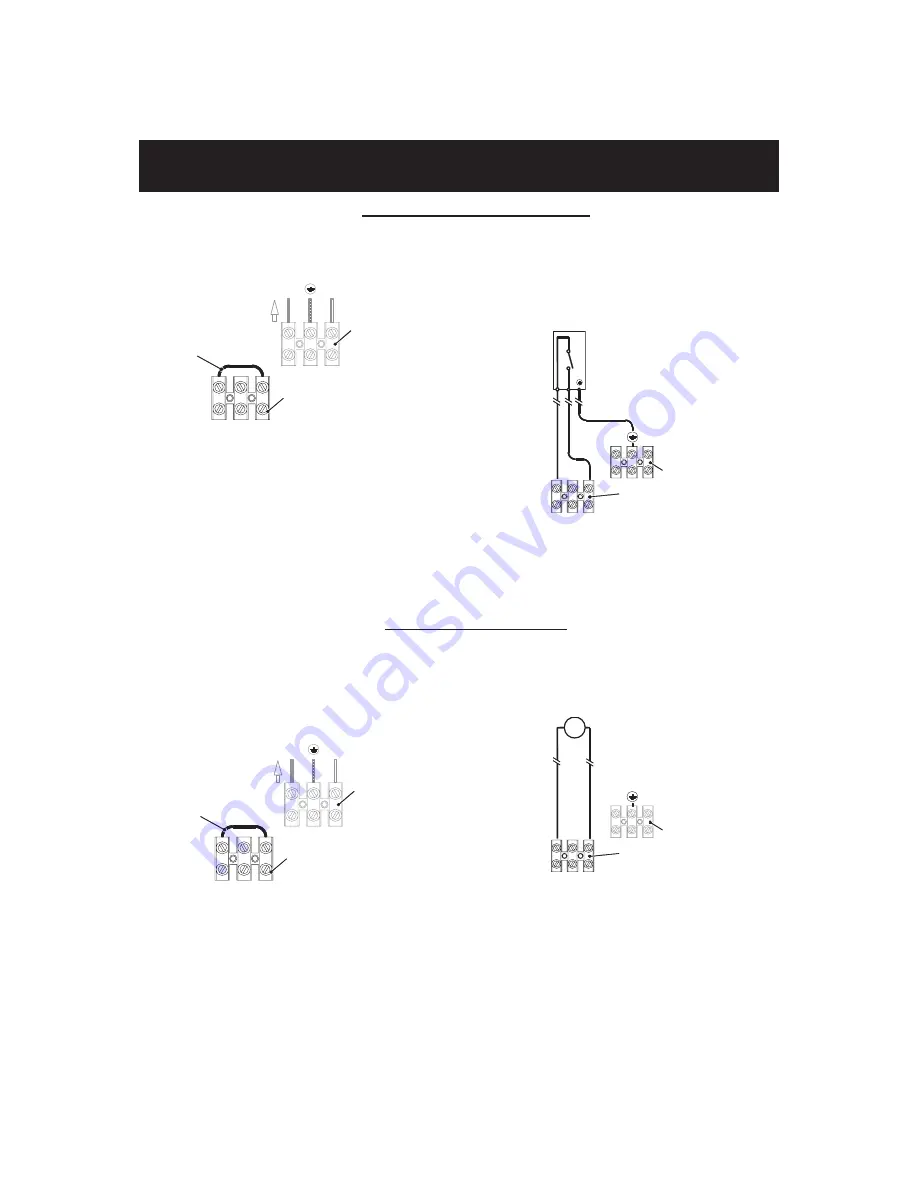
SAVIO HEAT ONLY MANUAL
23
12. Electrical Connections/Wiring Cont.
Room Thermostat Connection:
12.3
The room thermostat must be connected
•
to the terminal block situated next to the
control panel.
Figure 12.6
Any external controls and connection lines
•
must be rated at 120 VAC but under no
circumstances should external live volt-
age be connected to the room thermostat
link on the boiler.
1
2
L
N
3
To fused spur
isolation switch
Power supply
terminal block
External controls
terminal block
J
120 VAC Control
Terminal Block
Relay Panel Connection:
12.4
When connecting any type of external
•
control, the jumper J in Fig. 12.6 must be
removed.
The room thermostat must be connected
•
to the “Control Terminal Block” (Fig 12.7).
Figure 12.7
Connect the room thermostat between
•
terminals 1 and 3 as shown in Fig. 12.7.
Power supply
terminal block
External controls
terminal block
T
Room thermostat
1
2
L
N
3
(120V rating)
The relay control must be connected to
•
the terminal block situated next to the
control panel.
Figure 12.8
When connecting any type of relay con-
•
trol, the jumper J in Fig. 12.8 must be re-
moved.
1
2
L
N
3
To fused spur
isolation switch
Power supply
terminal block
External controls
terminal block
J
Connect the dry contact switch of the re-
•
lay panel to the 120 VAC control terminal
block (Fig 12.9).
Figure 12.9
Connect the dry contact switch to termi-
•
nals 1 and 3 shown in Fig. 12.9.
Power supply
terminal block
External controls
terminal block
Generic Relay Control
1
2
L
N
3
(120V rating)
T
Summary of Contents for Heat Only
Page 39: ...SAVIO HEAT ONLY MANUAL 39 ...
Page 40: ...17962 1507 0 2908 40A4 USA ...