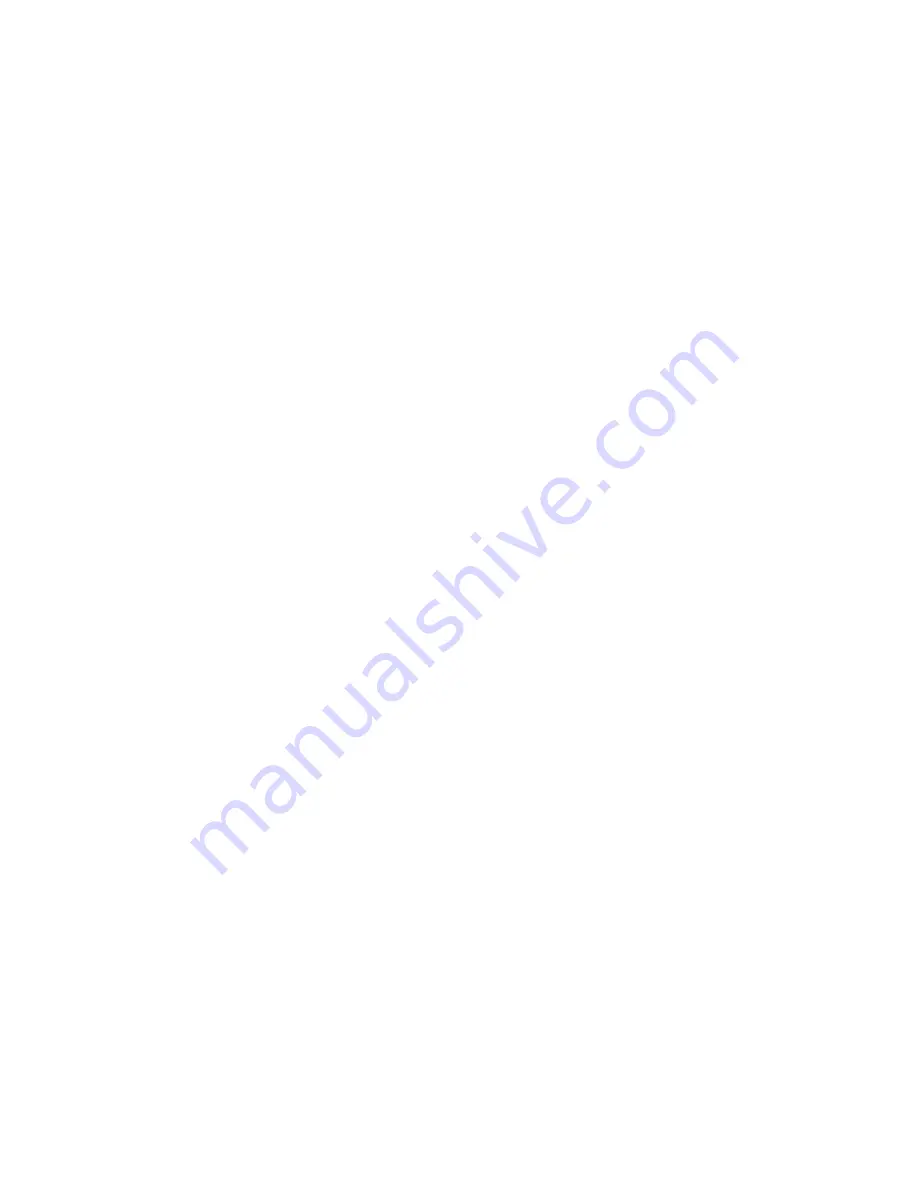
41
due to high ambient atmosphere temperature (850-900°), and the penetrating power of high
intensity short wave radiation, the organic volatiles within the inks essentially sublimate
completely from the structure without eruption. Structure depths up to 300 um thickness are
possible without the unacceptable diffusions and migrations of materials encountered in
conventional processing.
Similarly, in most cases, single print firing may be done wet, and the print/fire process will
be shorter, even than the former print/dry process.
5.4.1.
Profile
For most thick film processes in the RTC furnaces, the rate of temperature rise in
the product can be made as fast as needed, the volatilization and sublimation of
organic binders being completed long before polymerization or fusion temperatures
are attained. To this end, zone 1 should be driven as hard as practical to maintain
the highest intensity short wave radiation (near infrared), reaching process
temperature at the beginning of subsequent holding zone(s). These are set at
process fusion or polymerization temperatures. Dwell time in these zones should
be just sufficient to drive the pyrolysis, fusion, or polymerization to completion.
By limiting the time at temperature in this manner, unacceptable migrations or
diffusions are avoided.
It has been found that substrate cracking is somewhat (if not entirely) dependent on
cooling rates. The cooling module should be adjusted to provide cooling rates
consistent with high yield and throughput.
5.5.
Solder Fusion, Die Attach, and Sealing Processing
In general, these process operations involve components which are sensitive to time at
temperature and exposure to atmosphere impurities. The ability to rapidly and linearly bring
a unit to a temperature substantially below process temperature, and subsequently provide a
"spike" of high intensity radiation to drive the process to completion, in an atmosphere under
complete control, serves to limit the time/temperature/exposure product to a minimum, and
increase yield and throughput substantially, compared to conventional processing.
5.5.1.
Profiling for Solder Fusion, Die Attach, and Sealing
The profiles for these operations are derived by trial and error, because of the great
number of variables involved affecting thermal response of the furnace and the
system being processed.
Boats, fixtures, and other processing aids should have a thermal mass as small as
practical, consistent with good manufacturing practice and requirements.
Conveyor speed should be adjusted as high as practical. Zone 1 (and 2)
temperature should be set to a temperature which will bring the system being
processed to an internal temperature substantially below the fusion temperature.
The spike zone (zone 2 or 3, depending on model) should be set such that the
internal temperature achieved by the system will insure that fusion is complete,
without exceeding limits imposed by the separate components of the system.
Summary of Contents for 2115150301
Page 23: ...22 Figure 3 8 1 1 Event Logging ...
Page 44: ...43 Section 6 PRODUCT SPECIFICATION 6 PRODUCT SPECIFICATION ...
Page 62: ...61 View Product Tracking ...
Page 83: ...82 ...