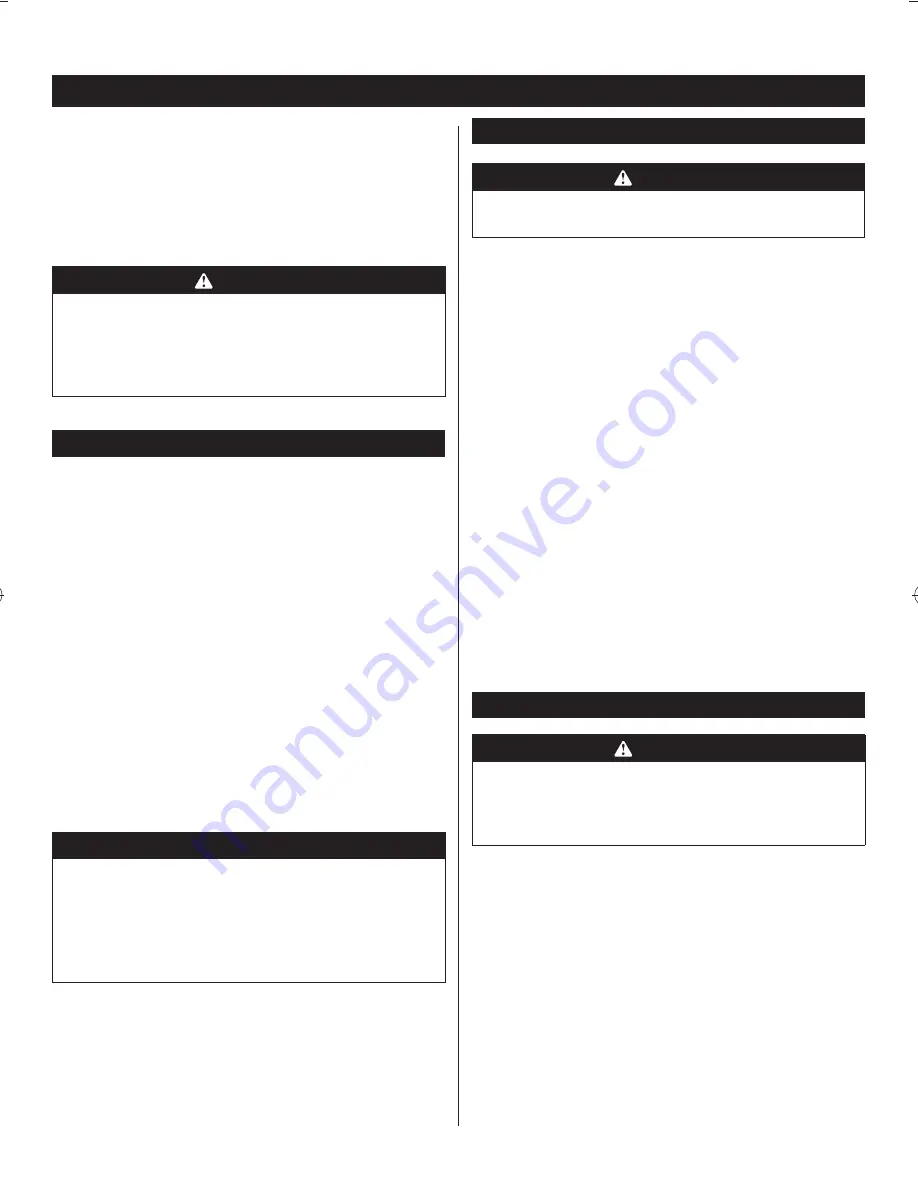
2
English
■
Connect the tool to the air hose.
■
Press trigger to operate the tool.
■
DO NOT use any additional force upon the
tool.
■
DO NOT allow tool to free run for an extended period
of time as this will shorten its life.
WARNING
Ensure the air supply is clean and does not exceed
90psi while operating the tool. Too high an air pressure
and unclean air will shorten the product life due to
excessive wear, and may be dangerous causing
damage and/or personal injury.
LUBRICATION
An automatic in-line
fi
lter-regulator-lubricator
is
recommended (Fig. 7) as it increases tool life and keeps
the tool in sustained operation. The in-line lubricator
should be regularly checked and
fi
lled with air tool oil.
Proper adjustment of the in-line lubricator is performed by
placing a sheet of paper next to the exhaust ports and
holding the throttle open approximately 30 seconds. The
lubricator is properly set when a light stain of oil collects
on the paper. Excessive amounts of oil should be avoided.
It becomes necessary to store the tool for an extended
period of time (overnight, weekend, etc.), it should receive
a generous amount of lubrication at that time. The tool
should be run for approximately 30 seconds to ensure oil
has been evenly distributed throughout the tool. The tool
should be stored in a clean and dry environment.
It is most important that the tool be properly lubricated by
keeping the air line lubricator filled and correctly adjusted.
Without proper lubrication the tool will not work properly
and parts will wear prematurely.
IMPORTANT!
See Figure 7.
If a
fi
lter/regulator/lubricator is not installed on the air
system, air operated tools should be lubricated at least
once a day or after 2 hours work with 2 to 6 drops of oil,
depending on the work environment, directly through
the male
fi
tting in the tool housing.
LOADING AND OPERATION
WARNING
Drain the air tank daily. Water in the air line will damage
the tool.
■
Clean air inlet filter weekly.
■
Line pressure should be increased to compensate for
unusually long air hoses (over 8 meters). The hose
diameter should be 9.52 mm (3/8”) I.D.
■
The high reaction torque can be developed in the case
of stalling. Stalling can be caused by excessive loads
being applied to the drill bit, the drill bit snags on the
material being drilled into or when the drill bit breaks
through the material being drilled.
■
In order to minimize the hazard due to reaction
torque, operate the tool with two hand and grip
tightly
■
The unexpected tool movement or breakage of
inserted tool may cause injuries.
■
There is a risk related to the rotated to the rotating
chuck or drill bit.
■
Keep hose away from heat, oil and sharp edges. Check
hose for wear, and make certain that all connections
are secure.
■
Air tools should not be used in a potentially explosive
environment.
MAINTENANCE
WARNING
Disconnect tool from air supply before changing
accessories, servicing or performing maintenance.
Replace or repair damaged parts. Use genuine parts
only. Non-authorized parts may be dangerous.
■
Keep the tool safe by regular maintenance.
■
Lubricate the tool daily with a few drops of air tool oil
dripped into the air inlet.
■
Clean the tool after use. Do not use worn out or
damaged sockets.
■
Loss of power or erratic action may be due to the
following:
–
Excessive drain on the air line. Moisture or
restriction in the air pipe. Incorrect size or type of
hose connectors. To remedy check the air supply
–
Grit or gum deposits in the tool may also reduce
performance. If your model has an air strainer
(located in the area of the air inlet), remove the