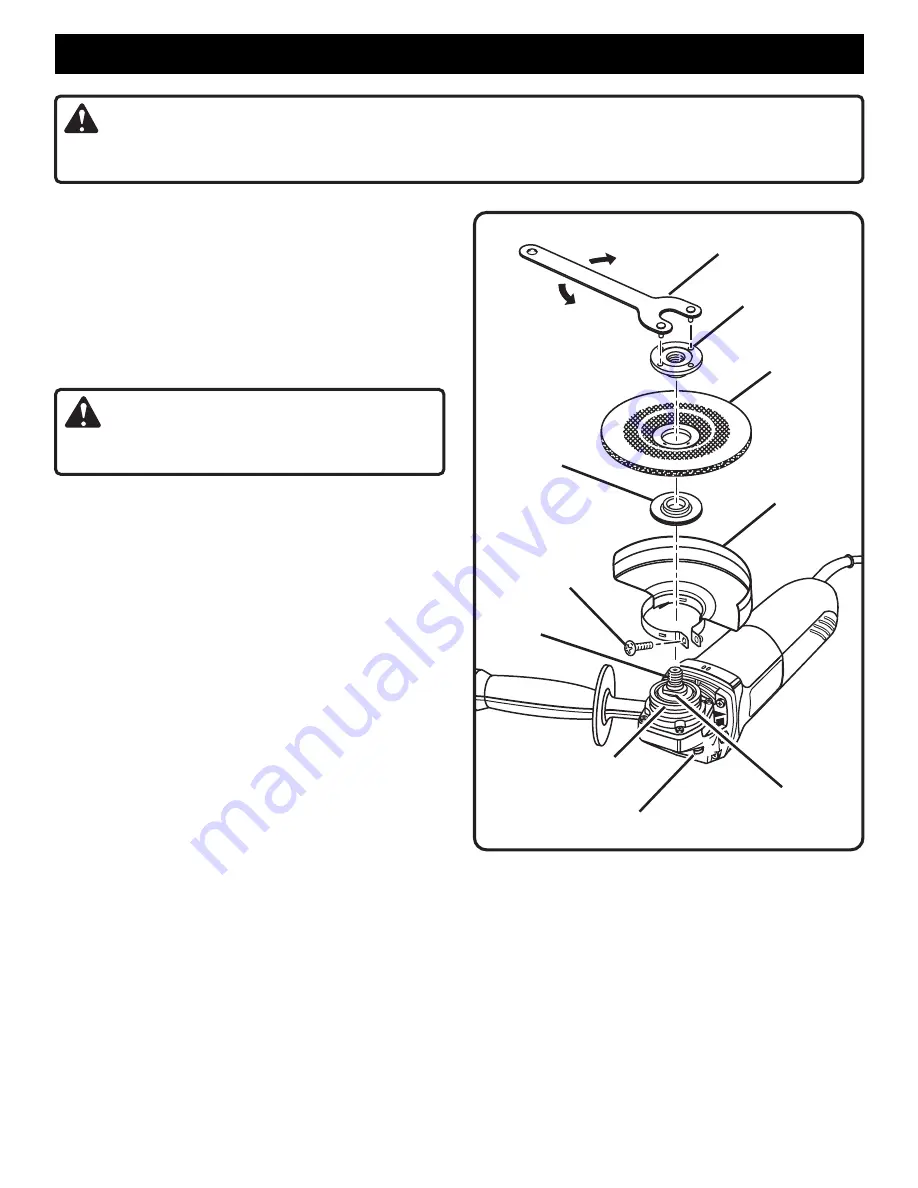
Page 12
WRENCH
CLAMP
NUT
GRINDING
WHEEL
GUARD
DISC
FLANGE
CLAMP
SCREW
TO
LOOSEN
TO
TIGHTEN
FLAT(S)
SPINDLE
LOCK BUTTON
SPINDLE
BEARING CAP
Fig. 9
WARNING:
When servicing use only identical Ryobi replacement parts. Use of any other parts may create a hazard or cause product
damage.
MAINTENANCE
GUARD REPLACEMENT
See Figure 9.
After extended use, the guard may become worn and need
adjustments or replacing. If you drop your grinder and
damage the guard it may also be necessary for you to
replace it.
PROCEED AS FOLLOWS WHEN REPLACEMENT IS
REQUIRED:
UNPLUG YOUR GRINDER.
WARNING:
Failure to unplug your grinder could result in accidental
starting causing serious injury.
Remove and reassemble parts as shown in figure 9.
Depress spindle lock button and rotate clamp nut until
spindle locks.
Using the wrench provided, loosen and remove clamp
nut from spindle.
Remove grinding wheel and disc flange.
Using a screwdriver, loosen the clamp screw until the
guard can be adjusted or removed.
If you are making adjustments, rotate the guard to its
correct position as shown in figures 4, 5, and 9, then
retighten clamp screw securely
.
Never use your grinder
without the guard in place and properly adjusted.
See Figures 4, 5, and 6.
Note:
Be sure the tabs on the guard are seated in the
groove in the bearing cap.
If you are replacing the guard, loosen the clamp screw
until the guard can be removed from the bearing cap.
Place the new guard on the shoulder of the bearing cap.
See Figure 9.
Note:
If the new guard will not fit, loosen the clamp
screw until the guard slides over the bearing cap.
Rotate guard to the correct position as shown in figures 4,
5, and 6.
Tighten clamp screw securely.
Note:
Be sure the tabs on the guard are seated in the
groove in the bearing cap.
Reassemble disc flange, grinding wheel, and clamp nut.
Refer to
"INSTALLING THE GRINDING WHEEL"
in-
structions on page 9.
Depress the spindle lock button and rotate the wheel
clockwise until the spindle locks in position.
Securely tighten the clamp nut with the wrench provided.