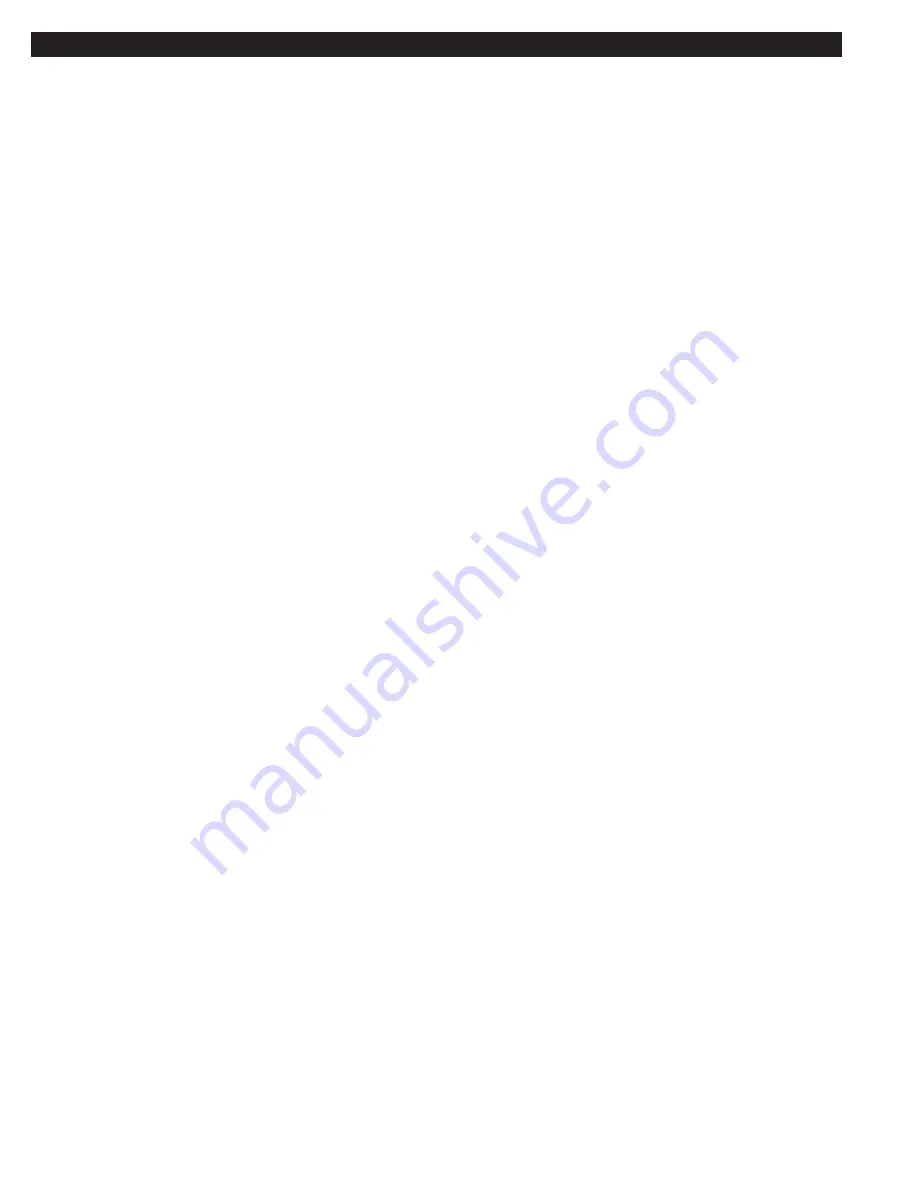
8
Purpose
This procedure establishes the minimum requirements for the lockout of energy that could cause injury to
personnel by the operation of lifts in need of repair or being serviced. All employees shall comply with this
procedure.
Responsibility
The responsibility for assuring that this procedure is followed is binding upon all employees and service
personnel from outside service companies (i.e., Authorized Rotary Installers, contactors, etc.). All employees
shall be instructed in the safety significance of the lockout procedure by the facility owner/manager. Each
new or transferred employee along with visiting outside service personnel shall be instructed by the owner/
manager (or assigned designee) in the purpose and use of the lockout procedure.
Preparation
Employees authorized to perform lockout shall ensure that the appropriate energy isolating device (i.e.,
circuit breaker, fuse, disconnect, etc.) is identified for the lift being locked out. Other such devices for other
equipment may be located in close proximity of the appropriate energy isolating device. If the identity of the
device is in question, see the shop supervisor for resolution. Assure that proper authorization is received
prior to performing the lockout procedure.
Sequence of Lockout Procedure
1) Notify all affected employees that a lockout is being performed and the reason for it.
2) Unload the subject lift. Shut it down and assure the disconnect switch is “OFF” if one is provided on
the lift.
3) The authorized lockout person operates the main energy isolation device removing power to the
subject lift.
• If this is a lockable device, the authorized lockout person places the assigned padlock on
the device to prevent its unintentional reactivation. An appropriate tag is applied stating the
person’s name, at least 3” x 6” in size, an easily noticeably color, and states not to operate
device or remove tag.
• If this device is a non-lockable circuit breaker or fuse, replace with a “dummy” device and
tag it appropriately as mentioned above.
4) Attempt to operate lift to assure the lockout is working. Be sure to return any switches to the “OFF”
position.
5) The equipment is now locked out and ready for the required maintenance or service.
Restoring Equipment to Service
1) Assure the work on the lift is complete and the area is clear of tools, vehicles, and personnel.
2) At this point, the authorized person can remove the lock (or dummy circuit breaker or fuse) & tag
and activate the energy isolating device so that the lift may again be placed into operation.
Rules for Using Lockout Procedure
Use the Lockout Procedure whenever the lift is being repaired or serviced, waiting for repair when current
operation could cause possible injury to personnel, or for any other situation when unintentional operation
could injure personnel. No attempt shall be made to operate the lift when the energy isolating device is
locked out.
LIFT LOCKOUT/TAGOUT PROCEDURE
Summary of Contents for SPOA7 Series
Page 10: ...10 NOTES...
Page 11: ...11 NOTES...