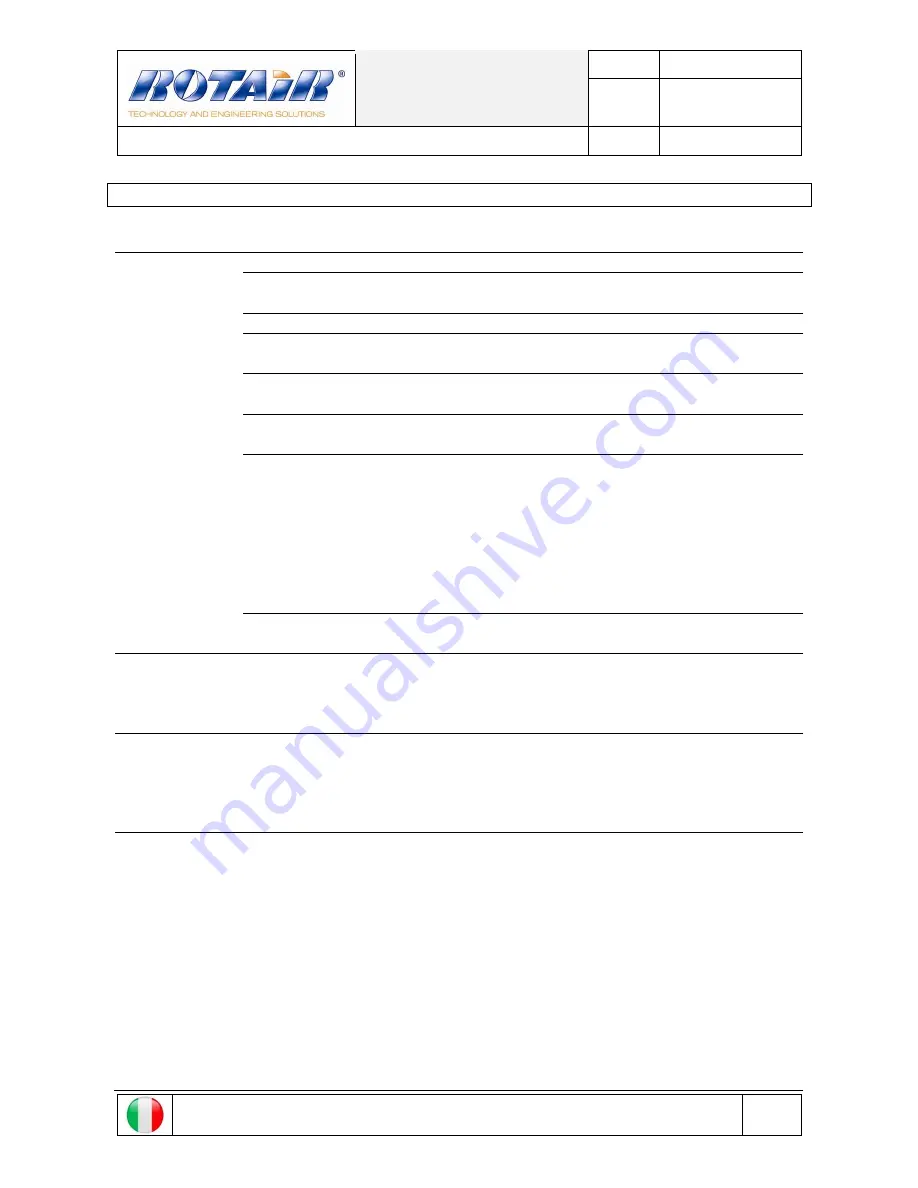
USER'S AND
MAINTENANCE
MANUAL
Date:
22/12/2016
Code
MAN D425T4F ENG
Motor compressor D425T4F
Revision 00
Copyright © 2014, ROTAIR S.P.A. - All rights reserved This manual is intellectual property of ROTAIR S.P.A. Its
full or partial reproduction is forbidden under any form, on any support and by any means, without the written
authorization by ROTAIR S.P.A.
Page
54/57
15 FAULTS AND TROUBLESHOOTING
Abnormal
Cause
Solution
The engine will
not start.
Battery discharged or defective.
Recharge and replace if necessary.
Terminals of the battery cables
oxidized or loose.
Cleaning of the same and their tightening.
No fuel.
Top up the fuel in the diesel tank.
Solenoid faulty fuel.
Seek customer service by the manufacturer of the
engine.
Air in the fuel pipe.
Locate the infiltration by careful verification of all
pipes.
Injection pump defective.
Call in Customer Service by the engine
manufacturer.
Temperature sensors defective.
They are located at:
- Headed-cylinder engine;
- Output air compressor;
- Tank separator.
One at a time, unplug its power cable from the
probes to identify the defective sensor and
replace it. The temperature light on the control
panel should go off.
Starter defective Injectors failures
Call in Customer Service by the engine
manufacturer.
Opening the taps
the motor does
not accelerate.
Control valve of maximum pressure
defective.
Remove the control valve max and accurately
control the spring and the conical seat. If the
defect cannot be repaired, the valve must be
replaced.
The engine
speeds up but no
air come out
Minimum pressure control valve
blocked.
Disassemble and check that the piston is free to
move. Check that the spring is intact. If the defect
cannot be repaired the valve must be replaced.
Reassemble and adjust the minimum pressure
following the instructions in Section 11.3.
The machine
stops suddenly
and can only be
restarted after a
few minutes of
waiting.
A temperature sensor detects a
temperature anomaly and
consequently stops the machine.
Take off one at a time, locate the probe that
determines the stop. If that proves to be placed on
the engine, check the oil level of the motor, the
voltage and the conditions of the alternator belt.
For water-cooled engines, check the coolant
level.
If it turned out to be the probe placed on the
compressor control the level of 'oil in the tank and
if necessary top up;
Check the cooling fan and clean the radiator;
replace the oil filter of the compressor.
If that proves to be positioned on the oil separator
tank, check the oil separator filter following the
Summary of Contents for D425T4F
Page 59: ......
Page 61: ......
Page 63: ......
Page 65: ......
Page 67: ......
Page 69: ......
Page 71: ......
Page 73: ......
Page 75: ......
Page 77: ......
Page 79: ......
Page 81: ......
Page 83: ......
Page 85: ......
Page 87: ......
Page 89: ......
Page 91: ......
Page 93: ......
Page 95: ......
Page 97: ......
Page 99: ......