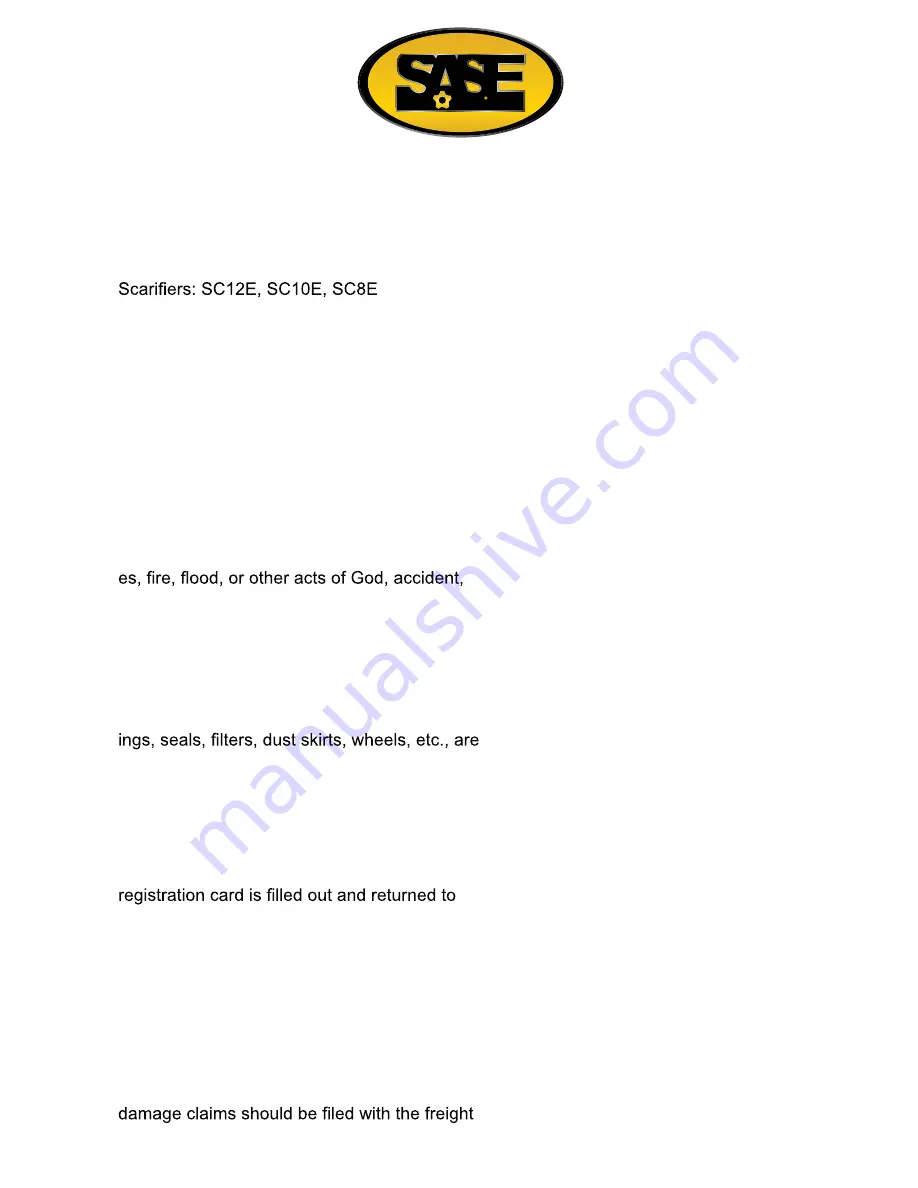
MANUFACTURER’S WARRANTY POLICY
Included in this warranty are the following pieces of equipment:
Planetary Diamond Grinders: PDG 8000, PDG 6000, PDG 5000, Edge Pro 180
Dust Extractors: Bull 1250, Bull 300, Bull 45
Our Commitment to our customer:
SASE Company (“SASE”) equipment is warranted to be free of defects in workmanship and
materials for a period of one (1) year from original date of purchase. In the event that you
should have a claim SASE shall repair, replace or remedy the defective parts resulting from
the faulty design, materials or workmanship. Note: This warranty is only valid for equipment
either sold by SASE or by an authorized wholesaler or distributor.
Limitations:
Warranty does not apply to cosmetic dam-
age, damage due to lightning, electrical surg-
misuse, abuse, repair or alteration by other
than factory service (unless service center was
approved in writing by SASE), negligence, or
improper or neglected maintenance as recom-
mended by SASE.
&RPPRQZDUHSDUWVVXFKDVEHOWVEHDU
-
exempt from warranty.
