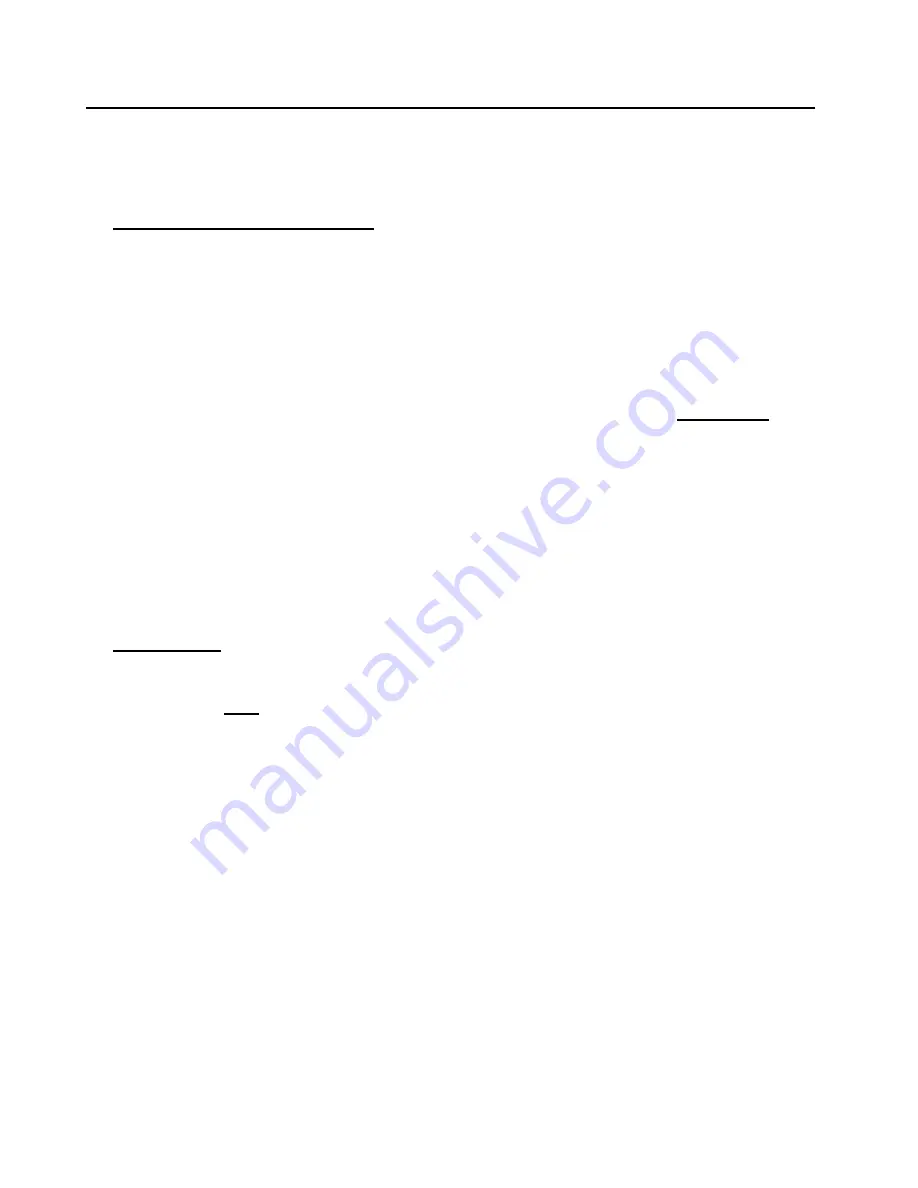
17
C. MAINTENANCE
The glue reservoir must be cleaned regularly of burnt glue build-up. Care must be taken not to
bend or damage the thermocouple during the cleaning process. The cleaning frequency will vary
depending on amount of usage, temperature range of glue being used and type of glue being used.
Every eight (8) hours of operation
Lubricate the glue spindle drive chain with a high quality chain lubricant.
Open the end access covers using the 1/8” hex wrench provided, and using compressed
air, blow through the area below the machine to remove cuttings, which may have
escaped the dust collection system.
Spray the end trim guillotines with WD-40 or equivalent to reduce glue and particle build-
up.
Raise power feeder and while it is operating, hold a damp cloth to the bottom of the belt,
to remove build-up that may affect belt traction and feed consistency.
WARNING: Use
caution when doing this and keep hands away from trim bits and end cutters that may
be inadvertently turned on. A safe way to avoid accidentally turning routers on while
cleaning belt, is to switch the manual switches situated on the routers, to the “OFF”
position.
Periodically, the four (4) blue slide strips mounted on the tabletop should be cleaned and
lubricated with WD-40 or an antifriction spray such as “Top Cote”.
Inspect and clean the tracer bearings to make sure they are clean and free of debris. These
bearing are located in front of the upper and lower router bits. The bearings ride on the
material as the trimming takes place.
Once a month
With the locating shoulder screw removed, lift the power feeder to its highest position and
apply a
light
coat of high quality grease to the feeder support post.