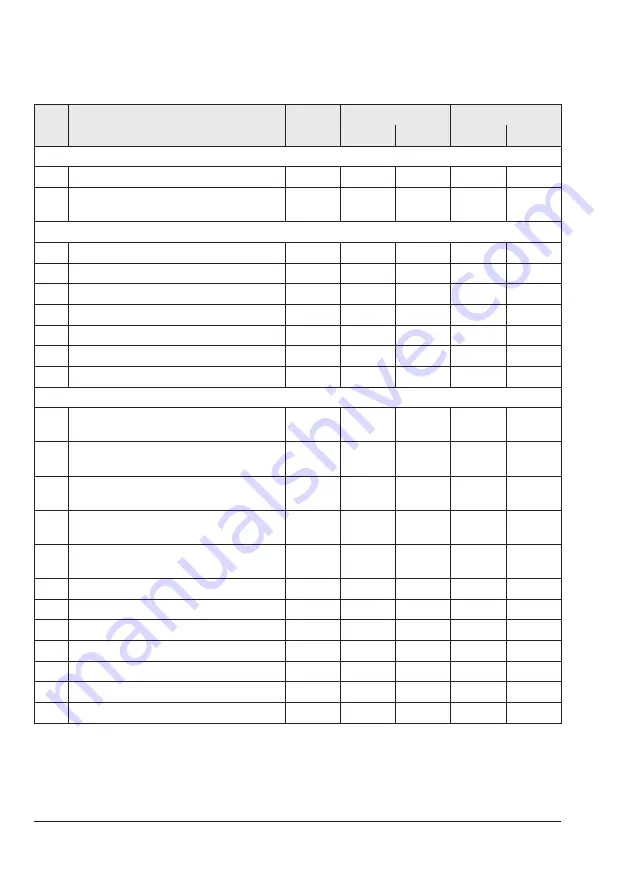
50
EB 5724-8 EN
Annex
HR
Designation
Access
Transmission range
Indicating range
Start
End
Start
End
Manual level
25
Manual positioning value (external)
R/W
0
1000
0.0
100.0
26
Set point deviation of the external manual lev-
el
R
0
1000
0.0
100.0
Operating values (operating function)
27
Operating function status
R
0
11
0
11
28
Operating function cause
R
0
3
0
3
29
Program controller set point
R
–500
1500
–50.0
150.0
30
Program controller time elapsed
R
0
10080
0
10080
31
Reserved (time elapsed for start function)
R
0
65535
0
65535
32
Reserved (time elapsed for end function)
R
0
65535
0
65535
33
Reserved (time elapsed for switching output)
R
0
65535
0
65535
Operating values and settings of controller [1]
34
Actual value before comparator of controller
[1] (PV[1])
R
–500
1500
–50.0
150.0
35
Set point before comparator of controller [1]
(SP[1])
R
–500
1500
–50.0
150.0
36
Set point deviation of controller [1] (SP[1] –
PV[1])
R
–9999
9999
–999.9
999.9
37
Positioning value of controller [1] before char
-
acteristic Y[1]
R
0
1000
0.0
100.0
38
Positioning value of controller [1] after charac
-
teristic YP[1]
R
0
1000
0.0
100.0
39
Set point deviation of controller [1]
R
0
1
0
1
40
Active controller set point [1]
R
0
9
0
9
41
Set point C1.SP
R/W
–500
1500
–50.0
150.0
42
Reserved
R
0
65535
0
65535
43
Reserved
R
0
65535
0
65535
44
Reserved
R
0
65535
0
65535
45
Reserved
R
0
65535
0
65535