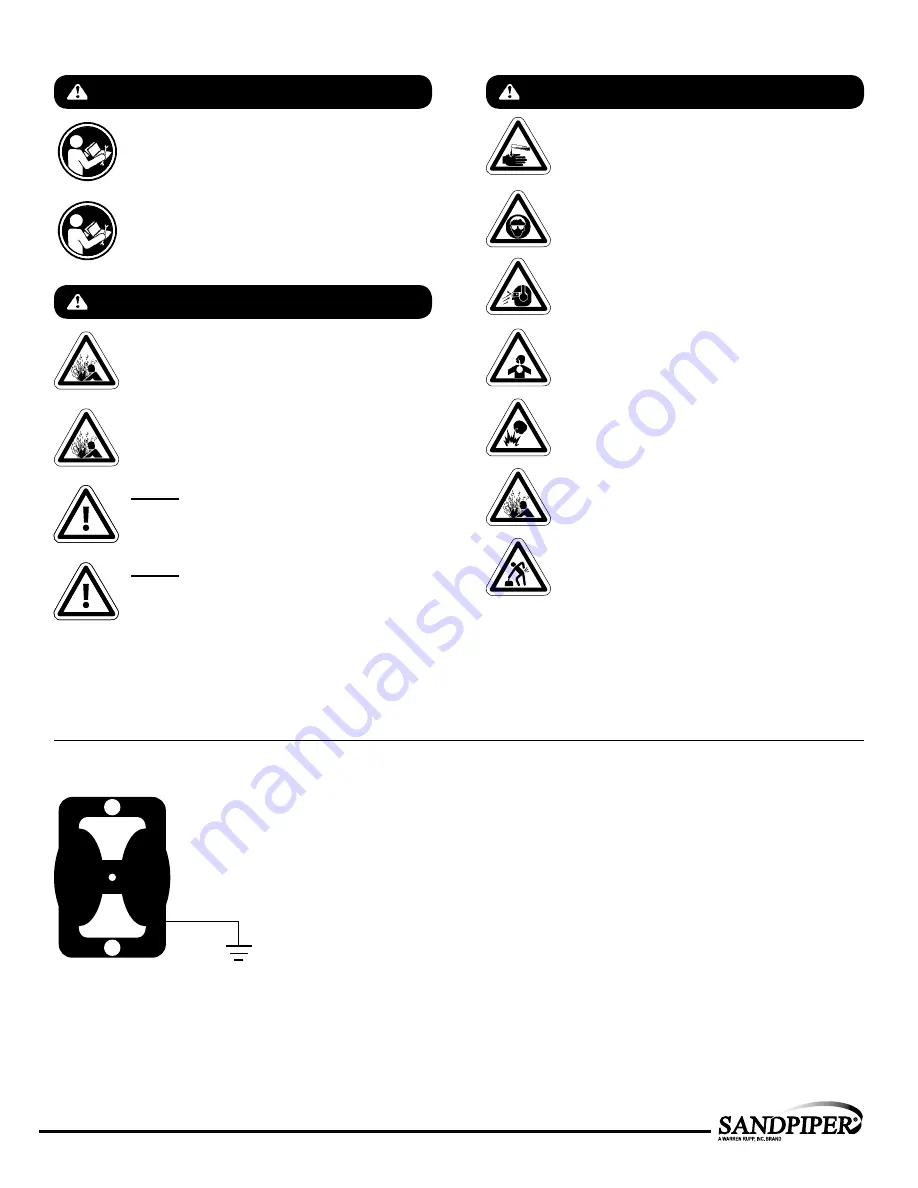
hdf2dl6sm-rev0817
sandpiperpump
.
com
Model HDF2/HDF50
IMPORTANT
Read the safety warnings and instructions in this manual
before pump installation and start-up. Failure to comply with
the recommendations stated in this manual could damage the
pump and void factory warranty.
When used for toxic or aggressive fluids, the pump should
always be flushed clean prior to disassembly.
Airborne particles and loud noise hazards. Wear eye and ear
protection.
Before maintenance or repair, shut off the compressed air line,
bleed the pressure, and disconnect the air line from the pump.
Be certain that approved eye protection and protective clothing
are worn at all times. Failure to follow these recommendations
may result in serious injury or death.
ATEX compliant pumps are suitable for use in explosive atmospheres when the equipment is properly grounded
in accordance with local electrical codes. Pumps equipped with electrically conductive diaphragms are suitable for
the transfer of conductive or non-conductive fluids of any explosion group. When operating pumps equipped with
non-conductive diaphragms that exceed the maximum permissible projected area, as defined in EN 13463-1: 2009
section 6.7.5 table 9, the following protection methods must be applied:
• Equipment is always used to transfer electrically conductive fluids or
• Explosive environment is prevented from entering the internal portions of the pump, i.e. dry running
For further guidance on ATEX applications, please consult the factory.
When the pump is used for materials that tend to settle out
or solidify, the pump should be flushed after each use to
prevent damage. In freezing temperatures the pump should be
completely drained between uses.
Before pump operation, inspect all fasteners for loosening
caused by gasket creep. Retighten loose fasteners to prevent
leakage. Follow recommended torques stated in this manual.
CAUTION
WARNING
Nonmetallic pumps and plastic components are not UV
stabilized. Ultraviolet radiation can damage these parts and
negatively affect material properties. Do not expose to UV light
for extended periods of time.
In the event of diaphragm rupture, pumped material may enter
the air end of the pump, and be discharged into the atmosphere.
If pumping a product that is hazardous or toxic, the air exhaust
must be piped to an appropriate area for safe containment.
This pump is pressurized internally with air pressure during
operation. Make certain that all fasteners are in good condition
and are reinstalled properly during reassembly.
Take action to prevent static sparking. Fire or explosion can
result, especially when handling flammable liquids. The pump,
piping, valves, containers and other miscellaneous equipment
must be properly grounded.
Safety Information
Grounding ATEX Pumps
WARNING
Pump not designed, tested or certified to be powered by
compressed natural gas. Powering the pump with natural
gas will void the warranty.
Use safe practices when lifting
kg
WARNING
The use of non-OEM replacement parts will void (or negate)
agency certifications, including CE, ATEX, CSA, 3A and EC1935
compliance (Food Contact Materials). Warren Rupp, Inc. cannot
ensure nor warrant non-OEM parts to meet the stringent
requirements of the certifying agencies.
UNIVERSAL ALL AODD