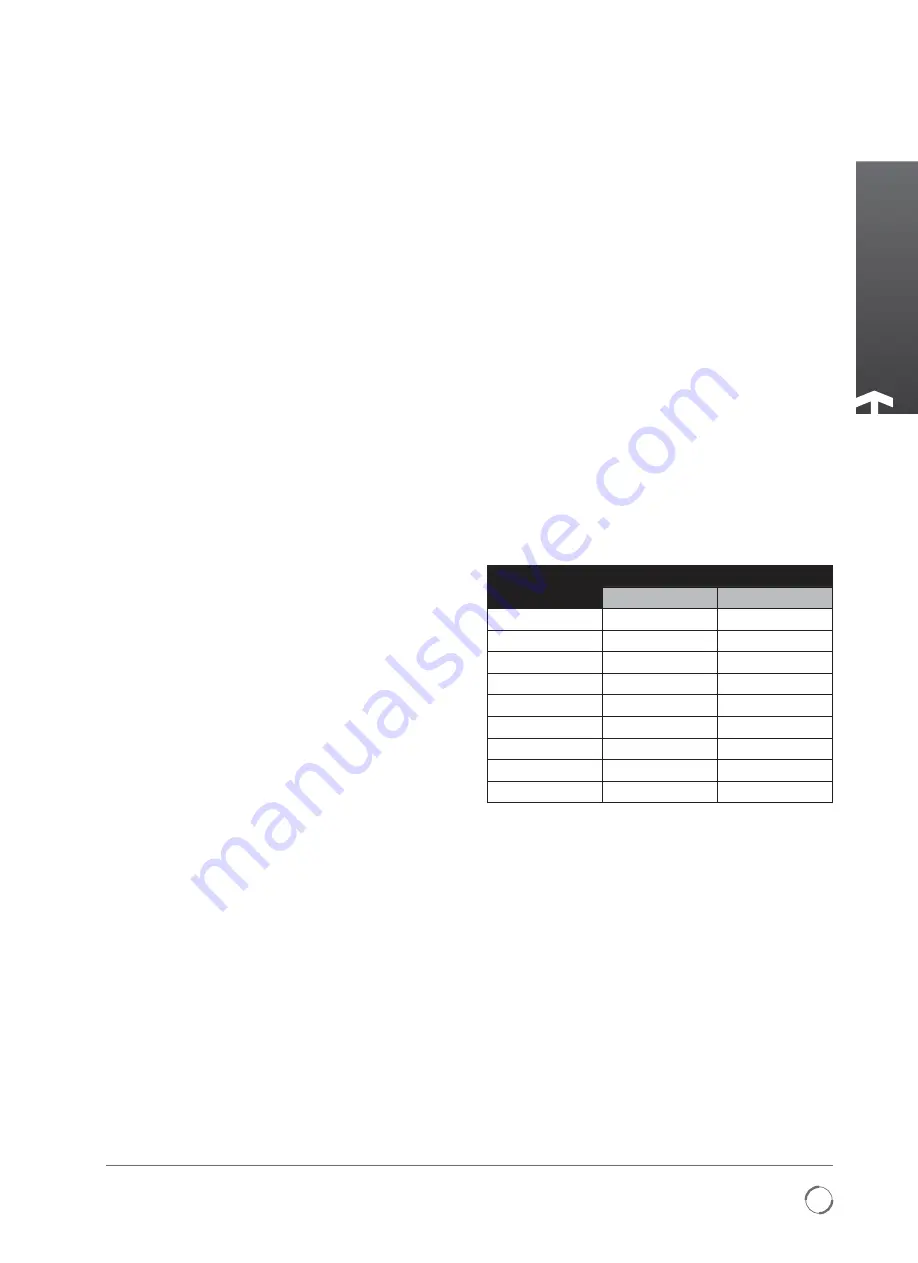
25
Keeping the World Flowing
Maintenance
11.1.2.7 Installing the spring module to the actuator
The spring module with the keeper plate should be
provided in the mid-stroke position. Before proceeding,
check that the keeper plate is properly installed and the
actuator is in mid-stroke position.
Place the actuator in a stable position, e.g. on a workbench.
See Figure 8 and proceed as follows:
a) Once the spring cover has been removed from the spring
module, apply a thin film of recommended silicone
sealant to the mounting face on the output side of the
actuator. Attach the spring cover to the actuator using
the four flat head screws provided.
b) Position the O-ring in the groove on the spring housing or
spring cover (this groove’s location will depend on spring
assembly size).
c) Align the actuator shaft to the spring shaft, ensuring
the vane is in the mid-position (45° of rotation). The
mount bolt holes of the spring housing should match the
orientation of the actuator mount bolt holes.
d) Install the spring module.
e) Carefully rotate the actuator vane to align the flange
bolt holes on the spring housing with the corresponding
flange bolt holes in the spring cover. Install the socket
head cap screws, including washers and nuts, and
tighten. ALL FLANGE BOLTS MUST BE INSTALLED AND
PROPERLY TIGHTENED BEFORE REMOVING THE KEEPER
PLATE.
Removing the Keeper Plate
f) Connect air supply using a regulator to actuator inlet port
(port opposing spring action).
g) Increase air pressure slowly until actuator shaft is
balanced in the keeper plate. Typically 38 to 42 psi to
balance actuator shaft for springs wound for 80 psi
service.
h) Loosen the keeper plate bolts. With proper air pressure,
the bolts will not bind. If binding adjust air until bolts are
loose enough to be removed.
i) Remove the spring retainer keeper plate.
j) Slowly reduce air supply with regulator to 0 psi.
After the final reassembly on the valve, execute the stop bolt
setting as in Paragraph 9.2.
11.1.2.8 Final reassembly and testing
a) Assemble the components on the actuator (e.g. limit
switch box, position transmitter), if any.
b) Assemble the control panel, if any.
c) The actuator must be tested prior to being mounted on a
valve.
-
Place the actuator in a stable position, e.g. on a
workbench.
-
Connect the pneumatic supply to the actuator and
cycle the actuator several times in order to verify that
it operates smoothly. Ensure there are no leaks from
pneumatic connections or housing seals.
-
If painted parts have been damaged during disassembly
and/or reassembly, repaint in accordance with the
applicable paint specification, available upon request
from Rotork.
The actuator may now be mounted to a valve.
Recommended Spare Parts
Table 5: Double-acting spare parts list (seal kit part numbers)
Model No.
Spare Part No.
Standard Temp.
High Temp.
KT-03*
2511800
2511801
KT-06*
2511000
2511001
KT-10
2011010
2011011
KT-20
2011020
2011021
KT-30
2011030
2011031
KT-40
2011040
2011041
KT-50
2011050
2011051
KT-60
2011060
2011061
KT-70
2011070
2011071
• Seal kit contains:
-
2 vanes seals (item 2)
-
2 expanders (item 3)
-
2 shaft seals (item 11)
-
2 stop bolts seals (item 14)
-
Packet of grease
-
Nylon insert lock nuts (item 6)
In addition a tube of sealant, either GT-3100 One Part RTV
Silicone or Dow Corning Silicone # 732 will be required to
seal the case halves.
* KT-03 and KT-06 not available, number is for FULL actuator
replacements