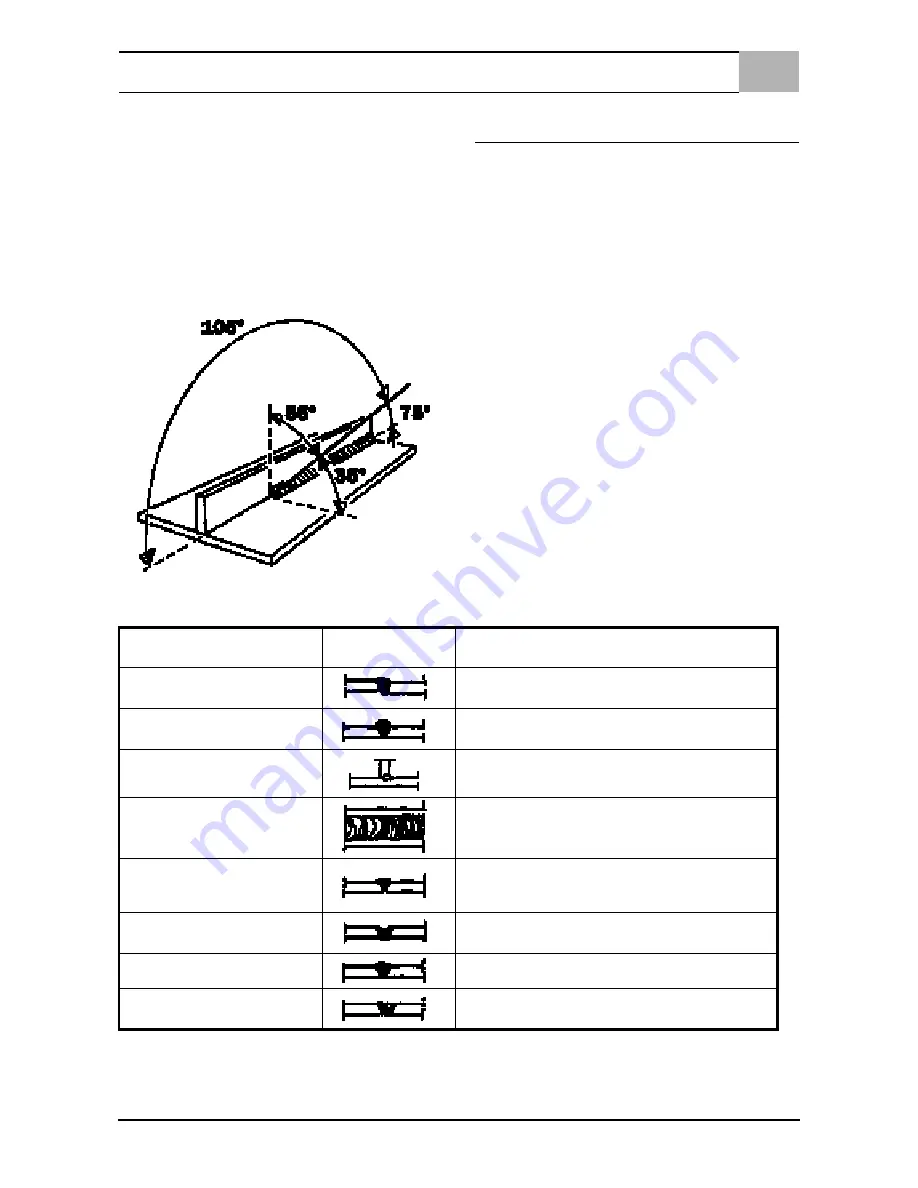
4 EN
MIG WELDING FAULTS FAULT CLASSIFICATION AND DESCRIPTION
EN
CAUTION: SCREEN GAS FLOW WHEN OPERATING IN OUT-
DOOR OR VENTILATED SITES; WELDING OPERATIONS
MAY NOT BE PROTECTED DUE TO DISPERSION OF INERT
SHIELDING GASES.
5.1
WELDING
1.
Open the gas valve of the regulator and set a flow, depending
on the welding position chosen. Fix the earth clamp to the
piece to be welded in a point free of rust, plastic and paint.
2.
Select the welding current; bear in mind that the thicker the
material, the greater the power required. The first positions
on the switch are suitable for welding less thick material.
Remember also that each position has its own wire speed,
which can be selected using the wire feed knob (Ref.1 - Pic-
ture 1 Page 3.).
6.0
MIG WELDING FAULTS FAULT CLASSIFICA-
TION AND DESCRIPTION
MIG welds may be affected by various defects, which are impor-
tant to identify.
These faults do not differ in form or nature from those encountered
during manual arc welding with coated electrodes.
The difference between the two applications lies rather in the fre-
quency of defects: porosity, for example, is more common in MIG
welding, while inclusion of slag is only encountered in welding with
coated electrodes.
The causes and prevention of faults are also quite different.
6.1
FORM
1.
Level variations.
2.
Excess thickness (over-convex bead).
3.
Insufficient metal (concave or soft beads,poorly filled cavi-
ties).
4.
Untidy beads.
In the above cases, the cause could be poor preparation of edges
(lack of support, distances too wide or too narrow), incorrect
equipment setting or improper work method.
The following table illustrates the various faults.
For best welding results, hold the torch and follow the
direction shown in the figure.
FAULT
APPEARANCE
CAUSE AND REMEDY
UNEVEN LEVEL
- Poor preparation
- Align edges and hold during spot welding.
EXCESS THICKNESS
- No-load voltage or welding speed too low.
- Incorrect torch inclination.
- Wire diameter too large.
INSUFFICIENT METAL
- Welding speed too high.
- Welding voltage too low for welding application.
OXIDISED BEAD
- Weld in the channel if using a long arc.
- Regulate voltage.
- Wire is bent or over-protruding from the wire guide tube.
- Incorrect wire feed speed.
INSUFFICIENT PENETRATION
- Incorrect torch inclination.
- Irregular or insufficient distance.
- Wire guide tube worn.
- Wire speed too slow for voltage used or for welding speed.
OVER PENETRATION
- Wire speed too high.
- Incorrect torch inclination.
- Excessive distance.
LACK OF FUSION
- Distance too short.
- Rough out or grind the weld, then repeat.
CHANNELS
- Welding speed too high.
(This fault is easily detected on sight by the welder, and should be cor-
rected immediately.)