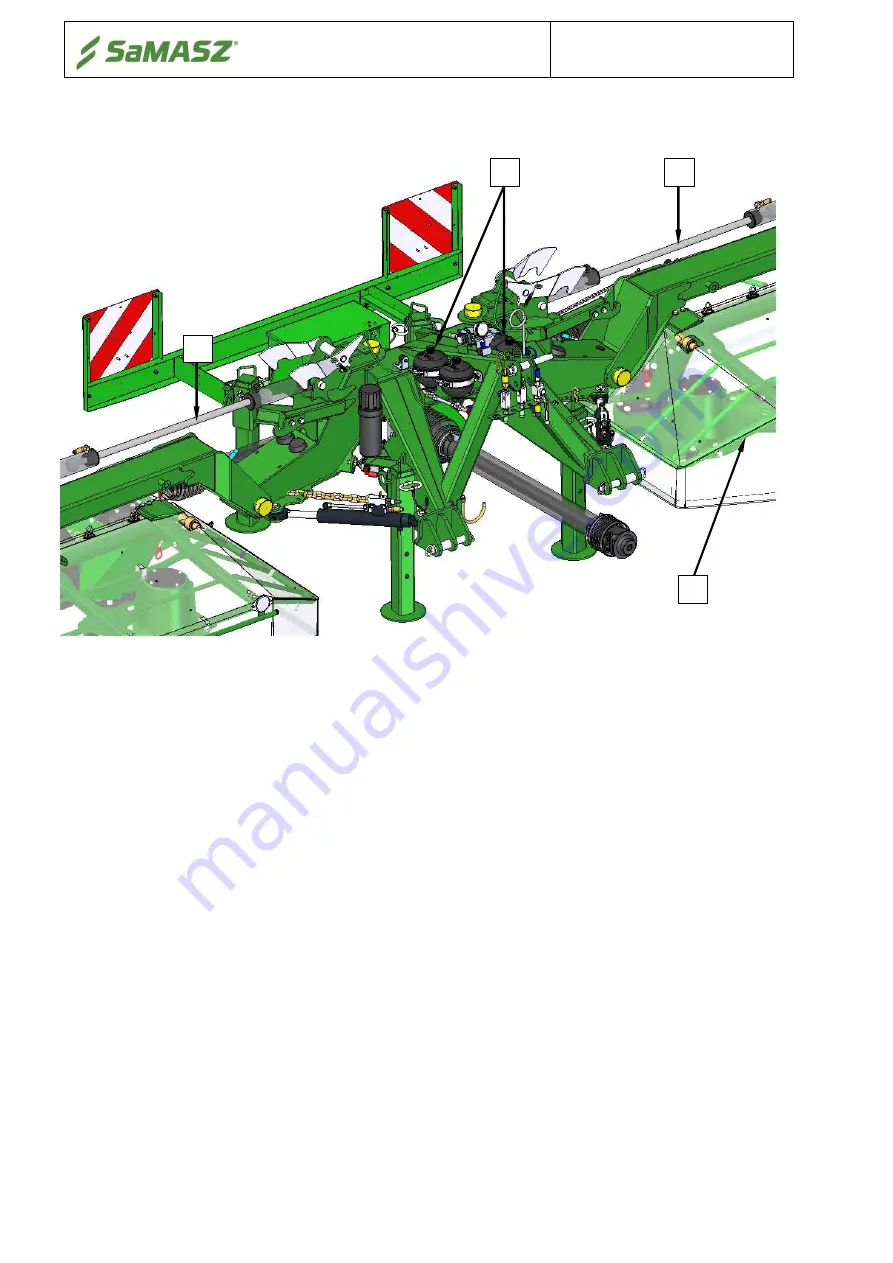
Operator’s manual
Double-sided disc mowers
with central suspension
- 10 -
3.2.6.
Double-sided disk mowers with hydro-pneumatic support
All KDD disk mowers are also offered with hydro-pneumatic support (
Fig. 4
).
Fig. 4.
Overview of rear disk mower with hydro-pneumatic support
Hydraulic lifting cylinder (
3
) and hydro-pneumatic suspension driven from the tractor external
hydraulics and hydraulic accumulators (
1
) are used to adjust the mower to working position.
3-point linkage frame, onto which cutterbar is set, features hydro-pneumatic support (
2
).
The abovementioned suspension enables the mower’s impact to the ground to be controlled by
modification of the pressure in hydraulics.
3.3.
Standard equipment and spare parts
The mowers are sold with the following standard equipment:
warranty card,
operator's manual with catalogue of spare parts
and declaration of conformity,
PTO shaft,
cutting disk with drum (2 pcs.),
spray paint (150 ml / 5.1 us fl oz),
reflective plates with lights,,
frame mounting key,
cutting disk (2 pcs.),
disk module (2 sets),
slide (2 pcs.),
slide cap (2 pcs.),
knife base (46 pcs.),
skew knife L=105mm/ 4.1
''
(180 pcs.),
knife holder (2 pcs.),
inter - skid insert (3pcs.).
Moreover, mowers with conveyers (KDD S/SL T (H)) are provided with convey belt – 1 pc.
3
1
2
3