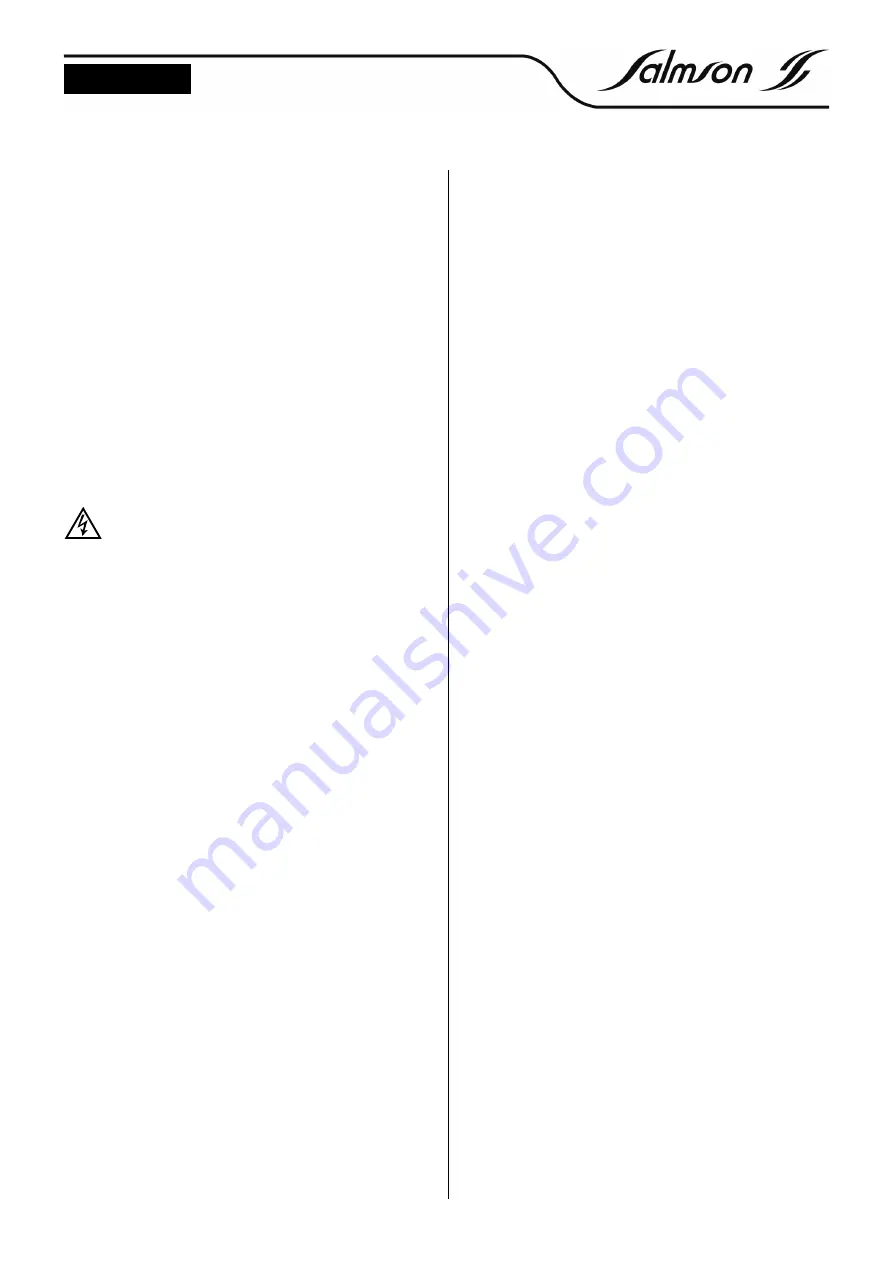
19
ENGLISH
Low-level emptying (run-down time 0-180 sec. after reaching the swit-
ch-off point) can be selected by entering the run-down time > 0 sec.
The changed parameters are stored fail-safe in the switching device.
5. INSTALLATION - ASSEMBLY
5.1 Scope of supply
Switch box YN3112 or YN 3212 complete (with installation and opera-
ting instructions).
5.2 Assembly
The switching device must be installed in a dry and frost-free loca-
tion.
The installation site should be protected against direct sunlight.
The device is mounted on the wall with 3 or 4 screws (
See FIG. 3 - 4
).
For outdoor installation, refer to the catalogue for the appropriate
accessories.
Switch box dimensions
- YN3212 : 300 mm x 320 mm x 120 mm (LxHxP)
- YN3112 : 255 mm x 180 mm x 180 mm (LxHxP
5.3 Electrical connections
The electrical connection must be made by a qualified elec-
trician in accordance with the local regulations.
- Check that the mains current and voltage comply with the data on
the rating plate.
- Mains fuse (max. 25 A, time-lag) and FI protection switch to be pro-
vided in accordance with local regulations.
- Pump/unit must be earthed in compliance with regulations.
- Feed cable ends of the mains and pump connecting cables
through the screwed cable glands and cable inlets and wire
according to the marking on the terminal strips.
- Power is supplied via the terminals designated PE, N, L1, L2, L3.
5.3.1 Electrical connections YN3112
Mains connection to terminals L1, L2, L3, PE (See FIG. 5) :
3 ~ 400 V + PE, 4-wire cable, cable to be provided on site.
The right rotary field is applied to the mains connection terminals.
