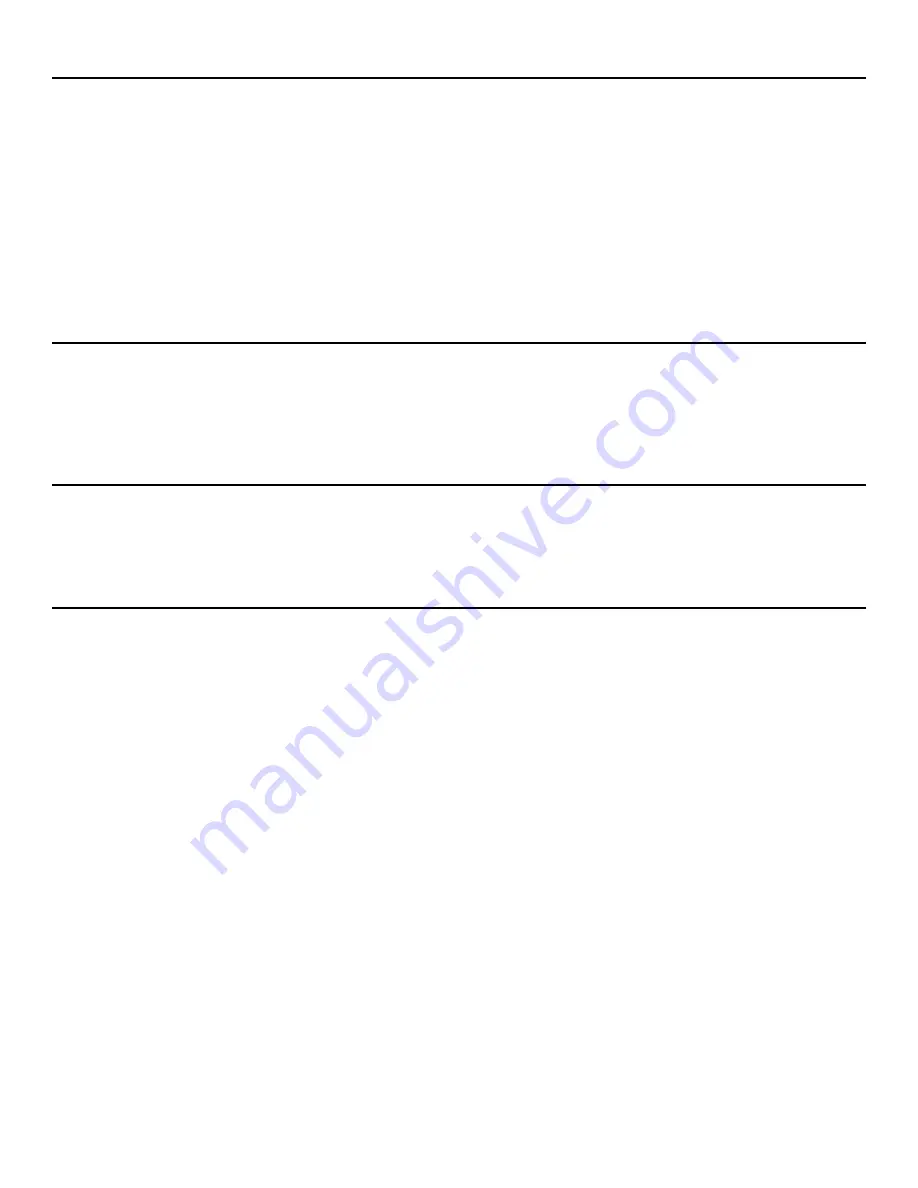
•
Operations Guide
Part 2
–
Agitating and Monitoring Temperature
1.
Never leave melter unattended when the burner is lit. If flame goes out, promptly turn off the flow of gas; double
check that the melter is free and clear of any gas odors before attempting to re-ignite the burner.
2.
While your melter is ignited you should continuously be monitoring the material temperature. Check with your crack
sealant manufacturer for safe melting temperatures and ensure you continually adjust the burner control knob to
maintain the recommended temperature range. If the material becomes too hot, you may need to turn off your
burner periodically.
3.
As material begins to melt, it’s important to consistently agitate. Agitation moves the solid crack sealant along the
bottom and prevents ‘hot spots’ from forming which can al
ter the effectiveness of the sealant after applied.
Agitation also prevents chunks of over-heated material from forming which will eventually
plug or block your flow valve which can slow down material flow.
Part 3
–
Dispensing Crack Filler
Once you have effectively liquefied the crack sealant, you may begin to dispense it from the molasses valve into a pour
pot or other application device. Having a hot molasses valve helps facilitate the flow of melted crack fill. We recommend
having an auxiliary heating torch on hand to heat up the molasses valve before dispensing.
Part 4
–
Turning Off and Draining
Once you have finished using the melter, make sure it is fully drained and no crack filler remains inside the kettle or the
flow valve. Leaving the flow valve empty after use will prevent the valve from being blocked the next time you use the
melter.