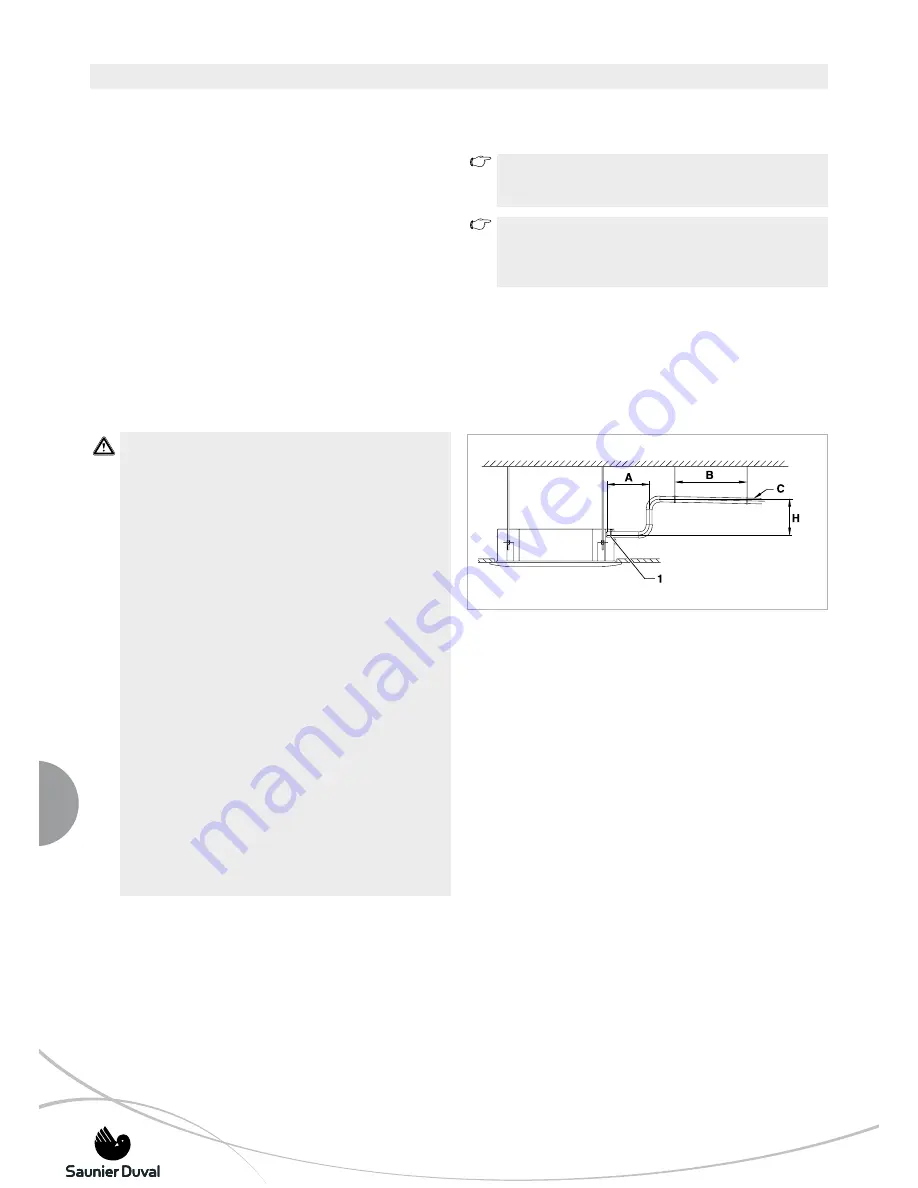
16
EN
CASSETTE - FLOOR-CEILING - DUCTED UNITS
/ Installation Manual
17
9.3 RECOMMENDED INSTALLATION PROCESS
It is recommended carrying out the installation in the follo-
wing order:
• Installation of the condensed water pipe.
• Installation of the refrigerant pipes.
• Installation of the fresh air and bypass lines.
• Electrical installation.
• Indoor unit assembly in the ceiling.
• Connections.
• Checking for leaks and starting the unit.
• Assembly of the decorative panel.
9.4 INSTALLATION OF THE CONDENSED WATER PIPE
9.4.1 HANDLING THE CONDENSED WATER PIPE
WARNING!
Danger of breakdowns or malfunction. Danger of
incorrect drainage of the condensed water and wear of
materials due to dripping water.
Take the following points into consideration:
- Ensure that air circulates through the condensed
water pipe in order to guarantee that the water can
be freely released. Otherwise, the condensed water
could leak through the indoor unit body.
- Mount the pipe without bending it in order to avoid
blockage.
- If the water pipe is channelled outdoors, ensure that
it is insulated against freezing.
- If the condensed water pipe is installed in a room, fit
thermal insulation.
- Avoid installing the condensed water pipe with an
ascending bend.
- Avoid installing the condensed water pipe with it
free end submerged in water.
- Avoid installing the condensed water pipe with
crimping.
- Install the condensed water pipe in such a way that
the distance of its free end from the floor is at least
5 cm.
- Install the condensed water pipe in such a way that
its free end is kept away from unpleasant odours to
ensure that they do not penetrate the room.
9.4.2 LAyING OF THE CONDENSED WATER PIPE
NOTE!
The indoor unit is fitted with a condensed water removal
pump.
NOTE!
Use a pipe whose diameter is at least the same as the
diameter of the indoor unit connection (polyethylene
pipe: inner diameter 25 mm, outer diameter 32 mm).
• Plan the layout of the condensed water pipe taking into
account the indications in section 9.4.1.
- Ensure that the pipe is as short as possible.
- Ensure that the minimum inclination from the indoor unit
is at least 1%.
• Mount the pipe supports taking into account the distances
and inclinations indicated in figure 9.1.
Fig. 9.1
Installation diagram of the Pipe for the Drainage of the
Condensed Water.
Legend
1 Pump flange (jacketing)
A Distance with regard to the indoor unit
(maximum 00 mm)
B Distance between supports (maximum 1 - 1.50 m)
C Pipe inclination (minimum 1%)
H Maximum height of the pipe with regard to the pump
(maximum 500 mm)
• Mount the condensed water pipe in its supports.
- Prevent the pipe from bulging to guarantee the correct
removal of the water.
• Insulate the pipe with thermal insulation.
9 INSTALLATION OF THE CASSETTE INDOOR UNIT