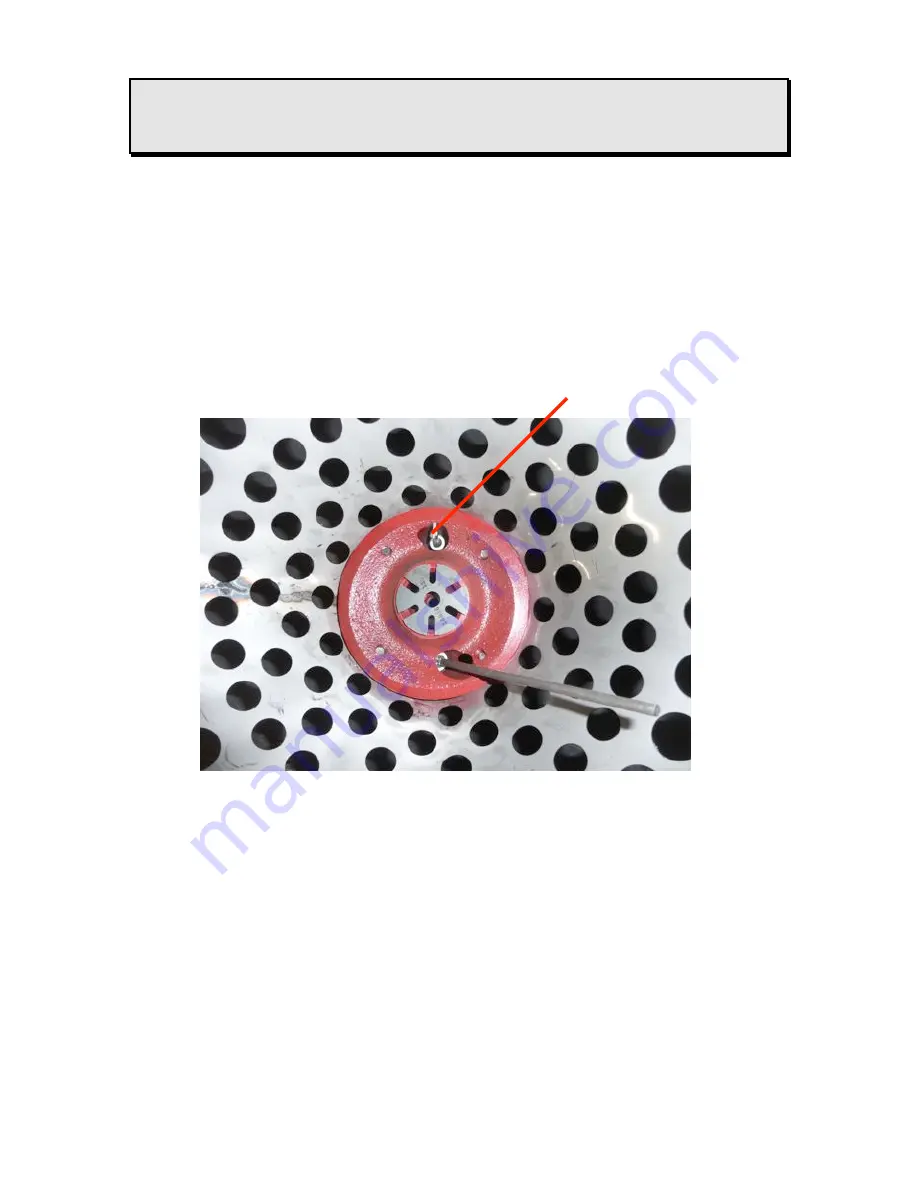
PAGE 29 of 46 HG-1-1501 GAS-FIRED HEATER
© SAMUEL JACKSON, INCORPORATED 2011 ALL RIGHTS RESERVED
BURNER ORIFICE ALIGNMENT
If you are experiencing excessive flame failures or difficulty establishing flame, check to
make sure the orifice in your burner head is aligned correctly to the flame rod. Proper
orifice alignment will also reduce the formation of soot and carbon on the flame rod
especially when using propane or butane fuels.
The picture below shows the correct alignment of the orifice disk. The contoured
stainless steel disk has been removed for illustration. Note that one of the orifice slots is
pointed directly toward the spark plug.
To adjust the orifice alignment, remove the contoured disk from the burner body by
removing the 3/8 inch stainless steel cap screw. Rotate the orifice disk so that one of the
slots is pointed directly at the spark plug. Insert a small screwdriver through the hole in
the burner shell and into a slot in the orifice. Reinstall the contoured disk while using the
screwdriver to keep the orifice from rotating.
After reinstalling the burner assembly, the flame rod should glow red hot while the flame
is on improving ignition, reducing flame failures and reducing formation of soot and
carbon on the flame rod.
Point one slot directly
to spark plug
Summary of Contents for HG-1-1501
Page 1: ...HG 1 1501 1 Million Btu Hr Gas Fired Heater Service and Operation Guide...
Page 2: ...PAGE 1 of 46 HG 1 1501 GAS FIRED HEATER SAMUEL JACKSON INCORPORATED 2011 ALL RIGHTS RESERVED...
Page 35: ...PAGE 32 of 46 HG 1 1501 GAS FIRED HEATER SAMUEL JACKSON INCORPORATED 2011 ALL RIGHTS RESERVED...
Page 36: ...PAGE 33 of 46 HG 1 1501 GAS FIRED HEATER SAMUEL JACKSON INCORPORATED 2011 ALL RIGHTS RESERVED...
Page 38: ...PAGE 35 of 46 HG 1 1501 GAS FIRED HEATER SAMUEL JACKSON INCORPORATED 2011 ALL RIGHTS RESERVED...
Page 40: ...PAGE 37 of 46 HG 1 1501 GAS FIRED HEATER SAMUEL JACKSON INCORPORATED 2011 ALL RIGHTS RESERVED...
Page 41: ...PAGE 38 of 46 HG 1 1501 GAS FIRED HEATER SAMUEL JACKSON INCORPORATED 2011 ALL RIGHTS RESERVED...
Page 46: ...PAGE 43 of 46 HG 1 1501 GAS FIRED HEATER SAMUEL JACKSON INCORPORATED 2011 ALL RIGHTS RESERVED...
Page 47: ...PAGE 44 of 46 HG 1 1501 GAS FIRED HEATER SAMUEL JACKSON INCORPORATED 2011 ALL RIGHTS RESERVED...
Page 48: ...PAGE 45 of 46 HG 1 1501 GAS FIRED HEATER SAMUEL JACKSON INCORPORATED 2011 ALL RIGHTS RESERVED...