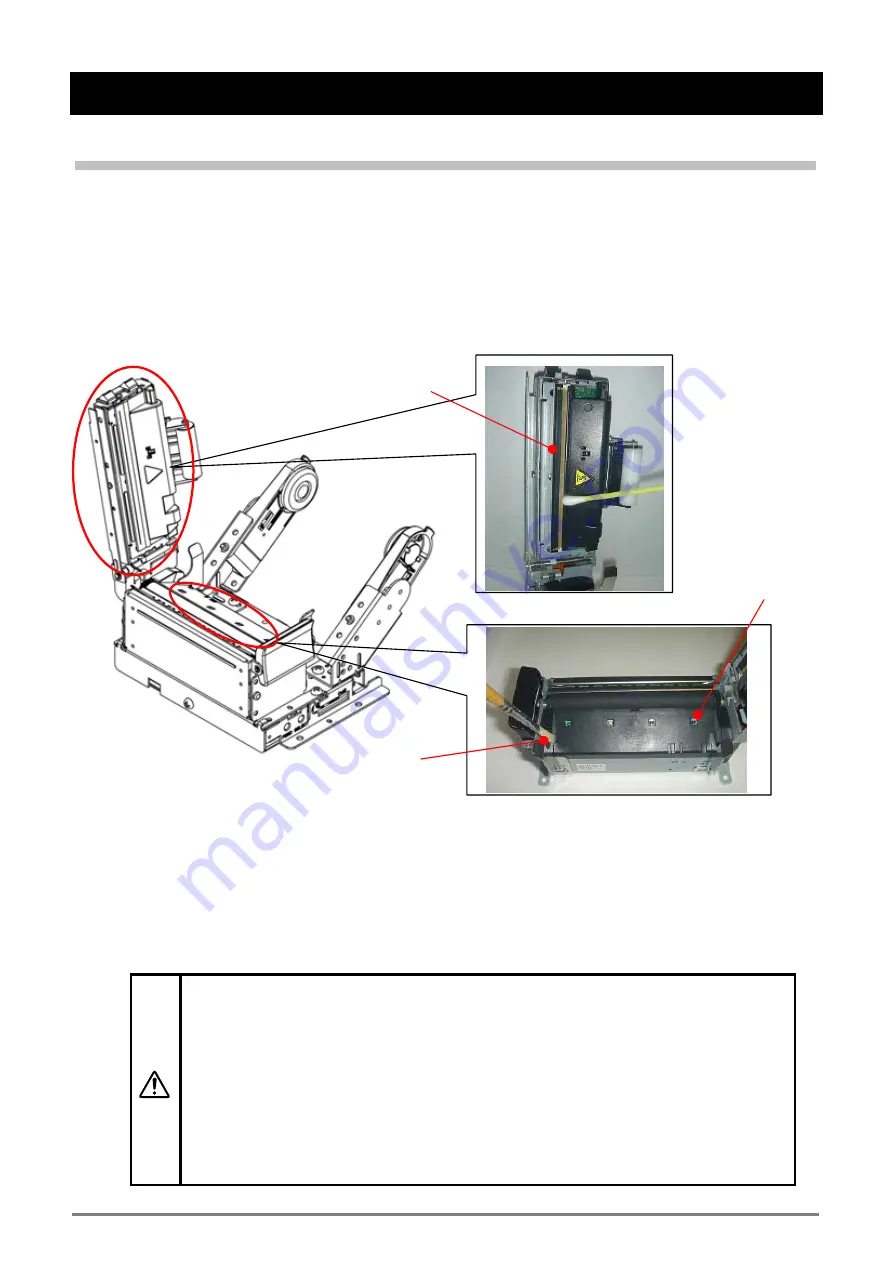
9
.
Maintenance
9- 1
.
Maintenance
Periodically clean the printer to maintain the printing quality and avoid failures. It is recommended
to maintain the printer every 6 months or 1 million lines of printing.
(
1
)
Print head
When cleaning the thermal dot line on the print head, use a cotton swab with alcohol
(ethanol, methanol or Isopropyl alcohol) and wipe off stains and dust.
49
SK1-211/311
Paper cover
sensor
Thermal dot line
Paper empty
sensor
(
2
)
Platen roller
When cleaning the platen roller, use a dry soft cloth and wipe off the stain with rotating
the roller.
(
3
)
Sensor and peripherals
Clean the stain, dust and paper powder on the paper empty sensor and paper cover
sensor.
・
Prior to maintenance work, be sure to turn OFF the printer.
・
Avoid cleaning the print head immediately because the print head is hot.
Start maintenance work after the thermal head becomes cool.
・
Do not touch the print head with fingers directly. It may cause damage by
electrostatic discharge and contamination.
・
Do not touch the thermal head dot line with bare hands or metal objects.
・
Do not use volatile chemical agents, such as thinner and benzene.
・
Do not get moisture or spill liquids inside of the printer.
・
Turn ON the printer only after alcohol is completely dried.
Summary of Contents for SK1-211
Page 1: ...Technical Guide KIOSK PRINTER SK1 211 SK1 311 Rev1 1E SK1 211 311...
Page 25: ...3 7 Dimensions External dimensions Unit mm SK1 311 model SK1 211 311...
Page 26: ...SK1 211 311...
Page 27: ...SK1 211 model SK1 211 311...
Page 28: ...SK1 311 with paper 83mm 120mm SK1 211 311...
Page 54: ...10 2 Data code table PC437 SK1 211 311...
Page 55: ...KATAKANA SK1 211 311...
Page 56: ...PC850 SK1 211 311...