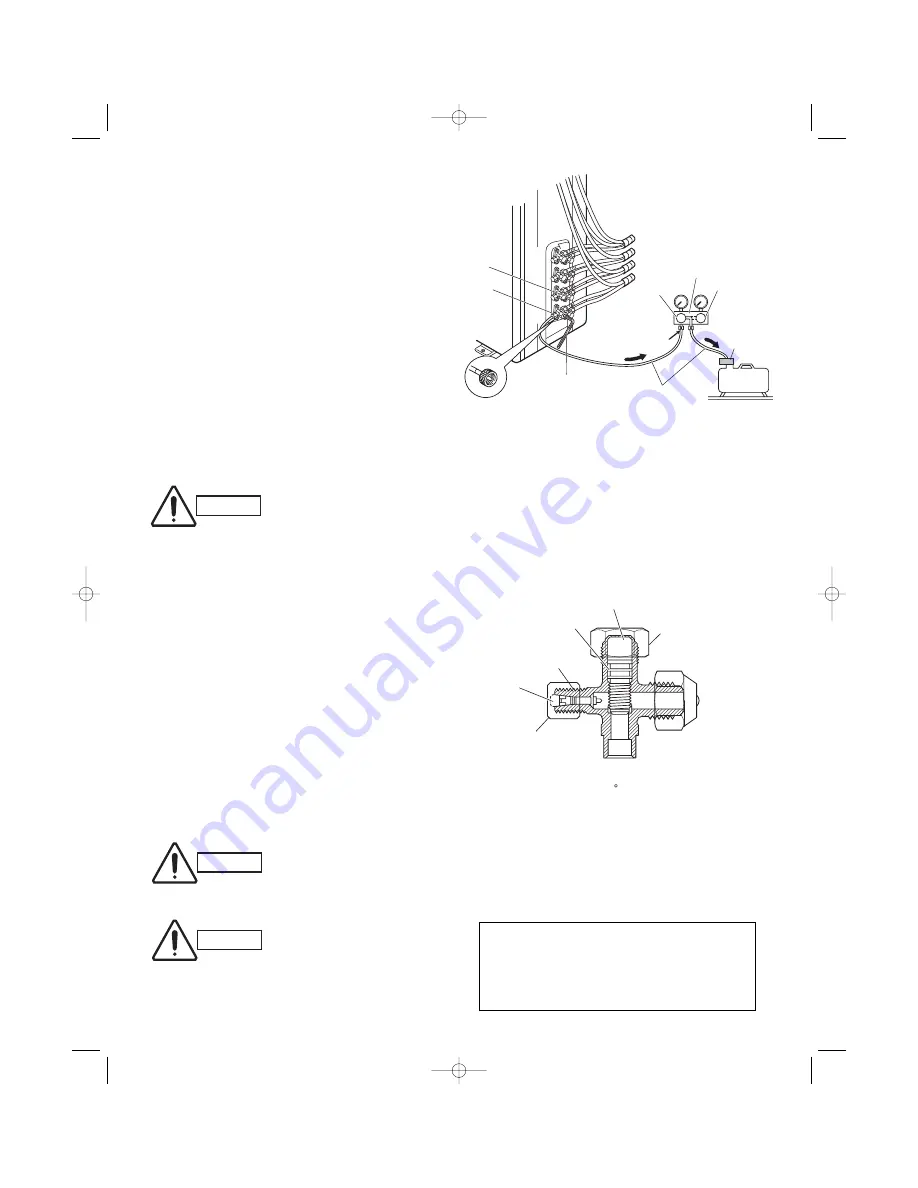
16
4. Air Purging
Air and moisture remaining in the refrigerant system have
undesirable effects as indicated below. Therefore, they
must be purged completely.
G
pressure in the system rises
G
operating current rises
G
cooling efficiency drops
G
moisture in the air may freeze and block capillary tubing
G
water may lead to corrosion of parts in the refrigerant
system
I
Air Purging with a Vacuum Pump
(for Test Run)
G
In order to protect the earth’s environment, be sure to use
a vacuum pump to perform the air purge.
(Never perform an air purge by using the refrigerant gas
cylinder or other external gas, or by using the gas inside
the outdoor unit.)
Perform the air purge for tubes A, B, C, and D. Use the
same procedures for all tubes.
(1) Check that each tube (both narrow and wide tubes)
between the indoor and outdoor units have been
properly connected and all wiring for the test run has
been completed. Note that both narrow and wide tube
service valves on the outdoor unit are kept closed at
this stage.
(2) Using an adjustable wrench or box wrench, remove
the valve caps from the service valve on both narrow
and wide tubes.
(3) Connect a vacuum pump and a manifold valve (with
pressure gauges) to the service port on the wide tube
service valve. (Fig. 20).
Fig. 20
Fig. 21
CAUTION
Be sure to use a manifold valve for
air purging. If it is not available,
use a stop valve for this purpose.
The “Hi” knob of the manifold
valve must always be kept closed.
CAUTION
CAUTION
Before using the vacuum pump
adapter, read the vacuum pump
adapter manual, and use the
adapter correctly.
In order to prevent charging errors with
A/C that uses R410A, the screw diameter
at the service valve charging port has
been changed. When recharging or per-
forming other servicing, use the special
charging hose and manifold gauge.
G
When using a hex wrench to open the spindle, an
extremely small amount of refrigerant may leak.
This does not indicate a problem.
G
Use a hex wrench of a type to which force can be
easily applied.
Service
valve on
wide tube
side
Service
valve on
narrow
A
B
C
D
Vacuum
pump
Vacuum pump
adapter
(for preventing
reverse flow)
(special for
R410A)
High-pressure valve
Manifold gauge
(special for R410A)
Low-pressure
valve
Leave the
valve open.
Open
Charging hose
(special for R410A)
Hex wrench
With push-pin
Hi
Lo
Cap tightening torque:
170 – 215 lbs·in
(200 – 250 kgf·cm)
(Tighten by hand, then
use a wrench to turn.)
Stopper
Spindle
Screw diameter: 1/2
UNF 20 threads
Valve core
Cap nut tightening torque:
60 – 95 lbs·in
(70 – 110 kgf·cm)
(Tighten by hand, then use a
wrench to turn approximately 30 .)
<Structure of service valve on wide tube side>
05-352 KMHS0772_outdoor 3/17/06 2:56 PM Page 16