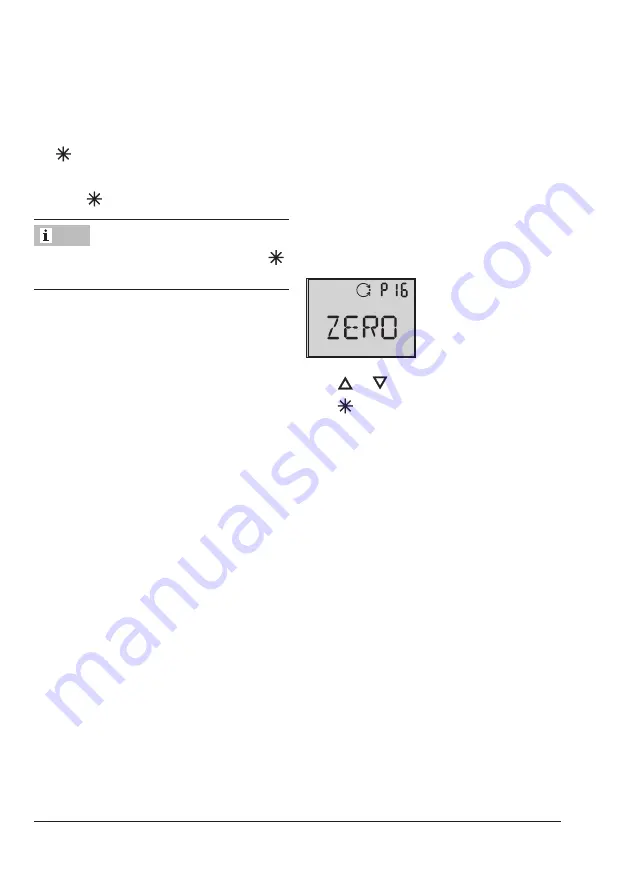
28
EB 8395 EN
Operating the positioner
Canceling initialization
The initialization can be canceled by press
-
ing .
−
ESC blinks on the display.
−
Press to confirm.
This code must be confirmed by touching
.
Otherwise, the code remains active.
Initial state 1:
Positioner has
not
been initialized
The positioner goes to the fail-safe position
after the initialization process has been can
-
celed.
Initial state 2:
Positioner is initialized
On canceling a new initialization process,
the positioner returns to closed-loop opera-
tion. The settings of the previous initialization
are used.
A new initialization can be started directly
afterwards.
7.10 Zero calibration
In case of inconsistencies in the closed posi-
tion of the valve (e.g. with soft-seated plugs),
it might be necessary to recalibrate zero. En
-
able configuration as described in sec
-
tion 7.2.
Start the zero calibration by activating Code
P16 as follows:
Press
or
until Code
P16
appears.
Press
and hold for six seconds.
6-5-4-3-
2-1-
is counted down on the display.
Zero calibration starts, the display blinks!
The positioner moves the control valve to the
CLOSED position and recalibrates the inter
-
nal electric zero point.
When the zero calibration has been success
-
fully completed, the positioner returns to
closed-loop operation (display with status in
-
dication).
Note
Summary of Contents for 3724
Page 39: ...EB 8395 EN 39...