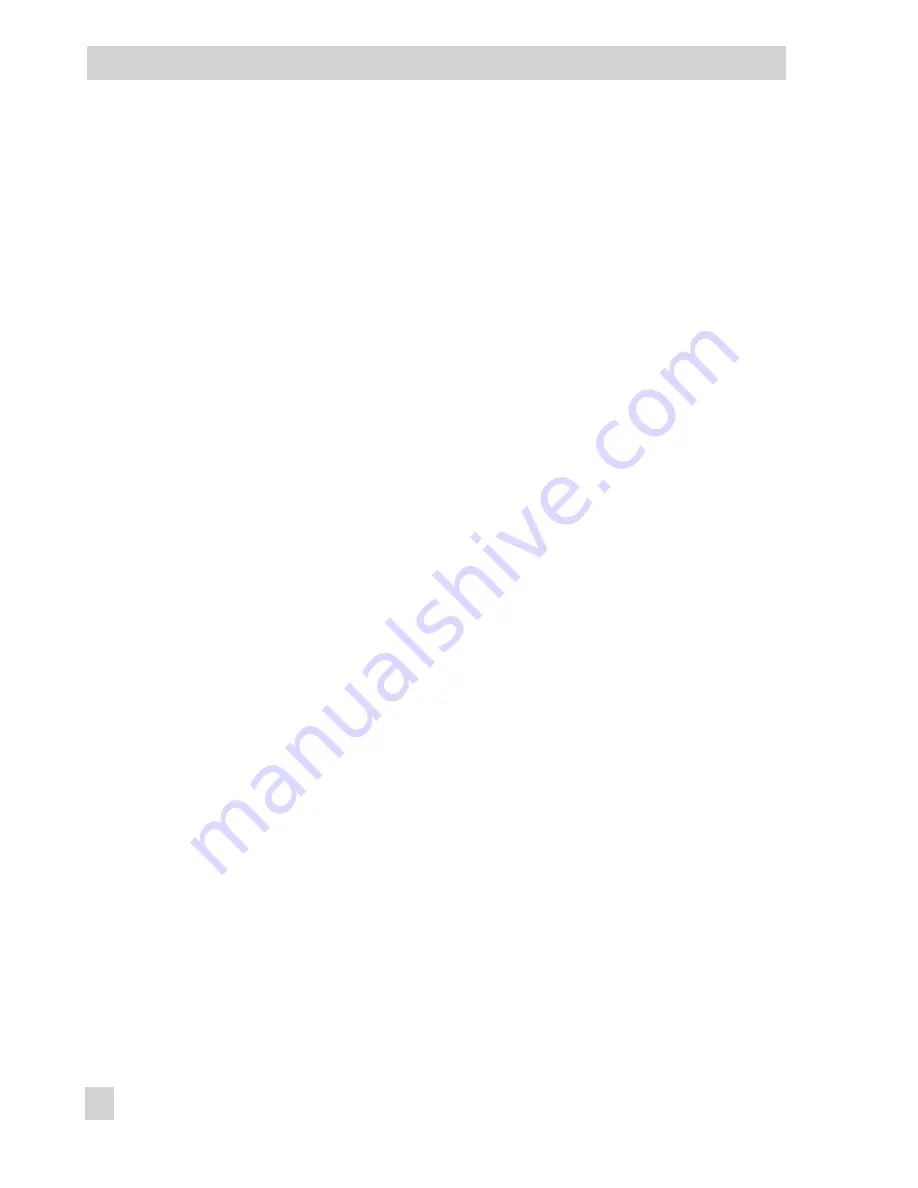
3
Design
and
principle
of
operation
The electropneumatic positioner is mounted
to pneumatic control valves and is used to
assign the valve position (controlled
variable x) to the control signal (reference
variable w). The DC control signal received
from a control unit is compared to the travel
or rotational angle of the control valve and
issues a signal pressure (output variable y).
The positioner is designed depending on the
corresponding accessories for direct attach-
ment to Type 3277 Actuators or for attach-
ment to actuators according to IEC 60534-6
(NAMUR).
Additionally, a coupling wheel included in
the accessories is required to transfer the ro-
tary motion for rotary actuators according to
VDI/VDE 3845.
Springless rotary actuators require an ac-
cessory reversing amplifier to permit the
powered operation in either direction.
The positioner basically consists of a travel
sensor system that functions proportional to
resistance, an analog i/p module with
downstream booster as well as the electronic
unit with a microcontroller. The positioner is
fitted with two adjustable software limit
switches as standard to indicate the valve's
end positions.
The position of the valve is transmitted as
linear travel motion or angle of rotation via
pick-up lever and travel sensor (2) to an an-
alog PD controller (3). Simultaneously, an
A/D converter (4) transmits the position of
the valve to the microcontroller (5). The PD
controller compares this actual position to
the 4 to 20 mA DC control signal (reference
variable) after it has been converted by the
A/D converter (4).
In case of a system deviation, the operation
of the i/p converter (6) is changed so that
the actuator (1) is filled or vented via the
downstream air capacity booster (7). This
causes the closure member of the control
valve to move to the position determined by
the reference variable.
The pneumatic air capacity booster (7) and
the pressure regulator (8) are provided with
supply air. An intermediate flow regulator
(9) with fixed settings is used to purge the
positioner and also guarantees trouble-free
operation of the pneumatic booster.
The output signal pressure supplied by the
booster can be limited to 2.4 bar by activat-
ing the parameter P9.
The volume restriction Q (10) is used to opti-
mize the positioner by adapting it to the ac-
tuator size.
Tight-closing function:
The pneumatic actuator is completely filled
with air or vented as soon as the reference
variable falls below 1 % or exceeds 99 %
(see end positions set over parameters P10
and P11).
8
EB 8384-1 EN
Design and principle of operation
Summary of Contents for 3730 Series
Page 4: ...4 EB 8384 1 EN...
Page 50: ...50 EB 8384 1 EN...
Page 54: ...54 EB 8384 1 EN...
Page 55: ...EB 8384 1 EN 55...
Page 56: ...56 EB 8384 1 EN...
Page 57: ...EB 8384 1 EN 57...
Page 58: ...58 EB 8384 1 EN...
Page 59: ...EB 8384 1 EN 59...
Page 60: ...60 EB 8384 1 EN...
Page 61: ...EB 8384 1 EN 61...
Page 62: ...62 EB 8384 1 EN...
Page 63: ...EB 8384 1 EN 63...
Page 64: ...64 EB 8384 1 EN...
Page 65: ...EB 8384 1 EN 65...
Page 70: ...70 EB 8384 1 EN...
Page 71: ...EB 8384 1 EN 71...