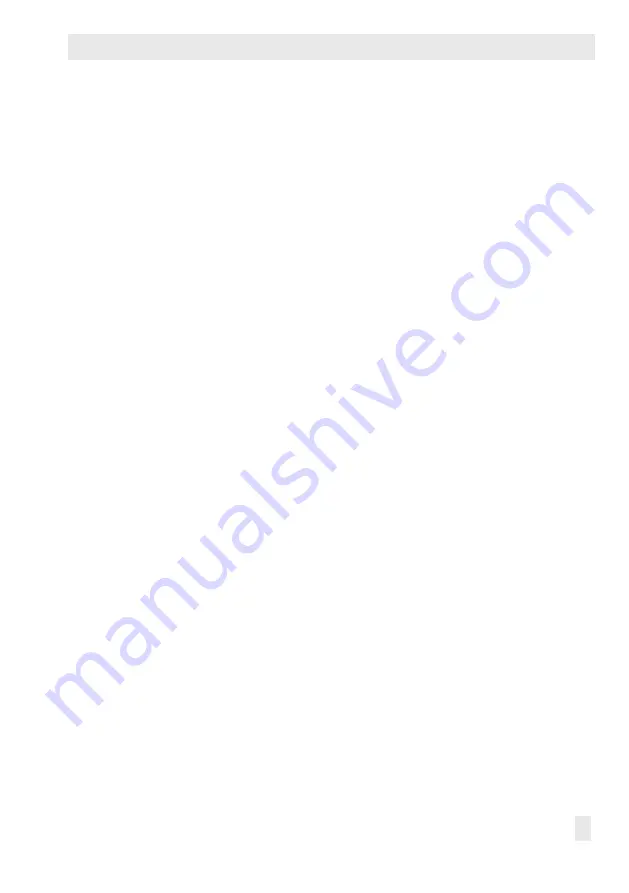
EB 2640 EN
9
Design and principle of operation
Pneumatic stem locking
Type 2371-10
To open the valve, apply a pressure p
V
(= 1 bar) to the pneumatic unit. This causes
the plug stem to move together with the plug
out of the valve seat. A set point pressure p
C
must not be applied to the regulator in this
case.
To switch the valve back to its control func
-
tion, remove the pressure p
V
(= 1 bar).
Type 2371-11
To open the valve, apply a pressure p
V
(= 6 bar) to the pneumatic unit. This causes
the plug stem to move together with the plug
out of the valve seat, opposing the spring
force.
To switch the valve back to its control func
-
tion, remove the pressure p
V
(= 6 bar).
Manual stem locking
Type 2371-11 only
To lock the stem into place, screw the pin into
the opening on top of the actuator housing
in place of the blanking plug. The end of the
pin comes to rest on the head of the set point
screw. As the pin is screwed into the valve, it
pushes the plug into the open position over
the set point screw and upper plug section.
A mechanical stop prevents it from being
screwed in any further, protecting the dia
-
phragm from overstretching or rupturing. Se-
cure the position using the lock nut.
When the groove of the pin is completely
concealed, the stem locking is active, where
-
as a visible groove means it is disengaged.