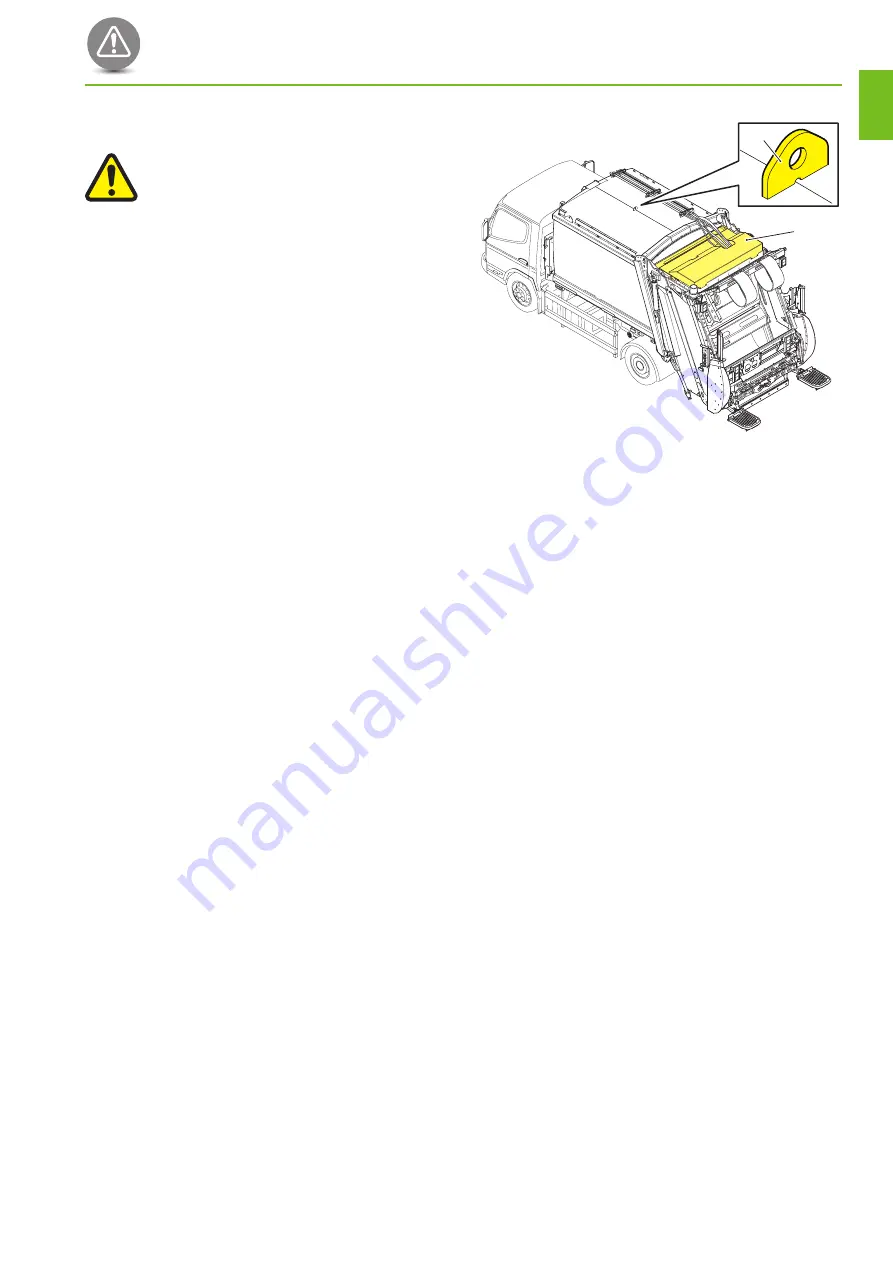
2.6
working at high level
wARNINGS:
FAILuRe TO OBSeRVe THe FOLLOwING
PReCAuTIONS MAY ReSuLT IN INJuRY OR
deATH.
dO NOT uNdeR ANY CIRCuMSTANCe
wALK ON OR LOAd THe PLASTIC TAILGATe
ROOF COVeRS (See FIG. 2-1, 1). THeSe ARe
NOT LOAd-BeARING STRuCTuReS.
SAFeTY HARNeSS ATTACHMeNT LuGS
(SHAL) SHOuLd NOT uNdeR ANY
CIRCuMSTANCeS Be uSed AS LIFTING
POINTS TO RAISe THe BOdY.
High level components and equipment mounted on
the roof of the body and tailgate are generally located
in positions accessible from the side or rear of the
vehicle.
Where possible, any maintenance (inspection,
replacement, repairs) of high level components and
equipment mounted on the body or tailgate should
be carried out using suitable access platforms to
either side or rear of the vehicle. Access platforms
should be used in compliance with all prevailing Health
and Safety Regulations, Workshop Regulations and
Workshop Codes of Practice.
Where components cannot be accessed from the side
or rear of the vehicle and it becomes necessary to
work on top of the body roof or tailgate, always wear
an approved safety harness connected to a Safety
Harness Attachment Lug (see Fig. 2‑1, 2) in accordance
with all prevailing safe systems of work, Health and
Safety Regulations, Workshop Regulations and
Workshop Codes of Practice.
Safety Harness Attachment Lugs (SHAL) are primarily
designed for the use of Ros Roca manufacturing,
production and service personnel when working at
height on vehicle roofs in line with risk assessments
and safe systems of work conducted at Ros Roca.
Customers may use the Safety Harness Attachment
Lugs only if they have conducted necessary risk
assessments and prescribed subsequent safe systems
of work based on their own activities.
If in doubt, contact your local Health and Safety
Officer.
If access to components under the covers is required,
remove them first as described in the appropriate
sections of the Olympus Mini Workshop Manual.
4639-OM1-R-GB-G1
1
2
Fig. 2-1
Olympus Mini roof
1. Tailgate roof covers.
2. Safety Harness Attachment Lug (SHAL).
HeALTH ANd SAFeTY
2‑5
OM1R-SM-GB01R
2
Summary of Contents for Olympus Mini
Page 2: ......
Page 6: ...Contents iv OM1R SM GB01R This page intentionally left blank ...
Page 8: ...Introduction 1 2 OM1R SM GB01R This page intentionally left blank 1 ...
Page 10: ...Introduction 1 4 OM1R SM GB01R This page intentionally left blank 1 ...
Page 12: ...Health and safety 2 2 OM1R SM GB01R This page intentionally left blank 2 ...
Page 26: ...Daily checks 3 2 OM1R SM GB01R This page intentionally left blank 3 ...
Page 56: ...Hydraulic system oil level 4 2 OM1R SM GB01R This page intentionally left blank 4 ...
Page 64: ...Cleaning 5 2 OM1R SM GB01R This page intentionally left blank 5 ...
Page 70: ...Scheduled maintenance 6 2 OM1R SM GB01R This page intentionally left blank 6 ...
Page 98: ...General specification data 8 2 OM1R SM GB01R This page intentionally left blank 8 ...
Page 102: ...General specification data 8 6 OM1R SM GB01R This page intentionally left blank 8 ...