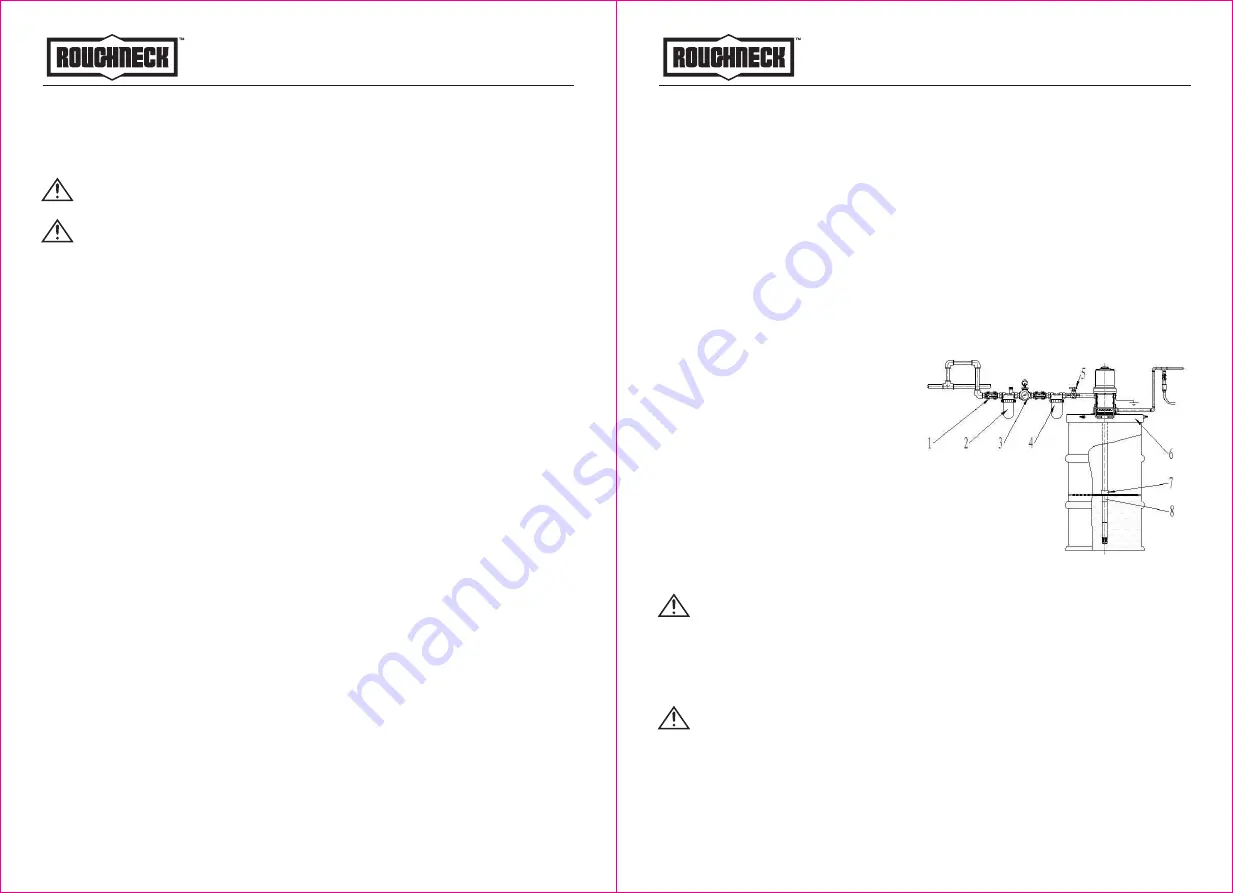
4. FIRE AND EXPLOSION HAZARD:
Improper grounding, poor ventilation, open flames or sparks
can cause a hazardous condition and result in a fire or explosion and serious injury.
• Ground the equipment and the object being dispensed to
• If there is any static sparking or you feel an electric shock while using this equipment, stop
dispensing immediately. Do not use the equipment until the grounding or any other problem
is identified and solved.
• Provide fresh air ventilation to avoid the buildup of flammable fumes from solvents or the
fluid being dispensed.
• Keep the dispensing area free of debris, including solvent, rags, and gasoline.
• Do not smoke in the dispensing area.
5. TOXIC FLUID HAZARD:
Hazardous fluid or toxic fumes can cause serious injury or death if
splashed in the eyes or on the skin, inhaled, or swallowed.
• Know the specific hazards of the fluid you are using.
• Store hazardous fluid in an approved container. Dispose of the hazardous fluid according
to all local, state and national guidelines.
