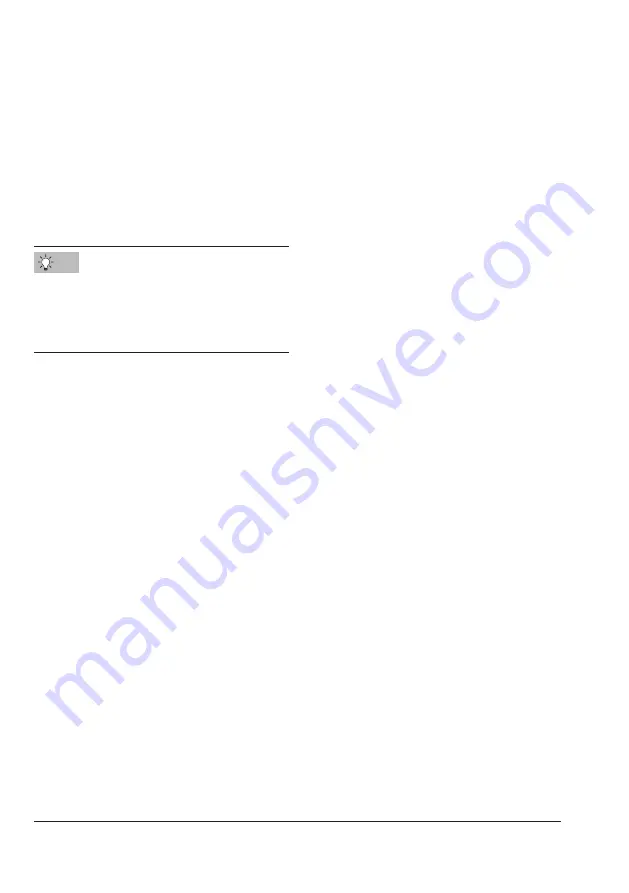
9-6
EB 3017 EN
Servicing
9.1 Preparation for service
work
1. Lay out the necessary material and tools
to have them ready for the service work.
2. Put the regulator out of operation (see
the 'Decommissioning' section).
We recommend removing the regulator from
the pipeline before performing any service
work (see the 'Removing the regulator from
the pipeline' section).
The following service work can be per-
formed after preparation is completed:
−
Replace the actuator (see section 9.3.1)
−
Replace the seat and plug (see sec-
−
Replace the actuator's operating dia
-
phragm (see section 9.3.3)
Tip
9.2 Installing the regulator
after service work
Î
Put the regulator back into operation (see
the 'Start-up' section). Make sure the re
-
quirements and conditions for start-up or
putting the valve back into operation are
met.
9.3 Service work
Î
Before performing any service work,
preparations must be made to the regu-
lator (see section 9.1).
Î
After all service work is completed, check
the regulator before start-up (see the
'Testing the regulator' section).
Summary of Contents for 42-37
Page 54: ...8 4 EB 3017 EN...
Page 66: ...11 2 EB 3017 EN...
Page 68: ...12 2 EB 3017 EN...
Page 70: ...13 2 EB 3017 EN...
Page 74: ...14 4 EB 3017 EN...
Page 83: ......