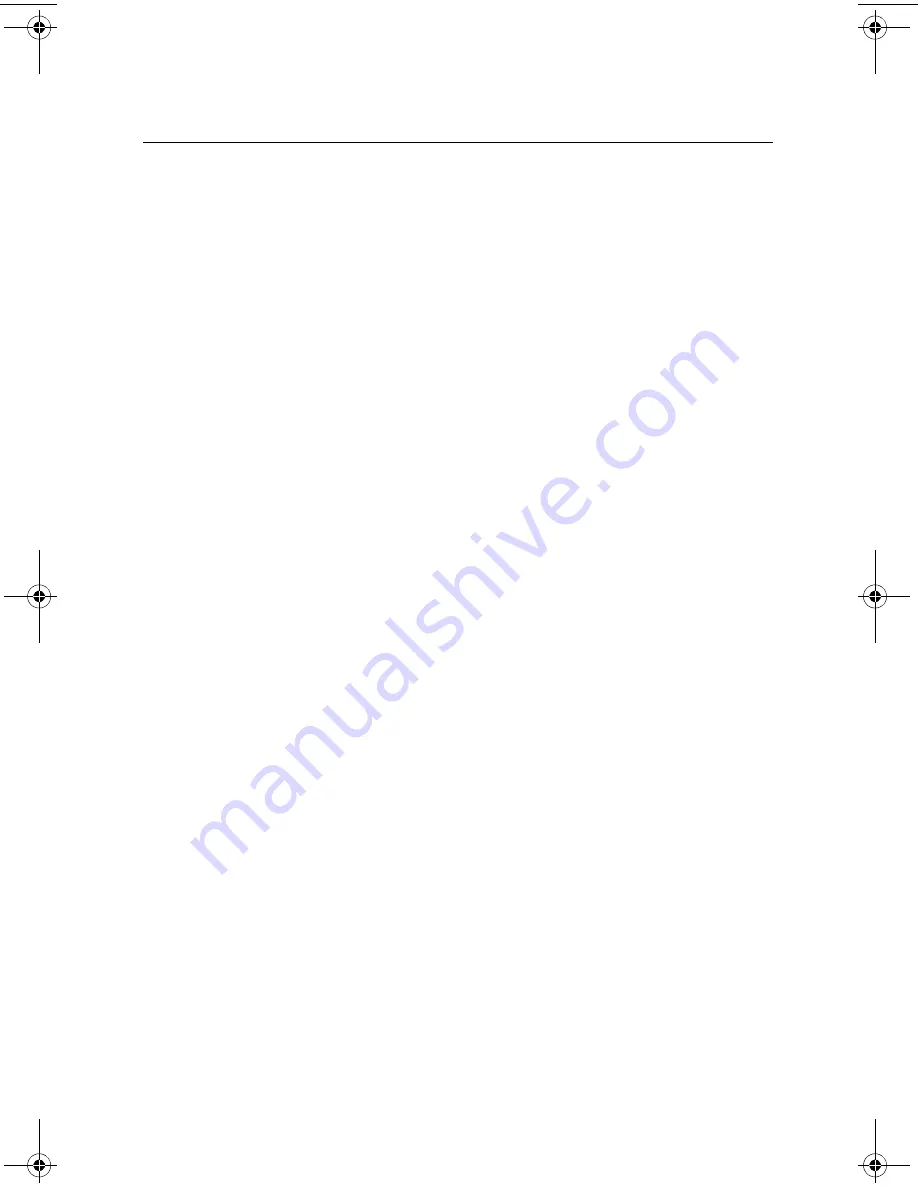
Quick Installation Guide
00825-0100-4750, Rev BA
June 2009
Rosemount 8750WA
15
S
TEP
6: W
IRING
S
TEP
6: W
IRING
Conduit Ports and Connections
Both the sensor and transmitter junction boxes have ports for
1
/
2
-inch NPT conduit
connections with optional CM20 or PG 13.5 connections available. These connections
should be made in accordance with local or plant electrical codes. Unused ports should be
sealed with metal plugs. Proper electrical installation is necessary to prevent errors due to
electrical noise and interference. Separate conduits are not necessary for the coil drive and
electrode cables, but a dedicated conduit line between each transmitter and sensor is
required. Shielded cable must be used for best results in electrically noisy environments.
When preparing all wire connections, remove only the insulation required to fit the wire
completely under the terminal connection. Removal of excessive insulation may result in an
unwanted electrical short to the transmitter housing or other wire connections.
For flanged sensors installed into an application requiring IP68 protection, sealed cable
glands, conduit, and conduit plugs that meet IP68 ratings are required.
Option Codes SA, SB, SC, SD, SE and SF provide a pre-wired potted and sealed junction
box to prevent the ingress of water. These options still require the use of sealed conduits to
meet IP68 protection requirements.
Conduit Cables
Run the appropriate size cable through the conduit connections in your magnetic flowmeter
system. Run the power cable from the power source to the transmitter. Run the coil drive
and electrode cables between the flowmeter sensor and transmitter. Prepare the ends of the
coil drive and electrode cables as shown in Figure 15. Limit the unshielded wire length to
1-inch on both the electrode and coil drive cables. Excessive lead length or failure to
connect cable shields can create electrical noise resulting in unstable meter readings.
• Installed signal wiring should not be run together and should not be in the same cable
tray as AC or DC power wiring.
• Device must be properly grounded or earthed according to local electric codes.
• Rosemount combination cable model number 08712-0752-0001 (ft) or
08712-0752-0003 (m) is required to be used to meet EMC requirements.
8750WA32 Wiring Connections
Powering the Transmitter
This wiring section covers supplying power to the transmitter, the connections between the
sensor and the transmitter, and the 4-20 mA loop.
Connect power to the transmitter according to local electrical requirements. For AC power
applications (90-250 VAC, 50-60 Hz) connect AC Neutral to terminal 9 (AC N/L2) and
connect AC Line to terminal 10 (AC/L1). For DC power applications, connect negative to
terminal 9 (DC -) and positive to terminal 10 (DC +). Units powered by 12-42 V DC power
supply may draw up to 1 amp of current. Follow the supply wire and disconnect
requirements below:
4750RevBAQIG.fm Page 15 Thursday, July 16, 2009 3:52 PM
Summary of Contents for 8750WA
Page 37: ...Quick Installation Guide 00825 0100 4750 Rev BA June 2009 Rosemount 8750WA 37 ...
Page 38: ...Quick Installation Guide 00825 0100 4750 Rev BA June 2009 Rosemount 8750WA 38 ...
Page 39: ...Quick Installation Guide 00825 0100 4750 Rev BA June 2009 Rosemount 8750WA 39 ...
Page 40: ...Quick Installation Guide 00825 0100 4750 Rev BA June 2009 Rosemount 8750WA 40 ...