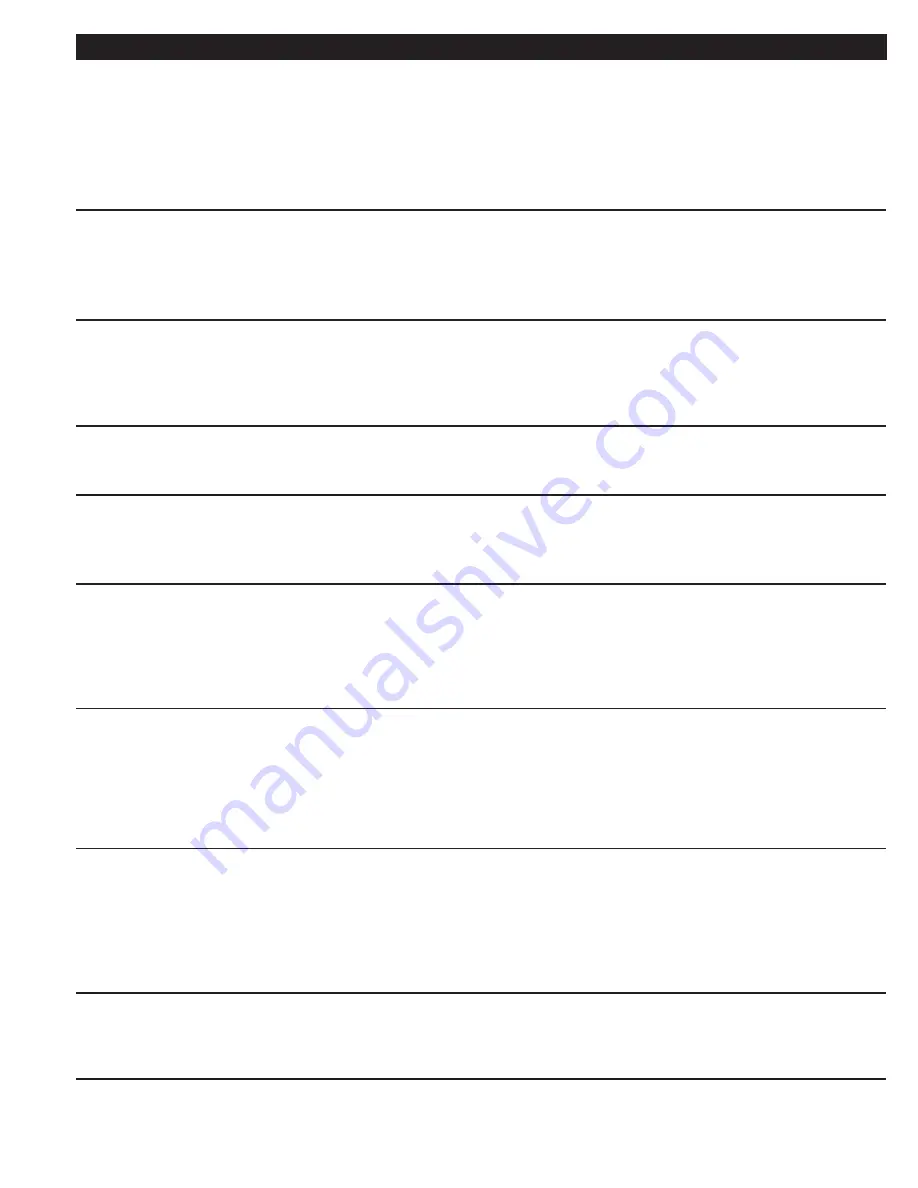
7
Trouble
Motor does not run.
Motor runs but will not raise lift.
Motor runs—raises unloaded lift but will
not raise vehicle.
Lift slowly settles down.
Slow lifting speed or oil blowing out filler
breather cap.
Lift going up unlevel.
Anchors will not stay tight.
Locking latches do not engage.
Locking latches do not disengage.
Lift stops short of full rise or chatters.
Remedy
1. Replace blown fuse or reset circuit
breaker.
2. Supply correct voltage to motor.
3. Repair and insulate all connections.
4. Replace switch.
5. Replace switch.
6. Replace motor.
1. Repair or replace lowering valve.
2. Tighten all suction line fittings.
3. Replace suction stub.
4. Fill tank to proper level with ISOVG32
Hydraulic Oil or Dexron III ATF.
1. Supply correct voltage to motor.
2. Clean lowering valve.
3. Replace relief valve cartridge.
4. Check vehicle weight and/or balance
vehicle weight on lift.
1. Clean check valve.
2. Clean lowering valve.
3. Repair external leaks.
1. Change oil using ISOVG32 Hydraulic Oil
or Dexron III ATF.
2. Tighten all suction line fittings.
3. Reinstall oil return tube.
1. Adjust equalizer cables to correct
tension.
2. Shim lift to level columns (Not to
exceed 1/2”). If over 1/2” break out
floor and repour per lift installation
instructions.
1. Relocate lift using a new bit to
drill holes. Reference installation
instructions for minimum spacing
requirements.
2. Break out old concrete and repour
new pads for lift per lift installation
instructions.
1. Remove covers, oil latch mechanism.
Actuate latch release handle several
times to allow oil to coat shaft.
2. Replace broken spring.
3. Adjust clamp at cable end per lift
installation instructions.
1. Replace cable.
2. Check position of cable on sheaves/
upper guides; adjust cable tension.
3. Adjust cable tension.
1. Fill tank to proper level with ISOVG32
Hydraulic Oil or Dexron III ATF.
2. Bleed lift per installation instructions.
Cause
1. Blown fuse or circuit breaker.
2. Incorrect voltage to motor.
3. Bad wiring connections.
4. Motor up switch burned out.
5. Overhead limit switch burned out.
6. Motor windings burned out.
1. Open lowering valve.
2. Pump sucking air.
3. Suction stub off pump.
4. Low oil level.
1. Motor running on low voltage.
2. Debris in lowering valve.
3. Improper relief valve adjustment.
4. Overloading lift.
1. Debris in check valve seat.
2. Debris in lowering valve seat.
3. External oil leaks.
1. Air mixed with oil.
2. Air mixed with oil suction.
3. Oil return tube loose.
1. Equalizer cables out of adjustment.
2. Lift installed on unlevel floor.
1. Holes drilled oversize.
2. Concrete floor thickness or holding
strength not sufficient.
1. Latch shafts rusted. (Usually occurs
on outside installations or in high
humidity areas such as vehicle wash
bays.)
2. Latch spring broken.
3. Latch cable needs adjustment.
1. Latch cable is broken.
2. Cable is off sheaves/upper guides.
3. Latch cable is loose.
1. Low oil level.
2. Air in hydraulic lines/cylinder.
TROUBLE SHOOTING
Summary of Contents for SPOA7 Series
Page 10: ...10 NOTES...
Page 11: ...11 NOTES...