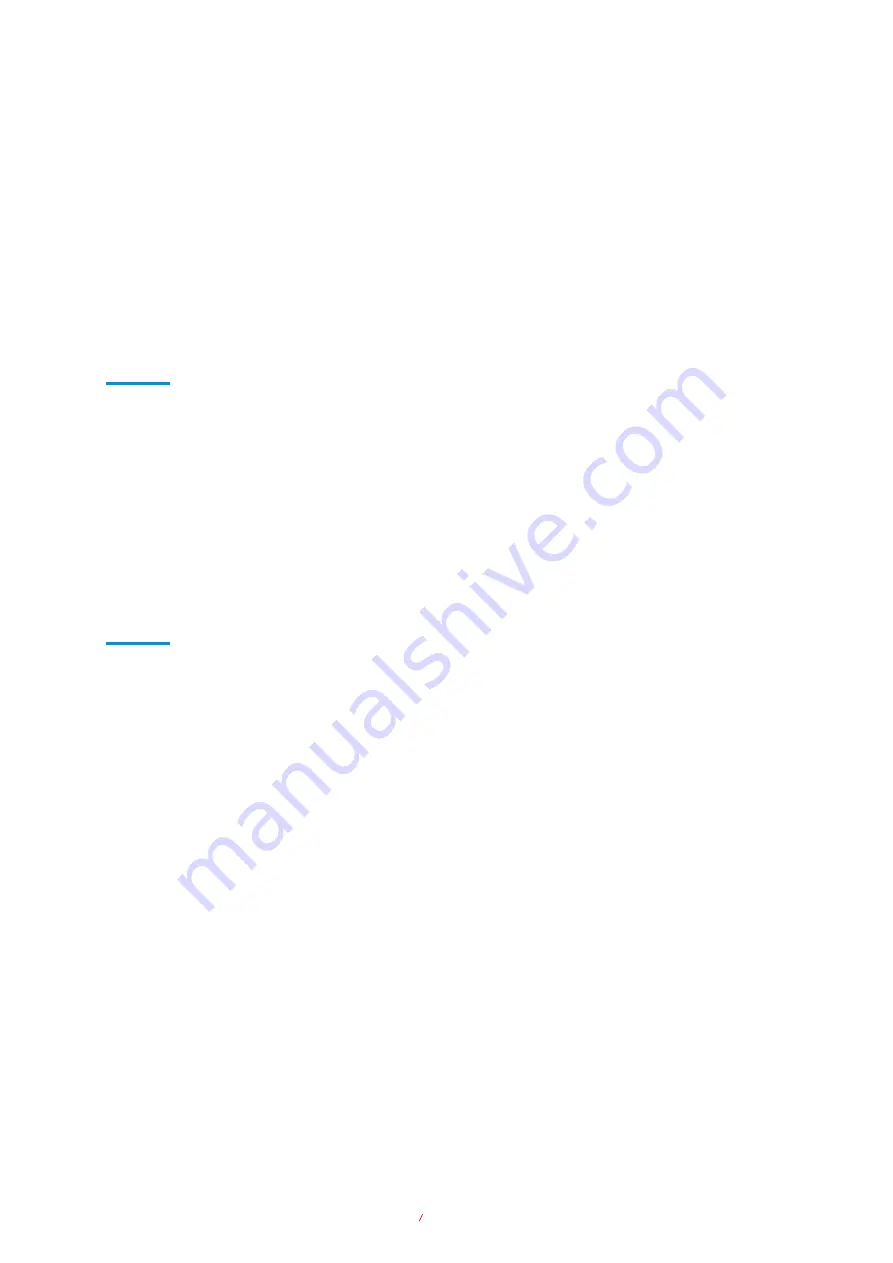
VISION-LITE® / VISION-LITE II®
PROCESSING GUIDELINES
MAY 2022
12
3. Processing of VISION-LITE® RANGE
All the recommendations outlined in § 2.4 remain valid.
•
Ensure, as much as possible, that the coating does not come in contact with guide rollers on the line;
the coating must be turned towards the operator when facing the line. If it has to go through, make
sure the conveying belts are perfectly clean and free from any abrasive material / particle;
•
Hoisting and handling instruments, tools and vacuum cups must be kept perfectly clean (or covered
with adapted caps) so as not to leave traces on the coating;
•
Wear dry and clean safety gloves when lifting the glass sheet manually. Limit area of contact as
much as possible;
•
The coating must be protected from any contact with greasy substances;
In general, and
to be considered for all steps of processing
, it is important to check whether the
installation is equipped with glass sensors functioning by detecting the glass reflectance to signal the
glass presence.
In fact,
the very low reflectance of the VISION-LITE® range glass may not be detected by the sensor
and therefore it may not send the information to the equipment. This could generate inappropriate
situation and by anticipation
sensor adjustment may be required and should be checked.
Here are examples of online sensors that works to detect correctly Vision-Lite:
•
OMRON E3X-DA41-N
•
PANASONIC SUNX cx-421-T
3.1. HANDLING ON THE PRODUCTION LINES
VISION-LITE® range is cut in the same way as any other ordinary coated glass. However, the following
recommendations have to be respected:
•
Any irregularity or damage of the edges must be avoided since it is likely to increase the risk of
breakage during the toughening process;
•
Use only light vaporising cutting oil (for instance Acecut 5503 or 5250) adapted to coated glass;
•
Do not dilute or mix the cutting oil;
•
Avoid all excess of cutting oil: Max width: 1 cm;
•
As coating could face the table, cutting table must be thoroughly cleaned from all particles of glass
or other material; cleaning must be maintained throughout the cutting process. For the glass with
coating on one side only (intended for lamination), the coating must not come into contact with the
table, but be on the upper side of the glass.
•
If the installation is equipped with rollers for conveying the glass sheets, the rollers must be regularly
inspected to check whether they move. A blocked or malfunctioning roller may scratch the anti-
reflective coating.
•
For cutting operation, avoid using natural latex coated gloves as latex tends to dissolve in cutting oil.
This leaves a greasy residue on the coating which may be difficult to wash in the industrial washing
machines. Grade 5 leather or PU palmed gloves as well as NBR nitrile dipped gloves should be
preferred;
•
Cutting templates can be used but great care must be taken not to scratch the coating. Soft
protection (soft tissue, felt or cork pad) should be placed underneath the template;
•
Fine glass splinters on the coated surface should not be wiped off by hand, but blown off by
dry
and oil-free air;
•
When stacking cut sizes prior to further processing, separate the panes by either:
• New cork pads (recommended);
3.2. GLASS CUTTING