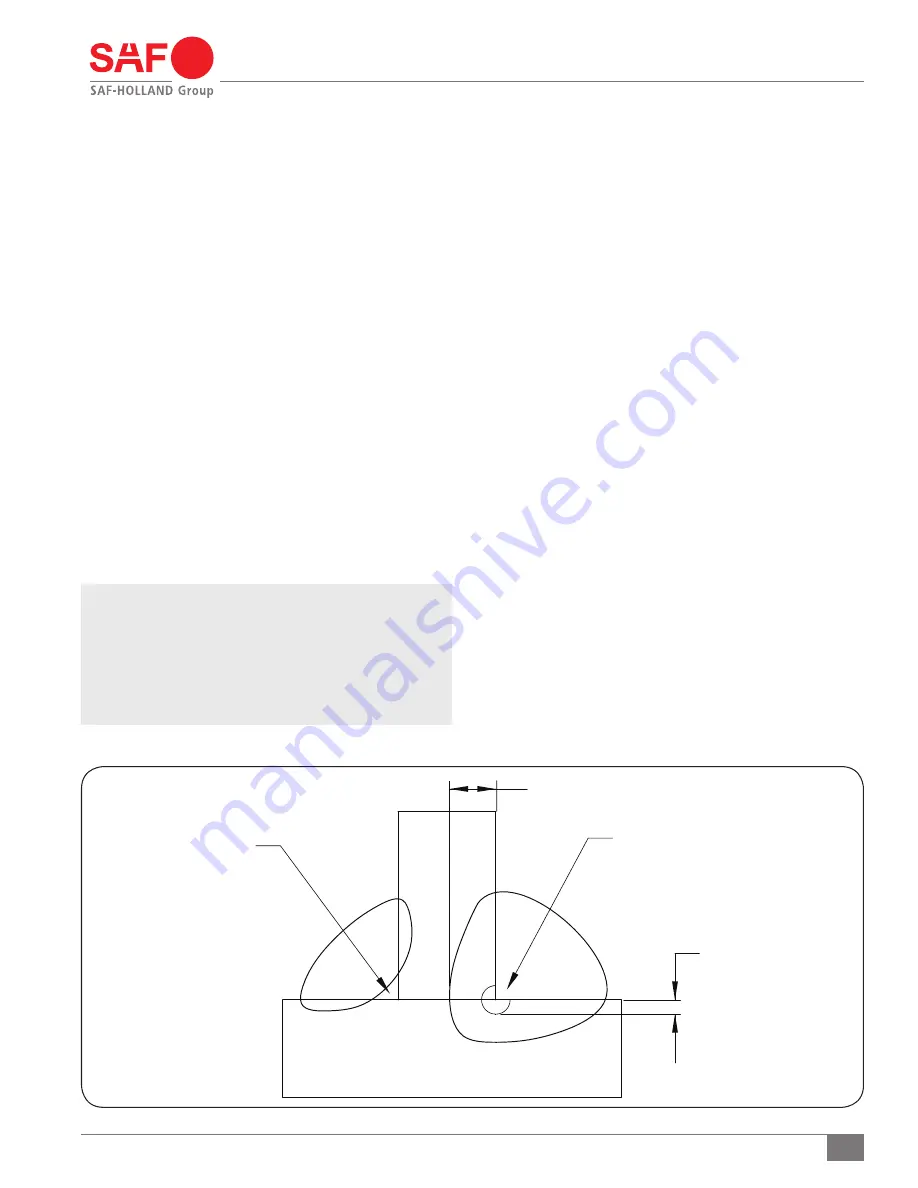
XL-AS20053BM-en-US · 2016-09-27 · Amendments and Errors Reserved · © SAF-HOLLAND, Inc., SAF-HOLLAND, HOLLAND, SAF,
and logos are trademarks of SAF-HOLLAND S.A., SAF-HOLLAND GmbH, and SAF-HOLLAND, Inc.
Welding Standards
9
6. Welding Standards
6.1 Scope
The SAF
®
suspension has been designed to be installed on a
trailer with no welding required. When welding is required for
suspension repairs, observe the requirements below. Customers
may not weld on an SAF
®
suspension without our prior approval,
including the application of the American Welding Society standards
by SAF-HOLLAND
®
engineering. This specification applies to
all components supplied by SAF-HOLLAND
®
, and its products.
The customer assumes all responsibility for weld integrity if
weld material and procedure differ from those listed below.
6.2 Workmanship
All welding on SAF-HOLLAND
®
products MUST be performed
by a welder qualified according to the appropriate AWS
standard for the weld being made or an equivalent standard.
It is the responsibility of the customer to provide good
workmanship when welding on SAF-HOLLAND
®
products.
6.3 Material
Items to be welded that are made from low carbon or high-strength
alloy steel are to be welded with AWS filler metal specification
AWS A5.18, filler metal classification ER-70S-3, ER-70S-6 or
equivalent unless specified on the installation drawing.
NOTE:
Any substitution for filler material from the above
standard must comply, as a minimum, with the
following mechanical properties:
Tensile Strength - 72k psi (496 MPa)
Yield Strength - 60k psi (414 MPa)
Charpy V Notch - 20 ft.-lbs. (27 N•m) at 0
o
F (-17.7
o
C)
% Elongation - 22%
The recommended welding gas for gas metal arc welding
(GMAW) is 90% Argon / 10% CO2. If a different gas is used,
welds must comply with penetration requirements illustrated
(Figure 10)
. Where the installation drawing specifies
different than above, the drawing shall prevail.
6.4 Procedures
Tack welds used for positioning components are to be located
in the center of the final weld, where practical. Tack weld
should be completely fused to the finish weld. DO NOT
break arc at the end of the weld. Back up all finish welds
at least 1/2" (12.7 mm) or a sufficient amount to prevent
craters at the end of the weld. Where weld is illustrated to go
around corners, it is assumed the corner represents a stress
concentration area. DO NOT start or stop weld within 1" (25.4 mm)
of the corner. Particular care should be taken to prevent
undercutting in this area.
6.5 Weld Size
If weld size is NOT specified, the effective throat of the weld
MUST be no smaller than the thinnest material being welded
(Figure 10)
.
Figure 10
LACK OF FUSION OF
ANY KIND IN THIS AREA
IS NOT ACCEPTABLE AT
ANY TIME
PENETRATION AS MEASURED
THROUGH SEAM
TARGET PENETRATION TO BE
10% OF THINNEST MATERIAL
FROM INTERSECTION OF FILLET
AS ILLUSTRATED
TARGET PENETRATION
Summary of Contents for CBXA 40
Page 2: ......