
equivalent mixture of a similar product, is at
least 35% by volume.
Minimal ice formation in the coolant sometimes
causes disruptions without any risk of damage.
For example, the auxiliary heater may not work
for up to one hour after the engine has been start
-
ed.
The chart depicts coolant properties at different
percentages of antifreeze and corrosion protec
-
tion concentration by volume.
The following example shows coolant properties
with 30% by volume of antifreeze and corrosion
protection:
•
Ice slush starts to form at -16°C (3°F).
•
At -30°C (-22°F), there is a risk of disruptions
in the cooling system.
•
There is no risk of damage by freezing with a
minimum antifreeze and corrosion protection
content of 35% by volume.
Example: If the temperature is -16°C (3°F), there
is a risk of damage by freezing if the percentage
of antifreeze and corrosion protection is 20% by
volume. At 30% antifreeze and corrosion protec
-
tion by volume the coolant will not contain any
ice.
Curve A: Ice formation starts (ice slush)
Curve B: Damage by freezing
Zone 1: Safe zone
Zone 2: Disruptions may occur (ice slush)
Zone 3: Risk of damage by freezing
10
20
30
40
50
60%
o
C
o
C
o
C
o
C
o
C
o
C
o
C
-10
-20
-30
-40
-50
-60
-16
3
2
1
A
B
1
2
1
1
3
4