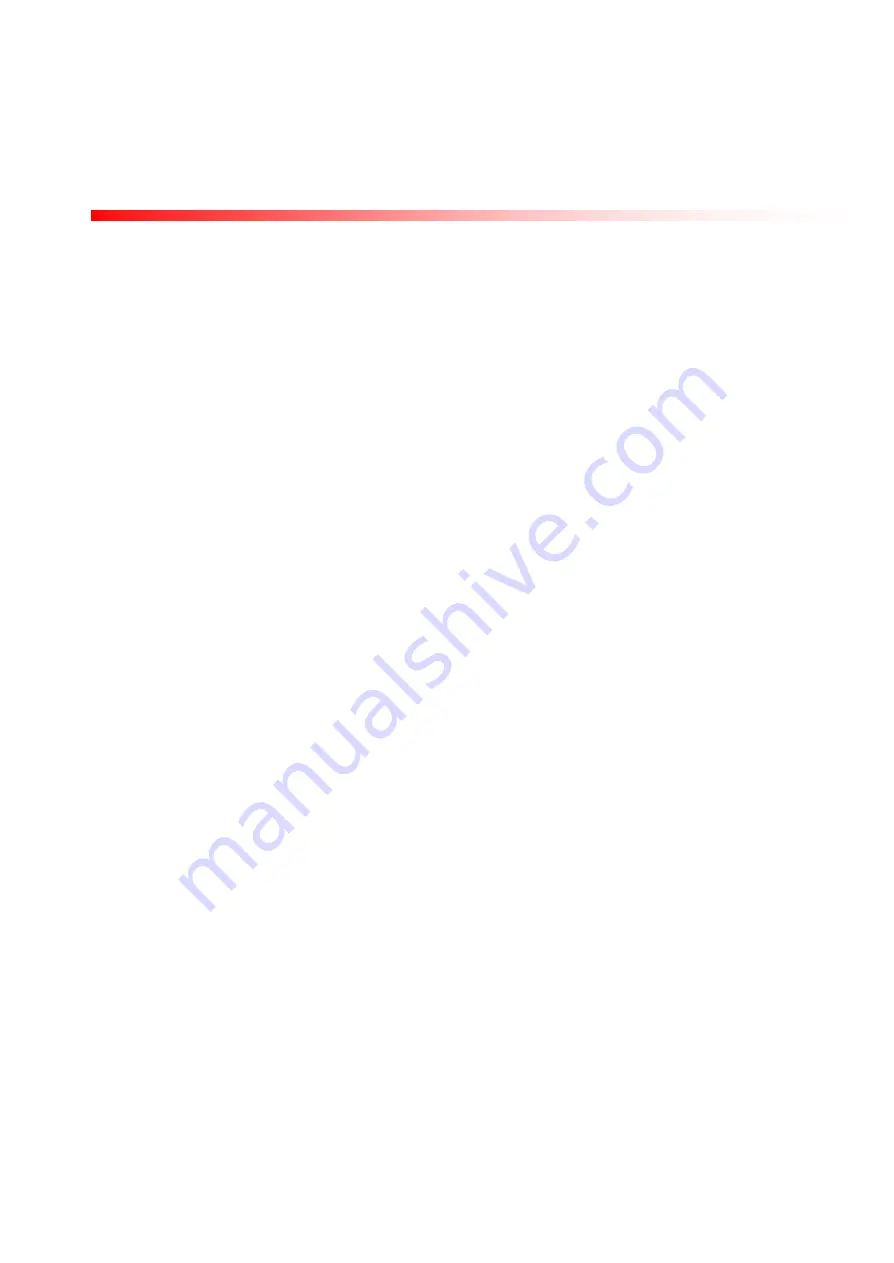
Page 4
SF-330 Series Graphic Print Bar
Service Guide
Samsung Electronics Confidential
Copyright Samsung Electronics Company 2002
SF-330 Series Graphic Print Bar Service Guide
Revision 1.0; 23-Jul-02
1.2 Carriage Movement
The carriage is belt driven, using a 3-to-1 gear set for coupling to the motor. The gear set minimizes side -loading
of the motor, because the belt is not attached directly to the motor. The belt is supported and driven at the left end
by the belt gear, and supported at the right end by the idler pulley. The belt is mounted to a clip that snaps into the
back of the carriage.
The top of the carriage travels across the carriage bar on a flat bearing that maintains the tilt of the carriage. The
bearing provides low overall friction with the steel carriage chassis. A sintered bronze bushing impregnated with
lubricant provides both low friction levels and environmental stability with changes in temperature or humidity.
Interface oil holds the friction level constant. The oil is a synthetic, low vapor -pressure oil that is compatible with
the plastic parts and resistant to evaporation.
The carriage rocks slightly, as a function of clearance between the carriage rod and the bushing on the bottom of
the carriage, as well as the bearing at the top of the carriage. To minimize the impact of carriage rocking, relative
to the encoder system, a mylar encoder strip is positioned closely to the nozzle plate of the print cartridge. The
mylar material is resistant to fingerprints, paper dust, and so forth. It is slightly sensitive to temperature and
humidity, so a flat spring (on the right side of the steel carriage bar) maintains tension on the encoder strip.
The quadrature optical encoder and a decoupling capacitor are soldered onto the flex circuit on the rear side of the
carriage. The flex circuit comes out through the front side of the carriage, where it splits and folds over itself in
order to travel within the compact carriage path.
The flex circuit carries signals for the encoder system, as well as drive voltage for the print cartridge. Signal lines
for the print cartridge terminate at the flex-circuit contacts on the interconnect pad in the front of the carriage.
These contacts interface with contacts on the back of the print cartridge.
1.3 Print Cartridge Maintenance
The top of the carriage contains a spring latch for the print cartridge. The spring latch provides tension for
consistent
snap-in
of the print cartridge. The print cartridge should only be replaced when the carriage is in the
designated service position, which is controlled from the product’s front panel.
When installing a print cartridge, the bottom portion of the print cartridge should be installed into the carriage
assembly as shown in Figure 1-2. Once the bottom is seated in the carriage, push the top portion of the cartridge
toward the carriage until it
snaps
into place beneath the spring latch. Always ensure that the electrical contacts
inside the carriage are clean. Do not handle or touch the contacts because oil from the user’s fingers can corrode
the electrical contacts (see Figure 2-3 in section 2.1.2.1 for carriage and cartridge contact cleaning instructions).
The service station, at the left end of the carriage path, contains two wipers and two nozzle caps to provide
servicing and capping for either a monochrome or a color print cartridge (see Figure 1-3). The caps and wip ers are
mounted on a rotary assembly, which incorporates a micro-switch for accurate positioning.