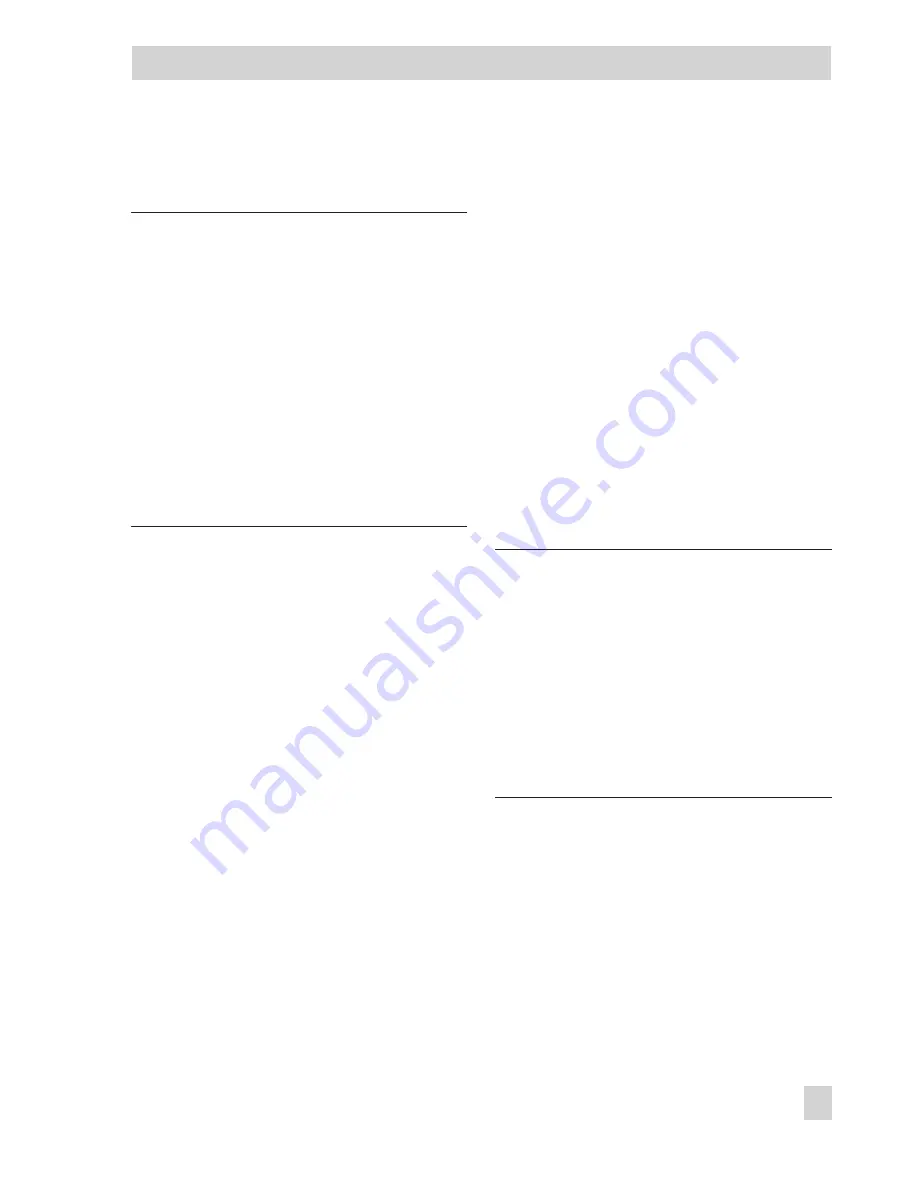
4.3.2 Setting actuator version
“Stem extends”
Note:
To ensure that the total closing force of the
actuator can be effective in the control valve,
the diaphragm chamber must be completely
vented at the lower range value of the refer-
ence variable (operating direction <<) and
at the upper range value (operating direc-
tion <>).
When the operating direction is direct <<,
the input signal is therefore set to a slightly
higher starting point of 0.23 bar and when
the operating direction is reverse <>, to a
slightly lower starting point of 0.97 bar.
Starting point (zero)
e.g. 0.23 bar
1. Turn the zero adjustment screw (4) until
the plug stem just begins to move from
the resting position (observe plug stem
with travel indicator).
2. Reduce the input signal on the ammeter
and increase again slowly. Check
whether the plug stem starts moving at a
starting point of 0.23 bar and, if neces-
sary, correct.
Upper range value (span)
e.g. 1 bar
3. After the starting point has been ad-
justed, increase the input signal. The plug
stem must be motionless at an upper
range value of exactly 1 bar and there-
fore already moved through 100 % of its
travel range (watch the travel indicator at
the valve!). If the upper range value is in-
correct, the pin (2) must be moved as fol-
lows in order to correct the signal:
4. Move pin to:
End of lever –> to increase travel
Pivot –> to reduce travel
If the span is corrected, the zero must be
recalibrated. Afterwards, the span must also
be checked.
Keep repeating the procedure until the two
values match.
If a pressure gauge is available, check
whether the actuator is completely vented at
an instrument input signal of exactly 0.2 bar
(operating direction <<), i.e. 1.0 bar (oper-
ating direction <>).
4.3.3 Setting actuator version
“Stem retracts”
Note:
For actuators with "Actuator stem retracts",
a signal pressure which is high enough to
tightly close the valve - even with existing
upstream plant pressure - must be applied to
the diaphragm chamber. For direct operat-
ing direction <<, the upper end value of the
reference variable is 1 bar. For reverse op-
erating direction <>, the lower end value of
the reference variable is 0.2 bar.
The required signal pressure is indicated on
the adhesive label on the positioner or is
roughly estimated as in section 3.1.2.
Starting point (zero)
e.g. 1 bar
1. Adjust the instrument input signal to
1 bar.
Turn zero adjustment screw (4) until the
control valve just begins to move from
the resting position.
EB 8359-1 EN
15
Operation