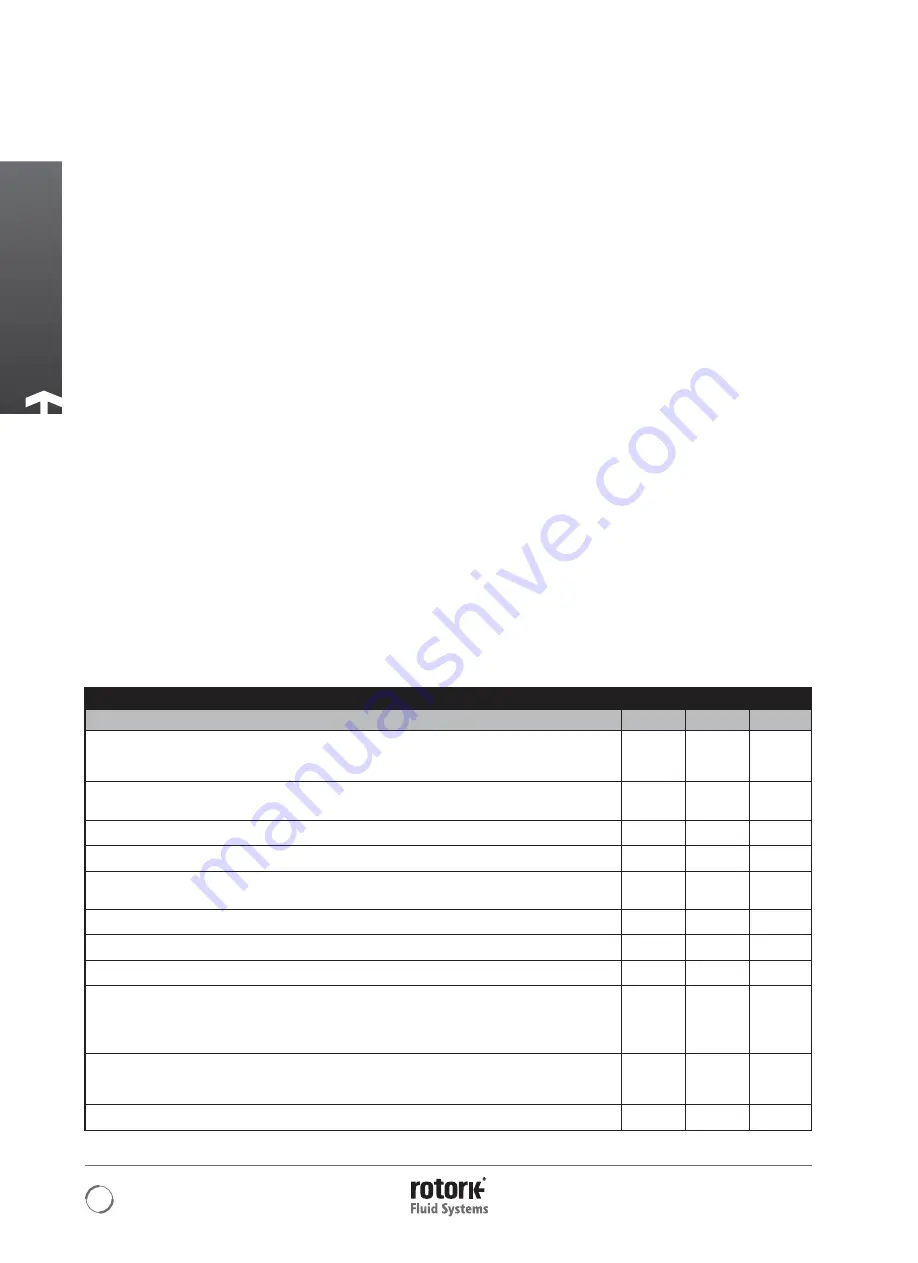
20
10.4 Start-up
During the start-up of the actuator, it is necessary to check that:
• the medium supply pressures, as well as its quality
(filtering degree, dehydration) are as prescribed.
• the feeding voltage values of electrical components
(solenoid valves, micro switches, pressure switches etc.,
if applicable) are as prescribed.
• the actuator controls such as remote control, local
control, emergency control etc. (if applicable) work
properly.
• the required remote signals (such as valve position, etc.)
are correct.
• the components setting of the actuator control unit is
according to the plant requirements.
• there are no leakages in the pneumatic connections.
If necessary, tighten the fittings.
• the painted parts have not been damaged during
transport, assembling or storage operations. If damage
has occurred, remove rust and repair the damaged parts
following the applicable painting specifications, please
contact Rotork.
• actuator and all of its control accessories work as
expected.
• the operating time is in accordance with requirements.
Table 2: Periodic Maintenance Schedule
10.5 Speed adjustment
Slower operation of the actuator is possible by restricting
the air exhausting from the actuator. The most common
device used for adjusting cycle speeds is a “flow control
valve” that free flows air into the actuator in one direction
and meters the air in the opposite direction. Flow control
mufflers will accomplish the same results when utilised with
a 5-ported direct acting solenoid valve that has independent
exhaust ports.
11 MAINTENANCE
11.1 Periodic inspections
K-TORK range actuators are designed to work for long
periods of time under severe conditions. A preventive
approach to maintenance helps to avoid costly down time
and can reduce the cost of ownership.
Rotork can provide actuator maintenance contracts tailored
to meet each individual customer’s requirement.
Perform checks specified in the following periodic
maintenance schedule, in accordance with the plant
maintenance procedures, and in compliance with the local
rules and regulations.
Start-up
Maintenance
Periodic Maintenance Schedule
Maintenance work
Month
Year
Work
Visually check the external components of the actuator as well as the control accessories (if applicable) for physical
damage and repair or replace as required. Verify the integrity of welding if applicable. In case an anomaly is detected,
please contact Rotork.
6
-
-
Ensure no leaks are present on the actuator parts under pressure. Check pneumatic connections for leaks.
Tighten plugs and pipe fittings as required.
-
1
-
Ensure no leaks are present on the control panel (if present).
-
1
-
Remove built-up dust and dirt from all actuator surfaces.
-
1
-
Inspect actuator paint work for damage to ensure continued corrosion protection. Touch-up as required in
accordance with the applicable paint specifications, please contact Rotork.
-
1
-
Verify operation. The actuator should be cycled several times with the local and remote (if present) control.
1
N/A
N/A
Ensure that the actuator operates the valve correctly within the required cycle time.
-
1
-
Check up and clean the air filter element (if present).
6
-
-
Check the state of electric components (if present)
Remove the covers from the electric components, check the state of electric device, the tightness of terminal
blocks, the presence of oxidation and humidity.
Check the cable gland seals.
-
1
-
Check the threaded connections (bolts, studs and nuts) connecting the actuator to the valve. If necessary
tighten the bolts or the nuts of the connecting studs to the correct torque, in accordance with the size and the
characteristics of the fastener material installed by the customer.
-
1
-
Replace actuator seals.
-
5
See section
11.1.2