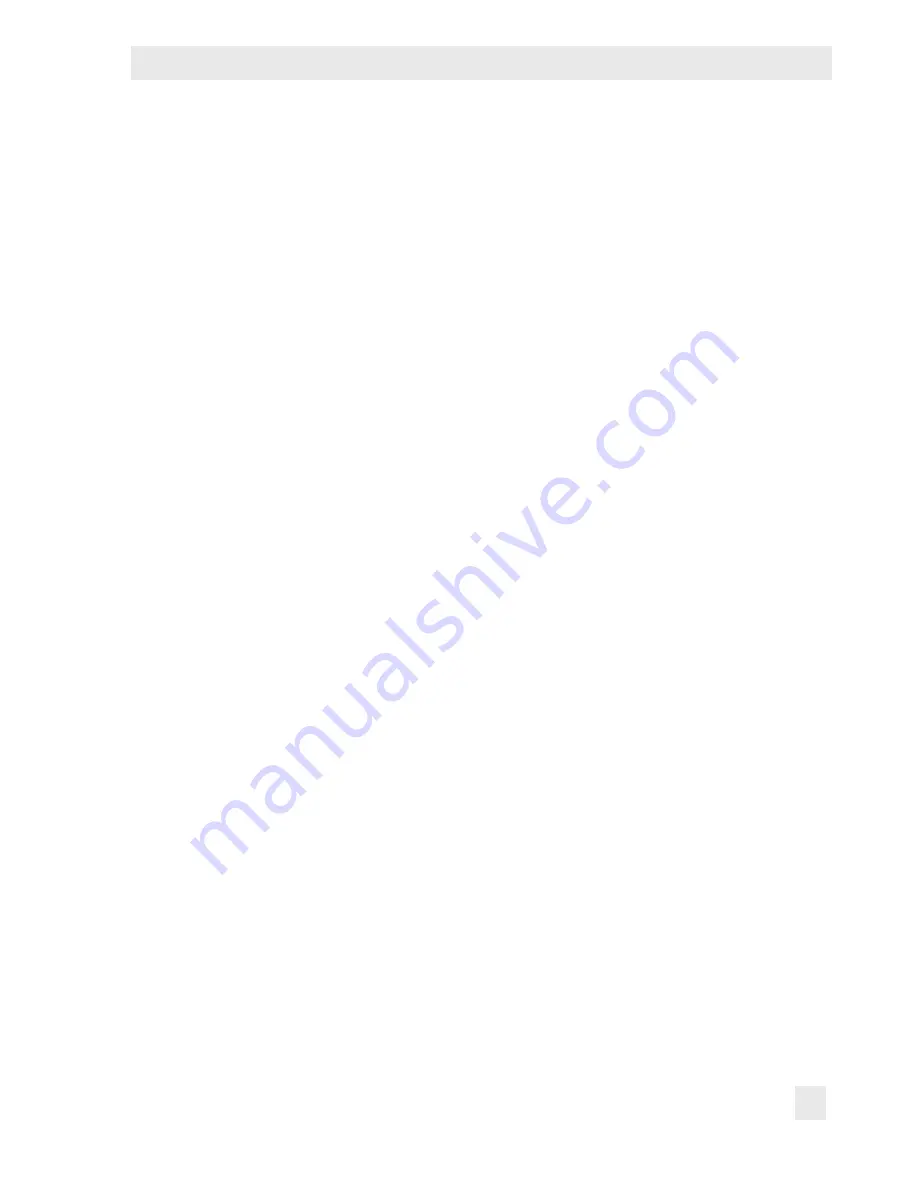
EB 2043 EN
29
Appendix
5. If necessary, allow the pipeline and de-
vice to cool down or heat up.
6. Remove the sensor from the pipeline
and, if necessary, seal the opening.
7. Remove the safety temperature monitor
from the valve.
9.2 Disposal
Î
Observe local, national and internation-
al refuse regulations.
Î
Do not dispose of components, lubricants
and hazardous substances together with
your household waste.
10 Appendix
10.1 After-sales service and
spare parts
After-sales service
Contact SAMSON's After-sales Service de-
partment for support concerning service or
repair work or when malfunctions or defects
arise.
You can reach the After-sales Service De-
partment at [email protected].
Addresses of SAMSON AG and its subsid
-
iaries
The addresses of SAMSON AG, its
subsidiaries, representatives and service
facilities worldwide can be found on the
SAMSON website (
u
www.samson.de) or in
all SAMSON product catalogs.
To assist diagnosis and in case of an unclear
mounting situation, specify the following
details (so far as possible). See section 2:
−
Device type and nominal size
−
Model number and configuration ID
−
Upstream and downstream pressure
−
Temperature and process medium
−
Min. and max. flow rate
−
Is a strainer installed?
−
Installation drawing showing the exact
location of the regulator and all the ad-
ditionally installed components (shut-off
valves, pressure gauge, etc.)
Spare parts
There are no spare parts available for the
safety temperature monitor.
10.2
Certificates
The EU declarations of conformity are in-
cluded on the next pages.