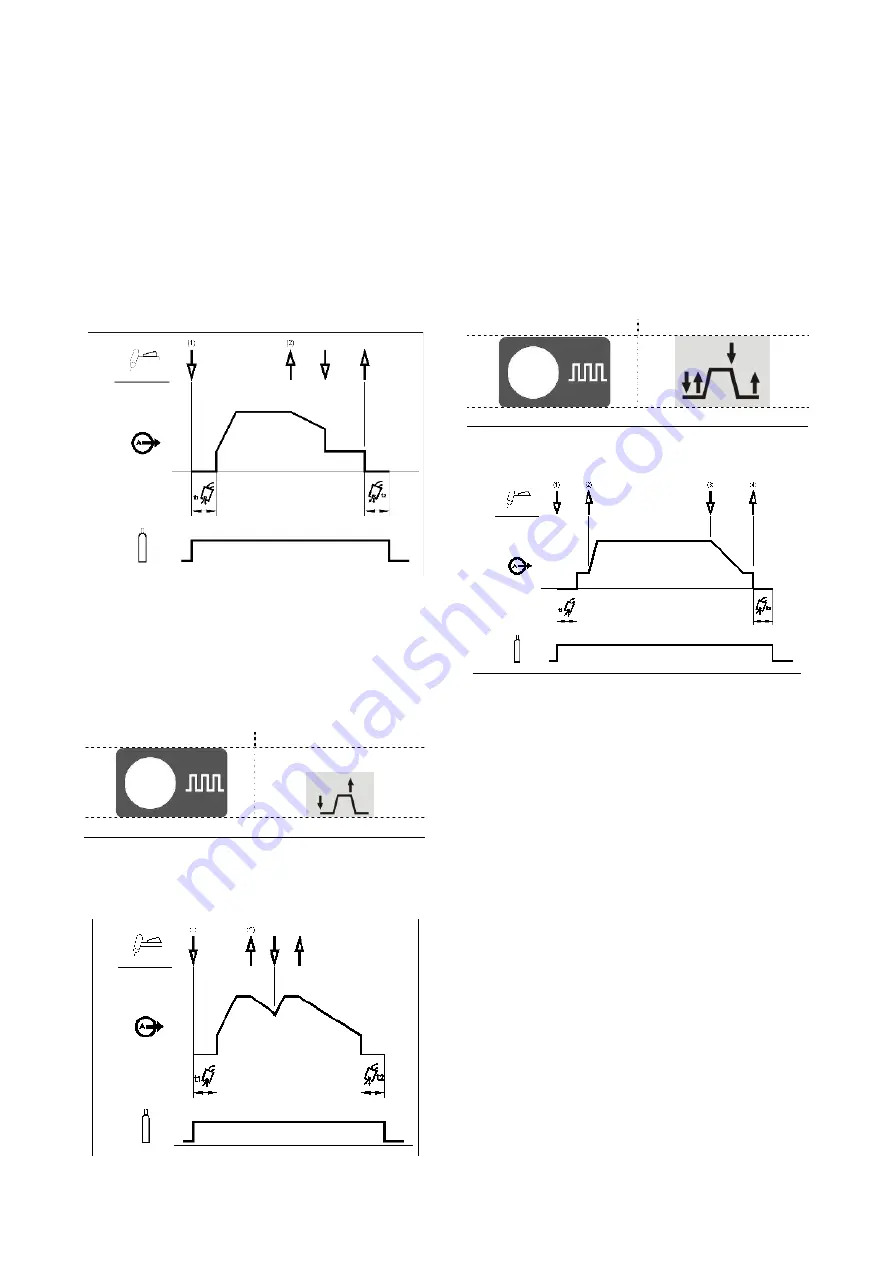
English 13 English
be increased at a controlled rate, or upslope time, until
the Welding current is reached.
If the torch trigger is released during the upslope time
the arc will stop immediately and the output of the
machine is turned OFF.
2. Release the TIG torch trigger to stop welding. The
machine will now decrease the output current at a
controlled rate, or downslope time, until the Crater
current is reached and the output of the machine is
turned OFF.
After the arc is turned OFF, the gas valve will remain
open to continue the flow of the shielding gas to the
hot electrode and work piece.
As shown above, it is possible to press and hold the TIG
torch trigger a second time during downslope to end the
downslope function and maintain the output current at the
Crater current. When the TIG torch trigger is released the
output will turn OFF and the postflow time will start. This
operation sequence, 2-step with restart disabled, is the
default setting from the factory.
2-Step Trigger Sequence with Restart Option
To select 2-Step with restart sequence:
Output
Visualization
Press several times until the LED above lights up
Enter Menu GTAW and enable 2RST option.
If the 2-step restart option is enabled from the setup menu
the following sequence will occur:
1. Press and hold the TIG torch trigger to start the
sequence as described above.
2. Release the TIG torch trigger to start the downslope.
During this time press and hold the TIG torch trigger
to restart welding. The output current will increase
again at a controlled rate until the Welding current is
reached. This sequence can be repeated as many
times as necessary. When the welding is complete
release the TIG torch trigger. When the Crater
current is reached the output of the machine is
turned OFF.
4-Step Trigger Sequence
To select 4-Step sequence:
Output
Visualization
Press several times until the LED above lights up
With the 4-step trigger mode and a TIG welding mode
selected, the following welding sequence will occur.
1. Press and hold the TIG torch trigger to start the
sequence. The machine will open the gas valve to
start the flow of the shielding gas. After the preflow
time, to purge air from the torch hose, the output of the
machine is turned ON. At this time the arc is started
according to the selected welding mode. In LIFT
starting the touching current is 25A until the short
circuit is removed.
After the arc is started the output current will be at the
Start current. This condition can be maintained as
long as necessary.
If the Start current is not necessary, do not hold the
TIG torch trigger as described at the beginning of this
step. In this condition, the machine will pass from
Step 1 to Step 2 when the arc is started.
2. Releasing the TIG torch trigger starts the upslope
function. The output current will be increased at a
controlled rate, or upslope time, until the Welding
current is reached. If the torch trigger is pushed during
the upslope time the arc will stop immediately and the
output of the machine is turned OFF.
3. Press and hold the TIG torch trigger when the main
part of the weld is complete. The machine will now
decrease the output current at a controlled rate, or
downslope time, until the Crater current is reached.
Summary of Contents for PRESTOTIG 200 AC/DC
Page 2: ......
Page 313: ...I 12 05 1 2 3 5 5 WEEE 26 26 REACh 26 26 26 27...
Page 315: ...2 01 11 A IEC 61000 3 11 IEC 61000 3 12 83 0 6 A...
Page 316: ...3 01 11 Lincoln Electric CE CE 2006 25 EC EN 12198 2 15 EN169...
Page 317: ...4 HF TIG GTAW TIG GTAW 85 8...
Page 323: ...10 4 5 A 9 1 2 1 M 1 SAVE 2 M 2 RECALL 3 M 3 MEM SET 3 3 3 MEM SAVE...
Page 326: ...13 5 2 2 2 TIG 1 TIG 25 LIFT 2 TIG TIG TIG 2 2 2 GTAW 2RST 2 1...
Page 329: ...16 2 SEL A2 2 TIG LIFT TIG ON TIG ON...
Page 436: ......