6$6(LVQRWUHVSRQVLEOHIRUORVVRILQFRPH
or down time as a result faulty design, materi-
als or workmanship.
Warranty coverage is valid once a warranty
SASE.
A $100 labor charge may be assessed on
the items returned for warranty repair in which
no fault is found. Freight charges and associ-
ated fees will then become the responsibility of
the customer in such an instance.
'DPDJHVZKLFKDUHFDXVHGGXULQJWUDQVSRU
-
tation are not covered under warranty. Such
carrier.
Claims:
In the unlikely event that you should experi-
ence a defect please contact your SASE
representative or a SASE service technician
by calling 1.800.522.2606. Please have all
pertinent information readily available such
as, invoice with date of purchase, model and
serial number, and an explanation of the is-
sue. SASE will respond immediately with a
corrective action.
Freight responsibility for approved warranty
claims:
If the piece of equipment was purchased
within 90 days of warranty claim, SASE will
arrange for ground freight and will assume all
ground freight charges to send the customer
the parts required or to send the equipment
to an authorized SASE repair center. This in-
cludes inbound and outbound ground freight
and all fees (duties, fuel surcharges) associ-
ated with the shipment.
If the piece of equipment was purchased
beyond 90 days and prior to one (1) year of
warranty claim, SASE will cover 50% of all
ground freight charges, including inbound
and outbound freight and all fees (duties, fuel
surcharges) associated with the shipment.
SASE
Summary of Contents for PDG 5000
Page 1: ...Version 7 3 Ser 2000 to 3000 Date 01 01 2018 ...
Page 2: ...2 ...
Page 4: ...Rev 7 4 ...
Page 13: ......
Page 16: ...1 2 3 3 SHEET 1 OF 1 SCALE 1 20 WEIGHT 5 4 3 2 1 3 9DFXXP RVH ...
Page 26: ...6 3 13 9 1 2 4 5 7 8 10 11 12 12 Top Drum SHEET 1 OF 1 SCALE 1 10 WEIGHT 17 3kg 5 4 3 2 1 3 5 ...
Page 28: ...3 4 8 5 1 6 6 2 6 6 6 3 7 SHEET 1 OF 3 SCALE 1 3 WEIGHT 22 Kg 5 4 3 2 1 3 RWWRP UXP Rev 7 ...
Page 30: ...8 7 9 5 6 4 1 3 10 2 SHEET 1 OF 1 SCALE 1 10 WEIGHT 26 Kg 5 4 3 2 1 3 RWWRP UXP ...
Page 32: ...1 1 1 2 2 2 SHEET 3 OF 3 SCALE 1 3 WEIGHT 36 Kg 5 4 3 2 1 3 RWWRP UXP Rev 7 ...
Page 34: ...2 5 4 3 5 1 6 SHEET 1 OF 1 SCALE 1 4 WEIGHT 9 5kg 5 4 3 2 1 3 UXP 6KHDYH VVHPEO Rev 7 ...
Page 36: ...3 2 4 1 6 7 5 SHEET 1 OF 1 SCALE 2 3 WEIGHT 212kg 5 4 3 2 1 3 7RS GOHU Rev 6 Rev 7 34 ...
Page 40: ...6 1 2 3 5 4 7 SHEET 1 OF 1 SCALE 1 5 WEIGHT 4 0kg 5 4 3 2 1 3 372 VVHPEO ...
Page 42: ...11 6 1 2 3 3 4 5 6 7 9 10 11 8 SHEET 2 OF 2 SCALE 1 4 WEIGHT 5 4 3 2 1 3 0DLQ 7LJKWHQHU ...
Page 44: ...7 6 5 1 3 3 4 2 SHEET 2 OF 2 SCALE 1 4 WEIGHT 1 59kg 5 4 3 2 1 3 0DLQ HOW ULYH ...
Page 46: ...1 2 3 4 4 SHEET 1 OF 1 SCALE 1 2 WEIGHT 1 25kg 5 4 3 2 1 3 0DLQ GOHU Rev 7 ...
Page 48: ...10 9 8 7 6 5 4 3 2 1 11 SHEET 1 OF 1 SCALE 1 8 WEIGHT 5 4 3 2 1 3 3ODQHWDU ...
Page 50: ...8 7 8 5 11 2 1 3 6 9 10 4 6 SHEET 1 OF 1 SCALE 1 10 WEIGHT 3 81 5 4 3 2 1 3 OH HDG ...
Page 52: ...2 3 1 4 5 SHEET 1 OF 1 SCALE 1 5 WEIGHT 5 4 3 2 1 3 7RROLQJ 3ODWH ...
Page 55: ...Rev 7 ...