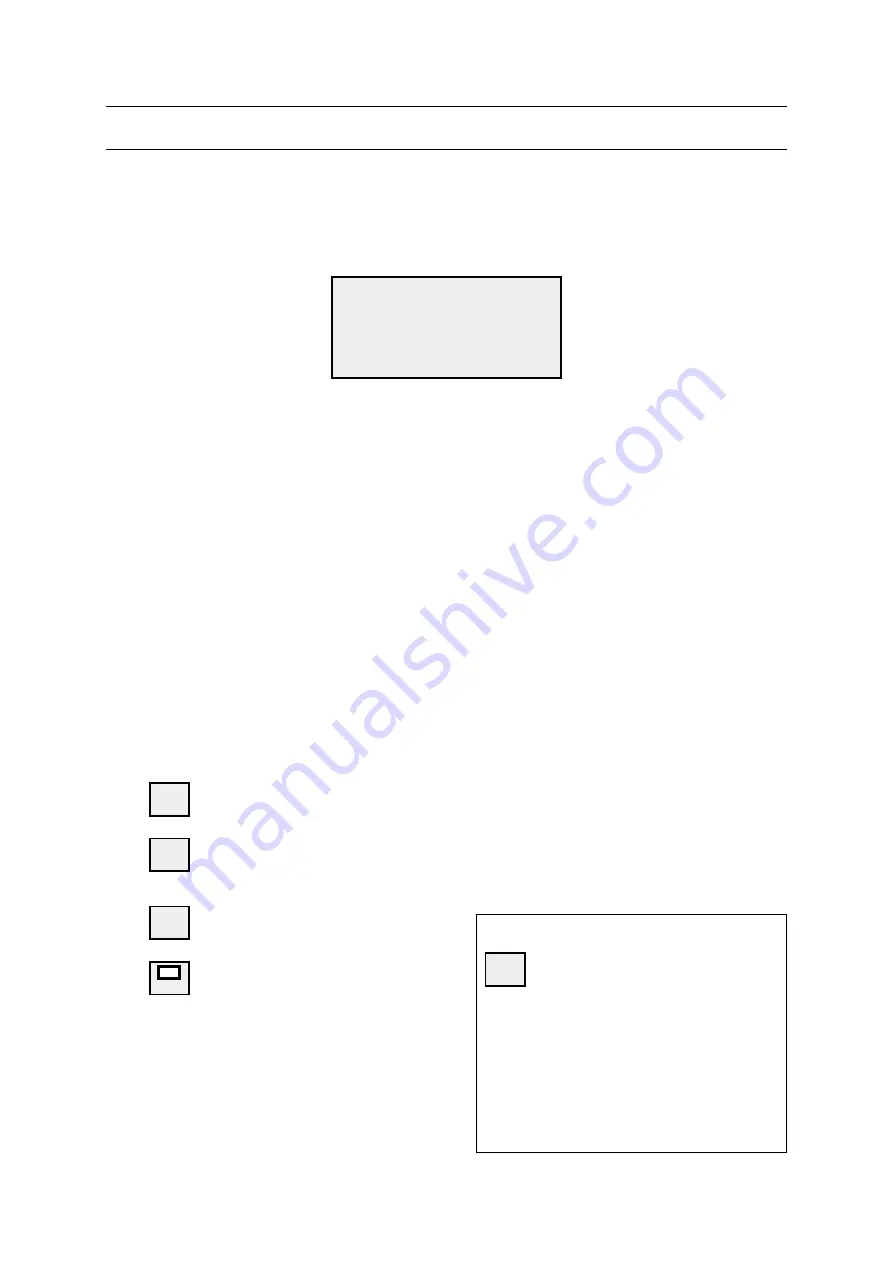
Pakscan IIS Technical Manual Issue 1.0
Publication S130E 43
8.5.8 Keypad Security Options
A security code, PIN, can be set up to prevent unauthorised changes to the master station settings or field unit
outputs. The second line shows ‘PIN Not In Use’ if no PIN has been set up and ‘PIN In Use’ once a PIN has
been set.
The operations which are protected by the PIN are indicated by the ‘Access Level’ number on line 3. The
meaning of these numbers is:
1 - No protection. Setups can be changed and keypad commands entered without the PIN.
2 - Setup protection. Setup changes require the PIN but keypad commands do not.
3 - Setup and Command protection. Both setup changes and keypad commands require the
PIN.
4 - No keypad commands permitted whilst either host serial communication line is active.
[If both serial communication links are inactive for 5 seconds then keypad commands
can be entered provided the PIN is entered (as with level 3) .]
Commands available:
(all changes require either the Access level to be set to 1 or the current PIN to be entered)
- Change the requirement for inputting a PIN. When setting the PIN as ‘Out of use’ the
previously programmed PIN is lost
- Enter a new PIN (when entered it will automatically place PIN ‘In use’). Type in the
required PIN. Numbers between 1000 and 9999 are acceptable. Mistakes can be
corrected using the CLEAR key. Finish entering the PIN by pressing LOAD.
- Change the access level
- Return to previous menu
Keypad Security
1>PIN In use
2>PIN = ****
3>Access Level 3
1
2
3
MENU
Entering a PIN from any screen:
Pressing the * key reveals the PIN entry
screen. Type in the PIN number and
then press the LOAD key. If the PIN is
correct then press the MENU key to
return to the previous page.
When an action requires the PIN to be entered a
screen message ‘PIN required’ is displayed.
*