The pump is connected directly to the motor contactor on terminals
2, 4 and 6. The earthed conductor is connected to the remaining PE
terminal.
Mains connection to terminals L1, N, PE (See FIG. 6) :
1 ~ 230 V + N + PE, 3-wire cable, cable to be provided on site.
The lead is connected with the phase to terminal L1 and the neutral
conductor to terminal N. The pump is connected directly to the
motor contactor at terminals 4 (phase) and 6 (neutral conductor).
The earthed conductor is connected to the remaining PE terminal.
Terminals 20 and 21 (WSK1) :
The bimetal contact, which automatically releases the pump after it
has cooled down, is connected to terminals 20 and 21 on the top cir-
cuit board.
Terminals 21 and 22 (WSK2) :
The bimetal contact, which only releases the pump after acknow-
ledgment, is connected to terminals 21 and 22 on the top circuit
board.
Configuration is via software.
Terminals 32 and 33 :
Terminals 32 and 33 on the top circuit board are provided for the
connection of an external acknowledge button.
Terminals 1 and 2 :
Terminals 1 and 2 have no function.
Terminals 3 and 4 :
Terminals 3 and 4 are used for a potential-free collective fault indica-
tion. The contact is closed in the case of an alarm, power failure and
when the main switch is off.
Terminals 5 and 6 :
Terminals 5 and 6 are used for the max. water level alarm (potential-
free).
The contact is closed in the case of an alarm.
Terminals 3 and 4 are active with any kind of fault, i.e. also in case of
a max. water level alarm.
If the interval alarm is activated via software, these alarm outputs are
operated, so that the blinking light can be replaced by a less expen-
sive indicator light.
Terminals 12 and 17 (floats switch) :
Float switches can be connected to terminals 12 to 17.
The display shows which switch is closed.
The contact of the float switch must be closed when the level is rea-
ched or exceeded. When the float switches are used in explosive
areas, isolating switch amplifiers must be provided.
Terminals 12 and 13
Level OFF
Terminals 14 and 15
Level ON
Terminals 16 and 17
Max. water level alarm
Terminals 13, 15, 17 are interconnected, so that also a common
conductor can be used.
Terminals 34 and 35 :
An external sensor (0-1 mCW) with an output signal of 4-20mA in two-
wire technique can be connected to terminals 34 (-) (green wire)
and 35 (+) (brown wire). The sensor is supplied with a stabilised DC
voltage of approx. 20V. Make sure to check the polarity. When the
sensor is used in explosive areas, a safety barrier must be provided.
When using and setting the electronic level sensor, a float switch can
be connected to the terminals for the max. water level alarm (termi-
nals 16 and 17) for added safety. Upon activation of the float switch,
the pump is forced to operate and the condition is indicated via the
alarm contact (terminals 5 and 6). When the value has dropped
below the alarm level, the pump is switched off immediately or after
expiry of the set run-down time.
5.3.2 Electrical connections YN3212
Mains connection to terminals L1, L2, L3, PE (See FIG. 7) :
3 ~ 400 V + PE, 4-wire cable, cable to be provided on site.
The right rotary field is applied to the mains connection terminals.
Pump 1 is connected to terminals 27, 28 and 29 and pump 2 to ter-
minals 34, 35 and 36. The earthed conductor is connected to the
remaining PE terminal.
Mains connection to terminals L1, N, PE (See FIG. 9) :
1 ~ 230 V + N + PE, 3-wire cable, cable to be provided on site.
Pump 1 is connected to terminals 27 and 28 and pump 2 to terminals
34 and 35. The earthed conductor is connected to the remaining PE
terminal.
Signal and indication contacts (See FIG. 8 - 10)
Terminals 31 - 32 (WSK1, pump 1) and 38 - 39 (WSK1, pump 2) :
The bimetal contact, which automatically releases the pumps after
they have cooled down, is connected to terminals 31 and 32
(pump 1) and 38 and 39 (pump 2). Deactivation is via software.
Terminals 32 - 33 (WSK2, pump 1) and 39 - 40 (WSK2, pump 2) :
The bimetal contact, which does not release the pump until after
acknowledgment, is connected to terminals 32 and 33 (pump 1) and
39 and 40 (pump 2).
Terminals 1 and 2 :
Terminals 1 and 2 have no function.
Terminals 3, 4 and 5 :
Terminals 6, 7 and 8 and terminals 9, 10 and 11 are used for a poten-
tial-free fault indication for pump 1 and pump 2 respectively.
The contact is closed in the case of an alarm, power failure and
when the main switch is off (between terminals 3 and 4).
Terminals 6 to 11 :
Terminals 6, 7 and 8 and terminals 9, 10 and 11 are used for a poten-
tial-free fault indication for pump 1 and pump 2 respectively.
Summary of Contents for YN3200
Page 3: ...3 E D B A C FIG 1 E D C B A FIG 2 164 238 FIG 3 1 2 280 210 220 FIG 4 2 1 1 2 ...
Page 4: ...4 FIG 5 YN3112 T4 ...
Page 5: ...5 FIG 6 YN3112 M ...
Page 6: ...6 FIG 7 YN3212 T4 ...
Page 7: ...7 FIG 8 YN3212 T4 ...
Page 8: ...8 FIG 9 YN3212 M ...
Page 9: ...9 FIG 10 YN3212 M ...