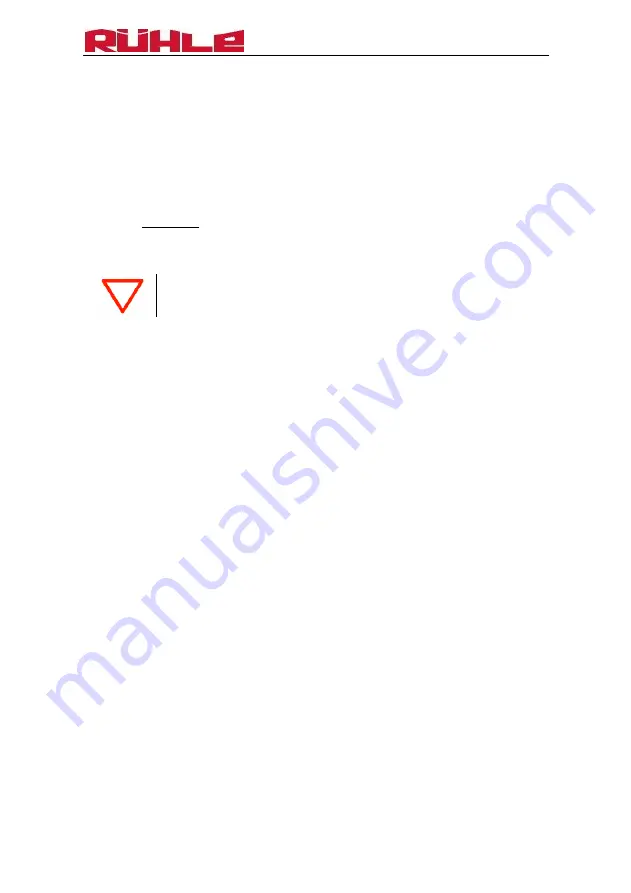
Miknetum MPR 400
7
1.3
Intended Use
The Miknetum has been solely designed for mixing, salting/season-
ing, marinating and tumbling meat products and salads. The max.
room temperature may be 12 °C for reasons of food hygiene!
This machine is designed to be operated by
a person over the age of 18!
only one tablet PC with the application software (Rühle MPR
App)!
Claims of any type because of damages due to non-in-
tended use are ruled out!
Misuse:
Any use other than the one listed above is strictly prohibited
and is considered misuse!
Operating the machine in explosion hazard areas is prohibited!
Handling / processing products and materials not belonging
to food products is prohibited!
The lifting aid may be used only for the standard trolleys pro-
vided and must not be overloaded! Lifting of persons is
strictly prohibited!
Connecting several tablet PCs with a machine is prohibited!
2
Installation instructions
Installation and commissioning of the machine may only be carried
out in the presence of a Rühle service technician or by persons au-
thorised by Rühle.
Rühle GmbH Lebensmitteltechnik shall not be liable for any damage
resulting from non-compliance with these operating instructions.