• Always wear protective eyewear, gloves, clothing and respirator as recommended by the
fluid and solvent manufacturer.
INSTALLATION
Typical installation refers to Fig.1.
1. Check valve
2. Filter
3. Pressure regulator
4. Lubricator
5. Control valve
6. Drum cover
7. Plate
8. Grease pump
NOTE:
The above typical installation is only for reference. It may
be different from your actual system design.
Fig 1 Typical installation
1. PRE-INSTALLATION PROCESS
WARNING:
To reduce the risk of serious injury, the pressure release should be concerned.
Please follow the
Pressure Relief Procedure
in
OPERATION INSTRUCTIONS
section for the
release process.
(1) Turn off the air check valve 1 as shown in Fig. 1.
(2) Effective grounding to grease supply system. Do not use an insulation material to the ground.
The grounding is a very important part to maintain the security system. Follow the instructions
below for effective grounding.
WARNING:
To reduce the risk of static sparking, effectively ground all of this equipment.
•
Control valve:
Use proper grounding wire to connect it to the pump. Always keep the metal
part of the control valve connected with the grounding equipment.
•
Air and fluid hoses:
Make sure they are effectively grounded.
•
Air compressor:
Follow the manufacturer's instruction to ground it.
•
Grease barrel:
Use a barrel that meets the local standard and ground it properly. A metal
barrel can be put directly on a surface of an electrical conductor which is well grounded.
•
Staying grounded during the working and grease release process:
Make sure that the metal
units are effectively grounded before operating the control valve.
DIGITAL GREASE CONTROL VALVE OWNER’S MANUAL
DIGITAL GREASE CONTROL VALVE OWNER’S MANUAL
7. DO NOT use the equipment when tired or under the influence of drugs, alcohol, or medication.
A moment of inattention while operating this equipment may result in serious personal injury.
8. Industrial applications must follow OSHA requirements.
SPECIFIC OPERATION WARNINGS
WARNING:
To prevent personal injury, perform Pressure Relief Procedure before and
after operating the control valve and before performing any disassembly or assembly.
WARNING:
No complying with below requests will result in severely harm to your
body even death.
1. EQUIPMENT MISUSE HAZARD:
Equipment misuse can cause the equipment to rupture or
malfunction and result in serious injury.
• Only trained or authorized people should operate this equipment.
• Read all instruction manuals, tags, and labels before you operate this equipment.
• Use the equipment only for its intended purpose. If you are not sure, call the distributor.
• Do not modify this equipment. If you need to replace the parts, use the standard parts or
components.
• Check equipment daily. Repair or replace worn or damaged parts immediately.
• Do not exceed the maximum working pressure of the lowest rated system component. This
equipment has an 8700 PSI maximum working pressure.
• Check equipment daily. Repair or replace worn or damaged parts immediately.
• Make sure all application comply with local, state, and national fire, electrical, and safety
regulations.
• Do not use a low pressure flexible extension on a high pressure dispensing valve.
• Wear heat-resistant gloves when using the control valve.
• Do not move or lift the equipment when the control valve is in use.
• Do not attempt to force lubricant into a fitting.
• The operation environment must be fireproof, safety electric use and other security a sured.
2. SKIN INJECTION HAZARD:
Fluid from the dispensing valve, leaks, or ruptured components
can splash into your body, eyes or skin, which may cause extremely serious injury. If this
happens, ask for medical help immediately.
• Do not point the dispensing valve at anyone or at any part of the body.
• Do not stop or deflect leaks with your hand, body, glove or rag.
• Do not use grease that has been polluted.
• Use only extensions and no-drip tips that are designed for use with your dispensing valve.
• Follow the
Pressure Relief Procedure
in the
OPERATION INSTRUCTIONS
section if the
grease fitting coupler clogs and before you clean or service this equipment.
• Before each use, make sure that all connections are properly installed.
• Check the hoses, tubes, and couplings daily. Replace worn or damaged parts immediately.
Do not repair high-pressure couplings; you must replace the entire hose.
3. MOVING PARTS HAZARD:
Moving parts, such as the air motor piston, can pinch or amputate
your fingers.
• Keep clear of all moving parts when you start or operate the control valve.
• Before you service this equipment, follow the
Pressure Relief Procedure
in
OPERATION
INSTRUCTIONS
section to prevent the equipment from starting unexpectedly.
• Before operating the control valve, make sure no moving parts of your system is exposed outside.
•
Never operate the control valve with the identification plate removed.
This plate protects
your fingers from pinching or amputation by moving parts.
2 of 9
3 of 9