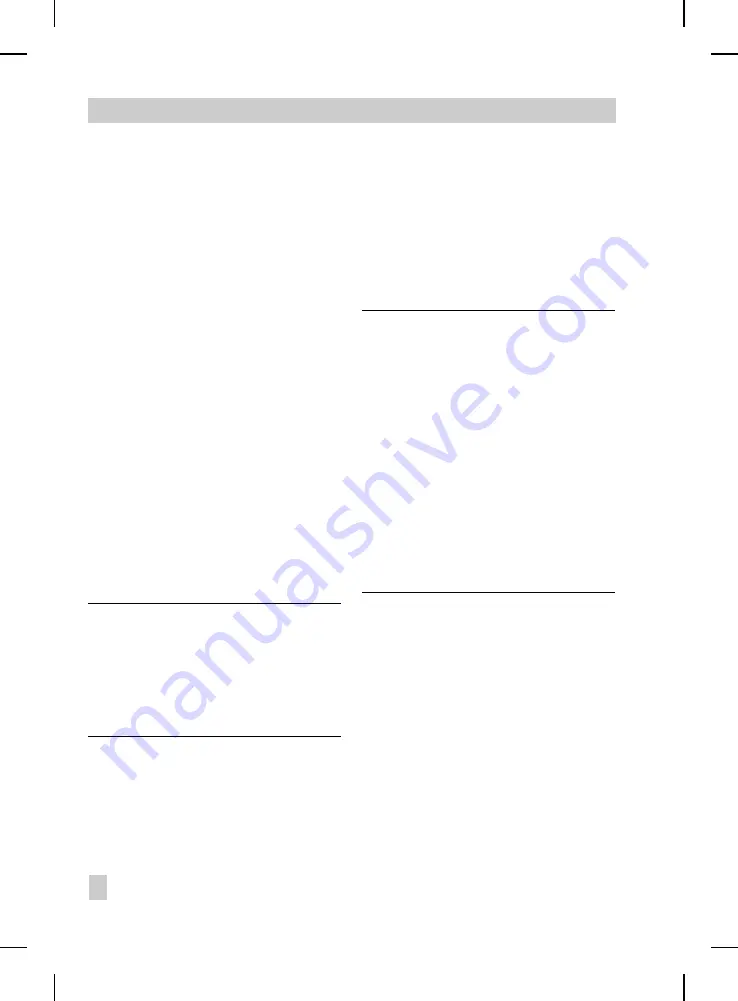
240, 350 and 700 cm
2
Actuators
6. Align
the lateral switch plate at the con-
nection block (Fig. 3) with the proper
arrow symbol on the block. This means,
the actuator symbol for "actuator stem
extends" or "actuator stem retracts"
must match the respective actuator ver-
sion used. If not, remove the two fasten-
ing screws and the switch plate, turn the
switch plate by 180
°
and reattach.
7. Place connection block with the associ-
ated sealing rings against the positioner
and the actuator yoke and screw it
tight, using the fastening screw.
For actuators with fail-safe position "ac-
tuator stem retracts", additionally
mount the prefabricated signal pressure
tube between connection block and ac-
tuator.
120 cm
2
actuator
For Type 3277-5 Actuators with 120 cm
2
,
the signal pressure is transmitted to the dia-
phragm chamber via the switchover plate
(see Fig. 3, bottom).
NOTE:
For a rated travel of 7.5 mm, a brass
throttle (see Accessories table on page 13)
must be pressed into the seal located in the
signal pressure input on the actuator yoke.
With 15 mm rated travel, this is only
required if the supply pressure exceeds 4 bar.
6. Remove the screw at the back of the po-
sitioner and close the signal pressure
output (output 38) at the side with the
associated plug included in the acces-
sory kit.
7. Mount the positioner so that the bore in
the distance plate (15) is aligned with
the seal located in the bore of the actua-
tor yoke.
8. Align the switchover plate with the
corresponding symbol for attachment
left, and screw the plate to the actuator
yoke.
NOTE:
If, in addition to the positioner, a solenoid
valve or a similar device is attached to the
120 cm
2
actuator, the rear M3 screw must
not be removed. In this case, the signal
pressure has to be fed from the signal press-
ure output to the actuator via the required
connecting plate (see Table 2). The swit-
chover plate is no longer required.
NOTE
(applicable for all actuators)
For faster control valves with a transit time <
0.6 s, replace the filter in the signal press-
ure output (output 38) with a screw-in
throttle (see Accessories table), if necessary,
to improve the control properties.
Filling the spring chamber with air
If the Type 3277 Actuator’s spring chamber
must be filled with the air exhausted from
the positioner, the spring chamber (version
"actuator stem extends") can be connected
to the connection block by means of a tube
(Table 3). For this, you need to remove the
vent plug on the connecting block.
With the Type 3277-5, version "actuator
stem retracts", the air exhausted from the
positioner is constantly applied to the spring
chamber via an internal bore.
12
EB 8382-1 EN
Attaching the positioner
Summary of Contents for 3785 series
Page 69: ...EB 8382 1 EN 69...
Page 70: ...70 EB 8382 1 EN...
Page 71: ...EB 8382 1 EN 71...
Page 72: ...72 EB 8382 1 EN...
Page 73: ...EB 8382 1 EN 73...
Page 74: ...74 EB 8382 1 EN...
Page 75: ...EB 8382 1 EN 75...
Page 76: ...76 EB 8382 1 EN...
Page 77: ...EB 8382 1 EN 77...
Page 78: ...78 EB 8382 1 EN...
Page 79: ...EB 8382 1 EN 79...