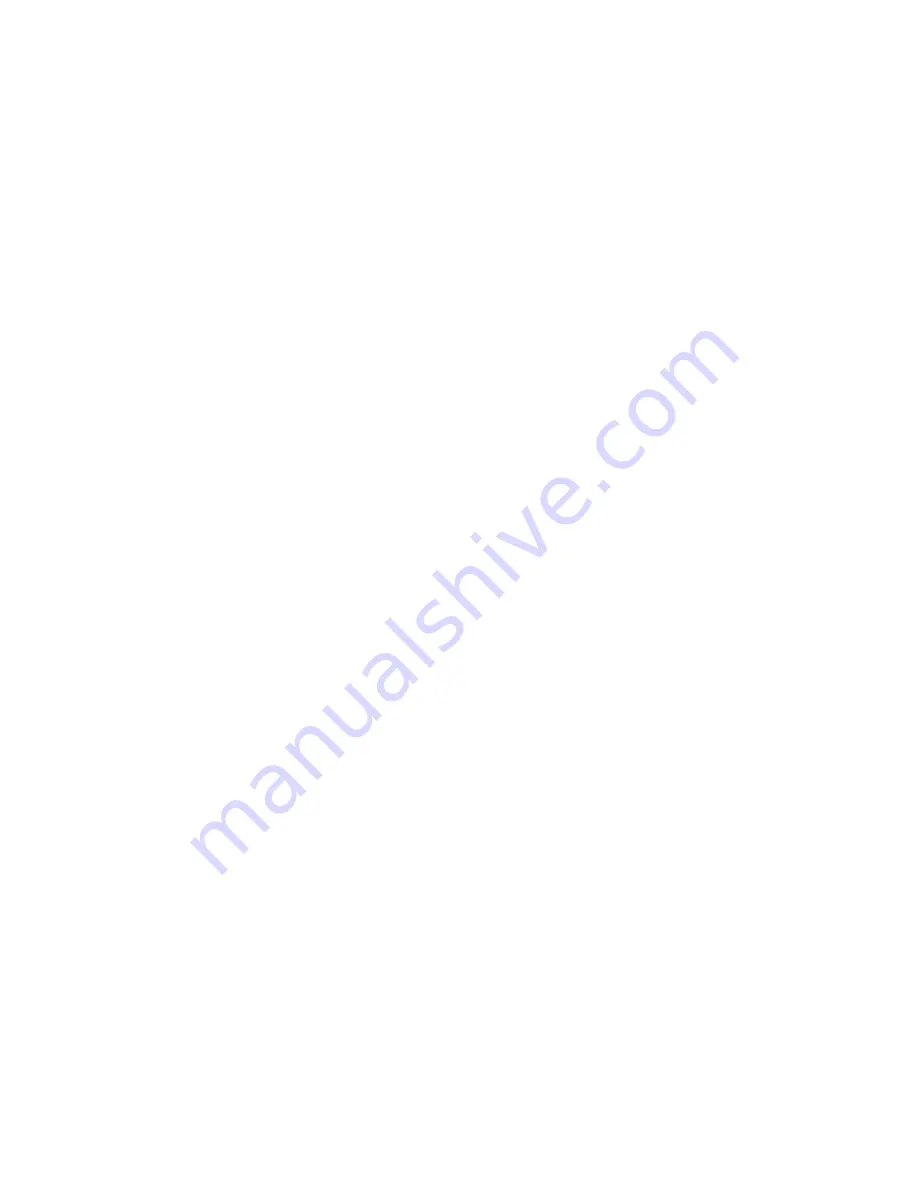
4
Introduction
-
16 programmable data logging partitions, each for recording from 1 to
16 user programmable parameters per record, providing total storage
for up to 114,688 parameters with a 512K memory module (assuming
the entire memory allocated for data logging)
-
one partition for high-speed waveform recording (32 samples x 16
cycles x 6 inputs per record) for disturbance analysis, and one partition
for high-resolution waveform recording (128 samples x 4 cycles x 6
inputs per record) for harmonic analysis, each providing storage for up
to 19, 40, or 82 records with a 512K memory module (assuming the
entire memory allocated for the partition)
•
each memory partition can be sized to store desired number of records, from
1 record and up to the entire memory size, using an arbitrary combination of
partitions
•
each memory partition can be programmed to store the oldest records without
overwriting previously recorded data when a partition is filled up, or to wrap
around by writing new records over the oldest records so that stored records
will always contain the most recent data
Time-of-Use System
•
8 programmable accumulating energy registers for 16 tariffs, each
configurable for counting kWh/kvarh/kVAh or pulses from up to 8 external
energy-counting meters
•
3 programmable demand registers for 16 tariffs, configurable for recording
extreme (minimum and maximum) demands using varying calculation
techniques: block interval/sliding window/thermal demand
•
16 daily profiles (types of days) with up to 8 tariff changes per day
•
2-year calendar
Communications
•
one programmable optically isolated serial port - RS-232/RS-422/RS-485
embedded options with a user-selectable baud rate of 110 to 38400 BPS
Display
•
multi-page display composed of 11 windows with high-brightness seven-
segment digital LEDs. A total of 55 display pages are available
Keypad
•
four membrane long-life push-buttons for page scrolling and programming
Power Supply
•
90-264 V AC, 10-290 V DC options