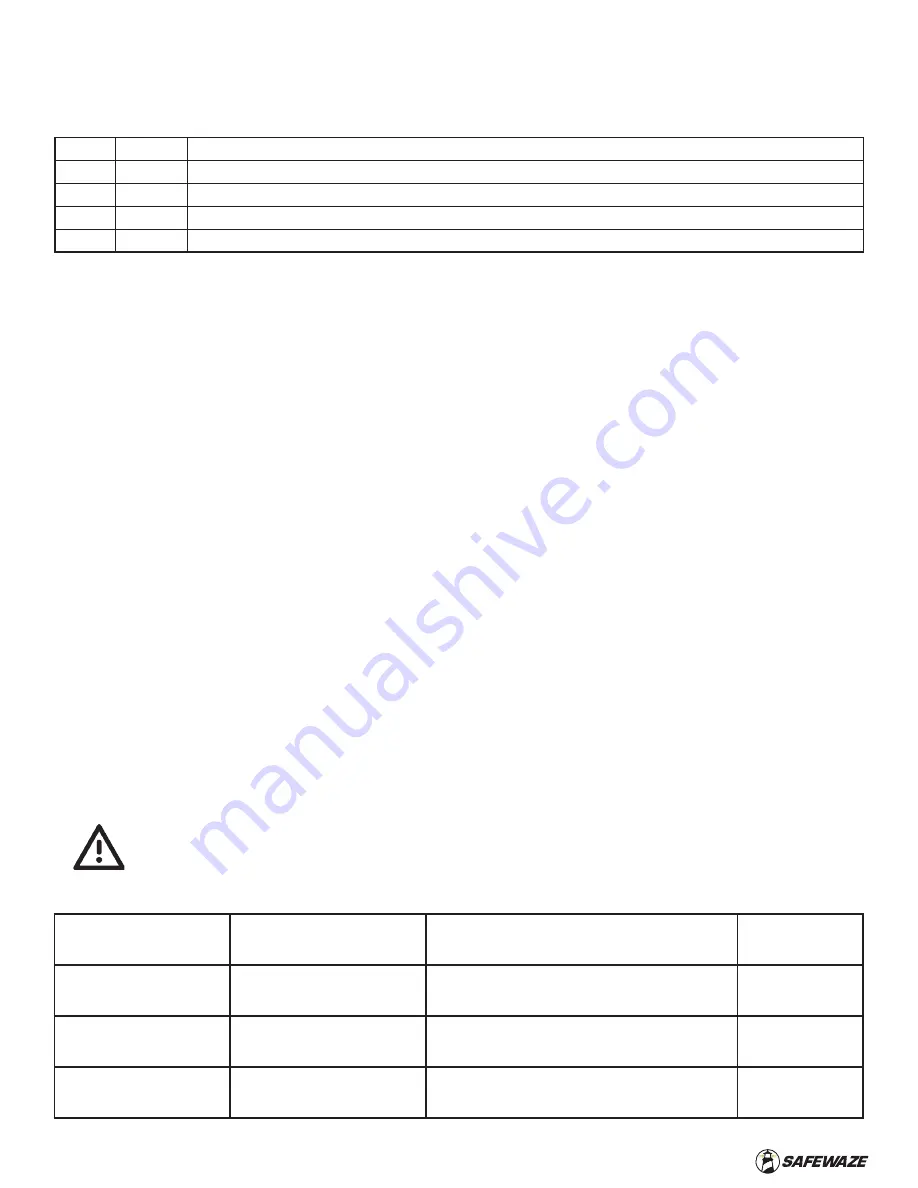
V2.0 2021 Copyright Safewaze
Page 4
ANSI Z359.0
Definitions and Nomenclature Used for Fall Protection and Fall Arrest
ANSI Z359.2
Minimum Requirements for a Comprehensive Managed Fall Protection Program
ANSI Z359.12 Connecting Components for Personal Fall Arrest Systems
ANSI Z359.14 Safety Requirements for Self-Retracting Devices for Personal Fall Arrest and Rescue Systems
ANSI A10.32
Personal Fall Protection use in Construction and Demolition
1.3 Training
This equipment is intended to be used by persons trained in its correct application and use. It is the responsibility of the user to assure they are familiar
with these instructions and are trained in the correct care and use of this equipment. Users must be aware of the operating characteristics, application,
limits, and the consequences of improper use.
2.1 Capacity
Safewaze Retractable Fall Arresters are all designed in compliance with ANSI Z359.14 to meet the weight capacity range of (130-310 lbs),
OSHA (420 lbs).
2.0 Limitations & Requirements
When installing or using this equipment always refer to the following requirements and limitations:
2.2 Anchorage
Anchorages selected for fall arrest systems shall have a strength capable of sustaining static loads applied in the directions permitted by the system of at
least:
1. 5,000 lbs. (22.2 kN) for non-certified anchorages, or
2. Two times the maximum arresting force for certified anchorages.
When more than one fall arrest system is attached to an anchorage, the strengths set forth in (1) and (2) above shall be multiplied by the number
of systems attached to the anchorage.
1.2 Standards
Safewaze SRL’s conform to the national standard(s) identified on their ID label. Refer to local, state, and federal (OSHA) requirements for additional
information concerning the governing of occupational safety regarding Personal Fall Arrest Systems (PFAS). Examples of Latitude HD SRL labeling are
located on (Page 18) of this manual.
2.4 Rescue Plan
When using this equipment, employers
must create a rescue plan, and provide the means to implement said rescue plan. This plan must be
communicated to equipment users, authorized persons, and rescuers.
From OSHA 1926.500 and 1910.66
Anchorages used for attachment of personal fall arrest systems shall be independent of any anchorage being used to support or suspend platforms, and
capable of supporting at least 5,000 lbs (22.2 kN) per user attached, or be designed, installed, and used as part of a complete personal fall arrest system
which maintains a safety factor of at least two, and is under the supervision of a qualified person.
NOTE:
Special rescue measures may be required for a fall over an edge.
TABLE 2 - ANSI STANDARDS
Type of Use
Application Examples
Conditions of Use
Inspection
Frequency
Competent Person
Infrequent to Light
Rescue and Confined Space,
Factory Maintenance
Good Storage Conditions, Indoor
or Infrequent Outdoor Use, Room
Temperature, Clean Environments
Annually
Moderate to Heavy
Transportation, Residential
Construction, Utilities, Warehouse
Fair Storage Conditions, Indoor and
Extended Outdoor Use, All Temperatures,
Clean or Dusty Environments
Semi-Annually to
Annually
Severe to Continuous
Commercial Construction, Oil and
Gas, Mining
Harsh Storage Conditions, Prolonged
or Continuous Outdoor Use, All
Temperatures, Dirty Environment
Quarterly to Semi-
Annually
1.
Authorized Person:
A person assigned by the employer to perform duties at a location where such person will be exposed to a fall hazard.
2.
Rescuer:
Person or persons other than the rescue subject acting to perform an assisted rescue by operation of a rescue system.
2.3 INSPECTION FREQUENCY
Either the Authorized Person¹ (User) or the Rescuer² must inspect this equipment prior to each use. The Inspection table (Table 3), should be used to
determine proper inspection frequency. The Inspection Checklist (Page 20) describes proper inspection procedures. The Competent Person should
record inspection results in the Maintenance Log (Page 21) of this manual. Annual inspections by a Competent Person other than the user must be
recorded in the Inspection Log (Page 22).
TABLE 3 - INSPECTION SCHEDULE PER ANSI Z359.14