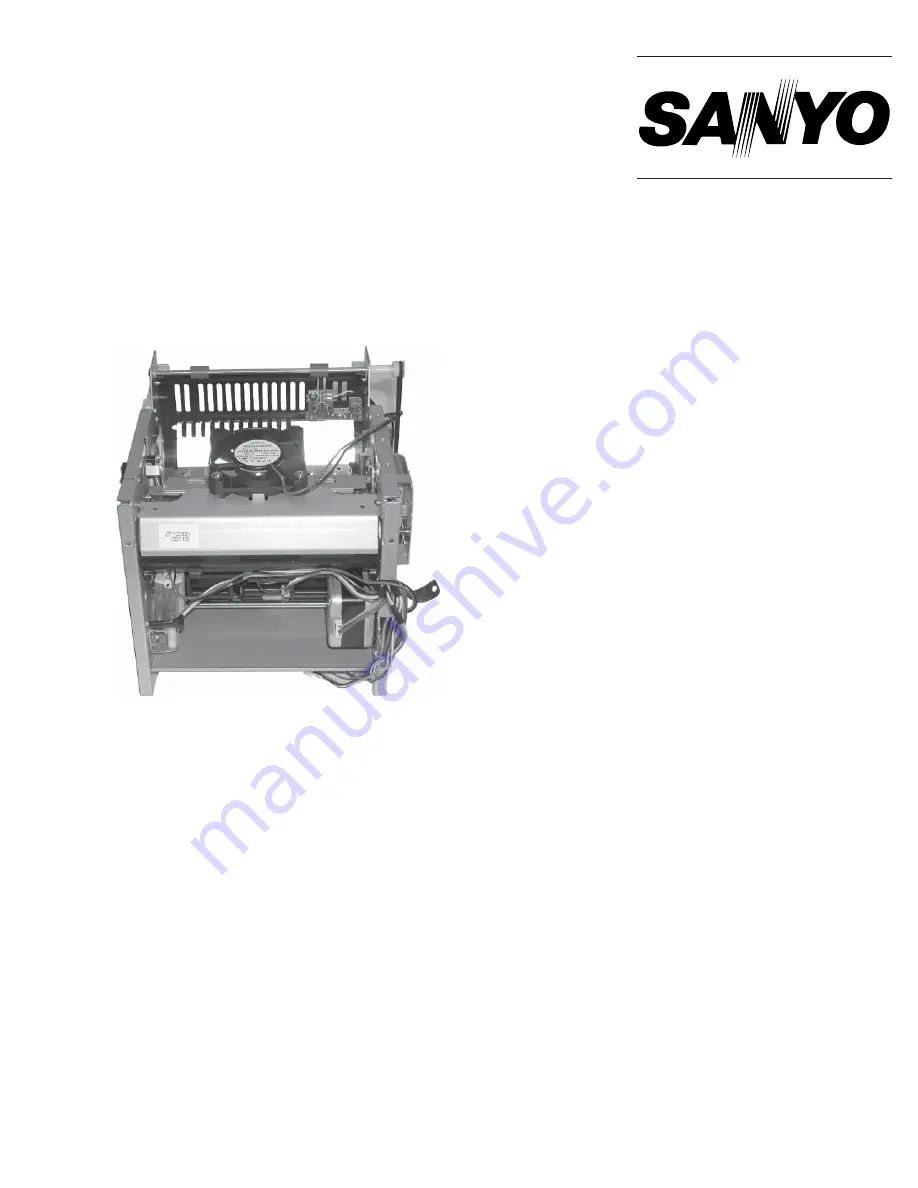
1. SERVICE TOOLS ........................... 2
MECHANISM .................................. 3
2-1. Exploded view of the Unit .................. 3
2-2. Overview ............................................ 5
2-3. Cam Drive .......................................... 5
2-4. Paper Advance Drive ......................... 6
2-5. Ink Ribbon Drive ................................ 7
2-6. Mechanism Mode Verification
Method ............................................... 7
PARTS OF THE MECHANISM ....... 8
3-1. “MOTOR,FAN DC 1.8W”, “GUIDE,
INK-SVF01/EX”, and “LEVER,
CASSETTE STOPPER” .................... 8
3-2. S REEL ASSEMBLY .......................... 9
3-3. HEAD ............................................... 10
3-4. PAPER EXIT ROLLER .................... 12
3-5. SUPPLY PAPER ROLLER .............. 12
3-6. “ASSY, MOTOR STEPPING” ........... 14
Contents
3-7. RELAY PULLEY .............................. 14
3-8. “PULLEY,DRUM” ............................. 16
3-9. CAM MOTOR .................................. 16
3-10. “CHASSIS,SUB LOWER” ................ 18
3-11. “COMPL,HOLDER,PINCH SIDE”,
3-12. “SLIDE,LEVER TPH” ....................... 20
“COMPL PWB,MC-6” ....................... 20
3-14. “ASSY,CHASSIS R”, “COMPL, PIPE
DRUM RUBBER”, “COMPL,GUIDE,
PAPER”, “CAM,MECHANISM R”,
and “CAM,MECHANISM L” ............. 22
“COMPL PWB,MC-3” ....................... 24
3-16. “GUIDE,PAPER EXIT”, “COMPL
PWB,MC-4”, and “COMPL PWB,
MC-5” ............................................... 24
3-17. “LEVER,TPH ADJUST”, “BEARING,
DRUM”, and “BEARING,DRUM” ..... 25
4. TROUBLESHOOTING .................. 26
4-1. The mechanism malfunctions when
the power is turned on. .................... 26
4-2. Poor printing quality ......................... 26
4-3. Not printing ...................................... 27
4-4. Paper stopping ................................ 28
MECHANISM SERVICE
TECHNICAL INFORMATION
Digital Photo Printer
FILE NO.
REFERENCE No.MM5310544
SVF01/EX, U, C
DVP-P1EX
(Product code: 126 306 02)
DVP-P1
(Product code: 126 306 01)
DVP-P1C
(Product code: 126 306 03)