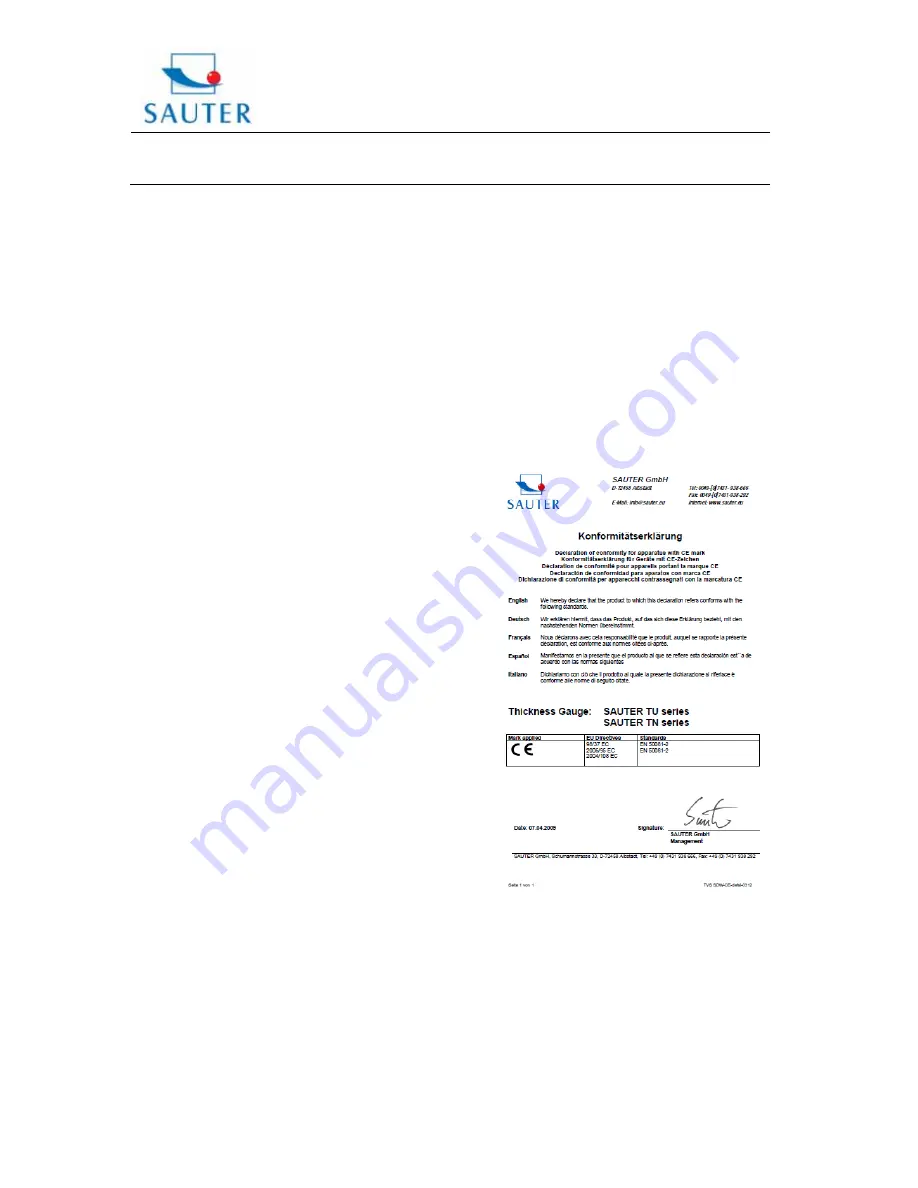
Sauter GmbH
Tieringerstr. 11-15
D-72336 Balingen
E-Mail: [email protected]
Tel: +49-[0]7433- 9976-174
Fax: +49-[0]7433-9976-285
Internet: www. sauter.eu
Instruction Manual
TU_US
TU_US-BA-e-1110
11
will be minimized by calibrating each test piece
individually.
An additional important consideration is , that any included
air gaps or air pockets will cause an early reflection of the
ultrasound beam. This will be noticed as a sudden
decrease in thickness in an otherwise regular surface.
While this may impede accurate measurement of the total
material thickness, it does positively indicate any air gaps
in the laminate.
Suitability of materials
Ultrasonic thickness measurement relies on passing a
sound wave through the material being measured. Not all
materials are suited to transmitting sound. Ultrasonic
thickness measurement is practically found in a wide
variety of materials including metals, plastic and glass.
7. Declaration of conformity
Materials which are difficult include some cast materials,
concrete, wood , fibreglass and some rubber.
Coupling medium
Every ultrasonic application requires some medium to
couple the sound from the transducer to the tested
material. Typically, a high viscosity liquid is used as the
medium. The sound used in ultrasonic thickness
measurement doesn’t travel through air efficiently.
A wide variety of coupling mediums may be used.
Propylene glycol is suitable for mostly all applications. In
difficult applications, where a maximum transfer of sound
energy is required, glycerine is recommended. However,
on some metals glycerine may promote corrosion by
means of water absorption, which is undesirable.
Other suitable coupling medium for measurements at
normal temperatures may include water, various oils and
greases, gels and silicone fluids. Measurements at
elevated temperatures will require specially formulated
high temperature coupling medium.
Inherent in ultrasonic thickness measurement is the
possibility that the instrument will use the second rather
than the first echo from the back surface of the material
being measured while being in standard pulse-echo mode.
This may result in a thickness reading that is TWICE what
it should be.
The responsibility of a proper use of the instrument and the
recognition of these types of phenomenon solely rest with
the user of the instrument.