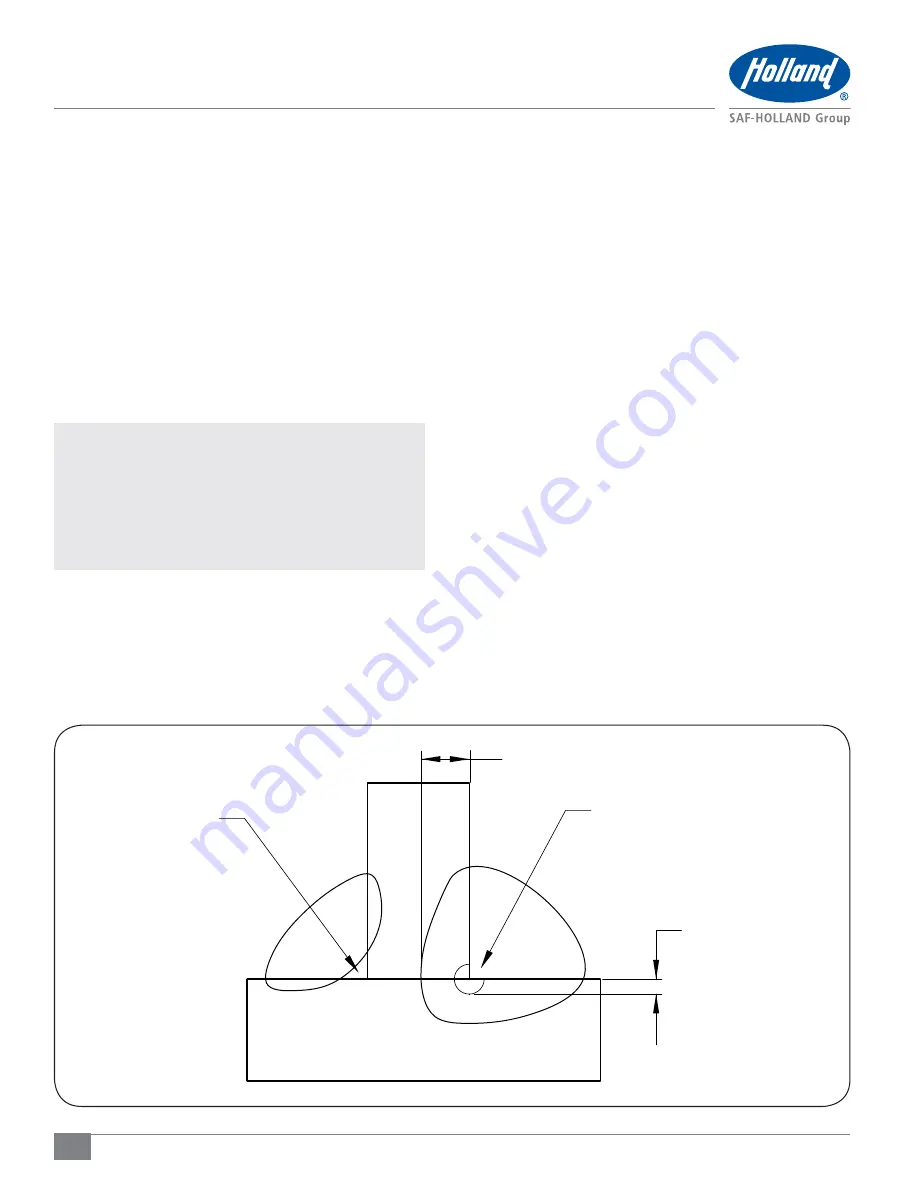
2
XL-TG20004BM-en-US · 2014-01-14 · Amendments and Errors Reserved · © SAF-HOLLAND, Inc., SAF-HOLLAND, HOLLAND, SAF,
and logos are trademarks of SAF-HOLLAND S.A., SAF-HOLLAND GmbH, and SAF-HOLLAND, Inc.
Welding Standards
2. Welding Standards
2.1 Scope
This specification applies to all components supplied by
SAF-HOLLAND
®
, and its products. The customer assumes
all responsibility for weld integrity if weld material and
procedure differ from that listed below.
2.2 Material
Frame attachment components made from low carbon or
high-strength alloy steel are to be welded with AWS filler
metal specification AWS A5.18, filler metal classification
ER-70S-3, ER-70S-6 or equivalent unless specified on the
installation drawing.
NOTE:
Any substitution for filler material from the above
standard MUST comply, as a minimum, with the
following mechanical properties:
Tensile Strength - 72k psi (496 MPa)
Yield Strength - 60k psi (414 MPa)
$IBSQZ7OPUDIGUMCT /tNBU
o
F (-17.7
o
C)
% Elongation - 22%
The recommended welding gas for gas metal arc welding
(GMAW) is 90% Argon / 10% CO2. If a different gas is used,
welds MUST comply with penetration requirements shown
(Figure 1)
. Where the installation drawing specifies different
than above, the drawing shall prevail.
2.3 Procedures
Tack welds used for positioning components are to be
located in the center of the final weld, where practical. Tack
weld should be completely fused to the finish weld. DO NOT
break arc at the end of the weld. Back up all finish welds
at least 1/2" (12.7 mm) or a sufficient amount to prevent
craters at the end of the weld. Where weld is shown to go
around corners, it is assumed the corner represents a stress
concentration area. DO NOT start or stop weld within 1" (25.4 mm)
of the corner. Particular care should be taken to prevent
undercutting in this area.
2.4 Workmanship
It is the responsibility of the customer to provide good workmanship
when attaching components to the frame structure.
2.5 Weld Size
If weld size is not specified, the effective throat of the weld
MUST be no smaller than the thinnest material being welded
(Figure 1)
.
Figure 1
LACK OF FUSION OF
ANY KIND IN THIS AREA
IS NOT ACCEPTABLE AT
ANY TIME
PENETRATION AS MEASURED
THROUGH SEAM
TARGET PENETRATION TO BE
10% OF THINNEST MATERIAL
FROM INTERSECTION OF FILLET
AS SHOWN
TARGET PENETRATION