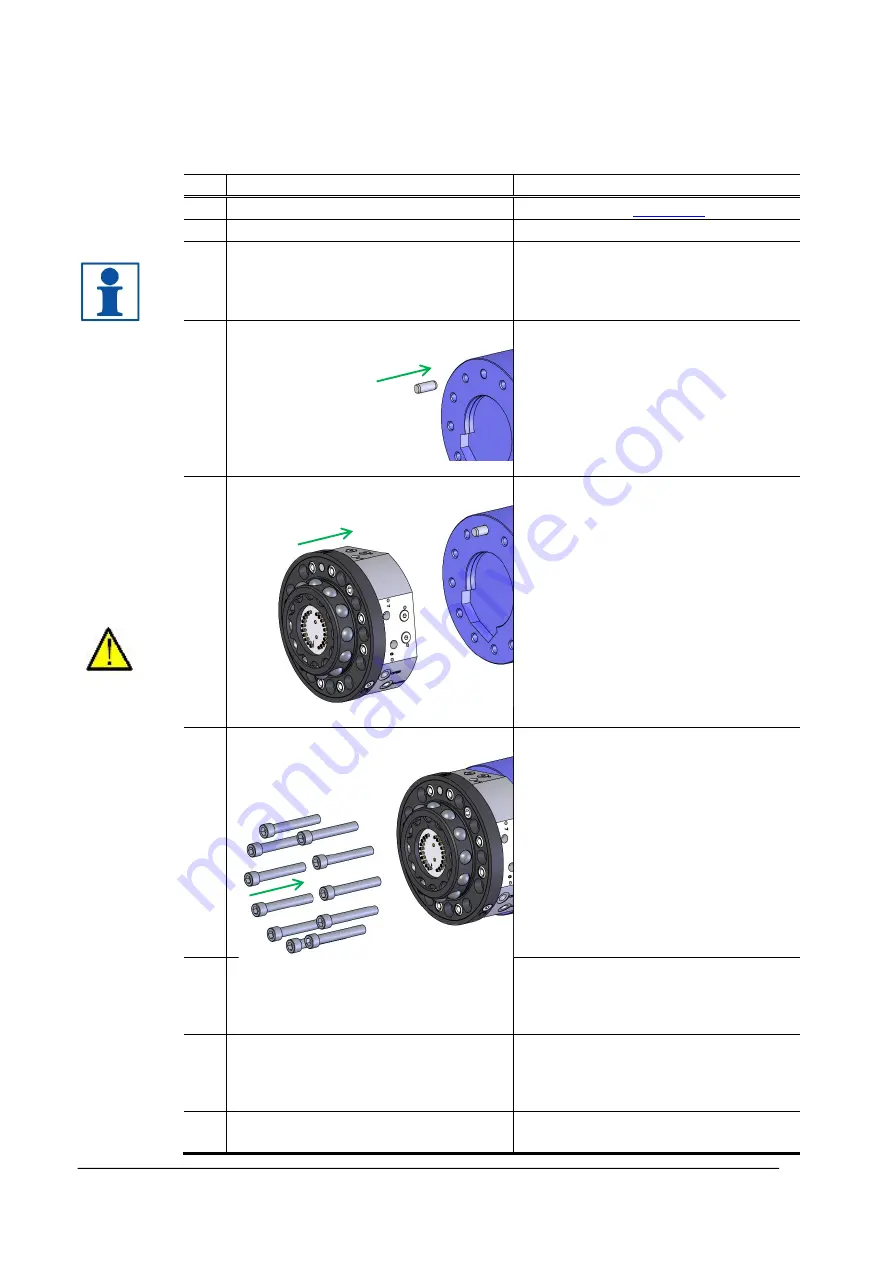
8
M0416-1 version 3.2
2 INSTALLATION
2.1 Installation of tool changer on robot
Action
Note
1
Safety
Read the safety
section 1.2
.
2
Service position
Place the robot in service position.
3
Power off
Switch the power off and lock the
circuit breaker.
NOTE!
Read the safety chapter for the
robot.
4
Mount guide pin
Press the enclosed guide pin into the
robot flange.
Alternatively, if adaptation plate is
used
:
Mount the adaptation plate on the robot
flange (see tightening torques above).
Press the enclosed guide pin into the
adaptation plate.
5
Fit tool changer
Lift the tool changer to the robot flange
(or adaptation plate). The arrow on the
front of the tool changer indicates the
position of the hole for the guide pin.
Make sure that the guide pin is fitted to
the guide hole in the tool changer.
WARNING!
The tool changer may
cause personal injury and equipment
damage if dropped.
6
Mount tool changer
Mount the tool changer with the
enclosed screws. Use an Allen key for
tightening (see tightening torques
above).
7
Connect air hoses
Connect the air hoses according to
markings. Pneumatic diagrams are
found in the Product Description of
respective unit.
8
Connect electrical signals
(electrical
versions only)
Connect electrical connectors in
accordance with selected unit. Circuit
diagrams are found in the Product
Description of respective unit.
9
Power on
Unlock the circuit breaker and switch
the power on.
Summary of Contents for Compact Series
Page 2: ...2 M0416 1 version 3 2 ...
Page 21: ...M0416 1 version 3 2 21 ...
Page 22: ...22 M0416 1 version 3 2 ...