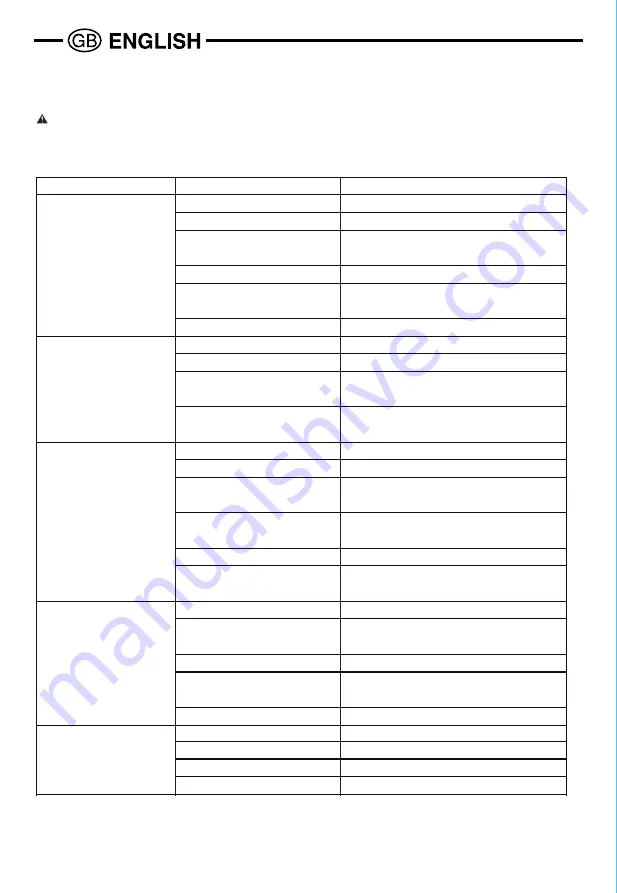
- 9 -
This section describes problems and malfunctions that you should be able to resolve yourself.
DANGER:
Many accidents happen particularly in connection with problems and faults. Therefore
please note:
1. Always unplug before servicing.
2. Check that all safety devices are operational again after each servicing.
SYMPTOM
POSSIBLE CAUSE(S)
CORRECTIVE ACTION
Excessive blade
breakage
Premature blade dulling
Crooked cuts
Rough cuts
Blade is twisting or
unusual wear on side/
back of blade
Material not secure on table Squarely place work on table
Blade too coarse for material Use finer pitch blade
Teeth in contact with work
before sawing
Place blade in contact with work after
saw is started and has reached full speed
Misaligned guides
Adjust blade guides properly
Blade too thick for wheel
diameter
Use thinner blade
Cracking at weld
Replace blade
Blade too coarse
Use finer tooth blade
Inadequate feed pressure
Gently increase pressure
Hard spots or scale in or on
material
Reduce speed; increase rate of feed for
scale and change blades for hard spots
Blade installed backwards
Remove blade, twist inside out and
reinstall blade
Work not square
Use miter gauge; adjust tilt of table at 90
0
Rate of feed too great
Reduce rate of feed
Blade guides not adjusted
properly
Move both guide blocks within 0.002”
from blade (use gauge)
Upper blade guide too far
from workpiece
Adjust upper guide to just clear
workpiece by
1
/
4
”
Dull blade
Replace blade
Blade guide assembly loose
or blade thrust bearing loose
Tighten blade thrust bearing within
0.002” behind blade back
Too much feed
Reduce feed
Blade too coarse
Replace with finer blade
Cut is binding blade
Decrease feed pressure
Blade guides or bearing worn Replace
Blade guides or bearing not
adjusted properly
Adjust blade guides; see “operation”
Blade guide brackets loose Tighten properly
TROUBLE SHOOTING
SYMPTOM
POSSIBLE CAUSE(S)
CORRECTIVE ACTION
Teeth ripping from blade
Motor running too hot
Saw will not start
Teeth too coarse for work
Use blade with finer teeth
Rate of feed too great
Decrease feed rate
Vibrating workpiece
Teeth filling with material
Hold workpiece firmly
Use blade with coarser teeth
Blade too coarse for work
(typical when cutting pipe)
Use blade with finer teeth
Blade too fine for work
(typical when cutting slick or
soft material)
Use blade with coarser teeth
Excessive dirt and chips
Clean thoroughly
Loose electrical connections Have qualified electrician check
electrical connections
Summary of Contents for BS-230
Page 1: ...BS 230 ...
Page 3: ... 2 Rubber Feet Additional Support Bolt 1 2 Wing Nut 3 4 6 Fence Clamp 5 6 ...
Page 5: ... 4 Miter gauge 13 ...
Page 12: ... 11 ...